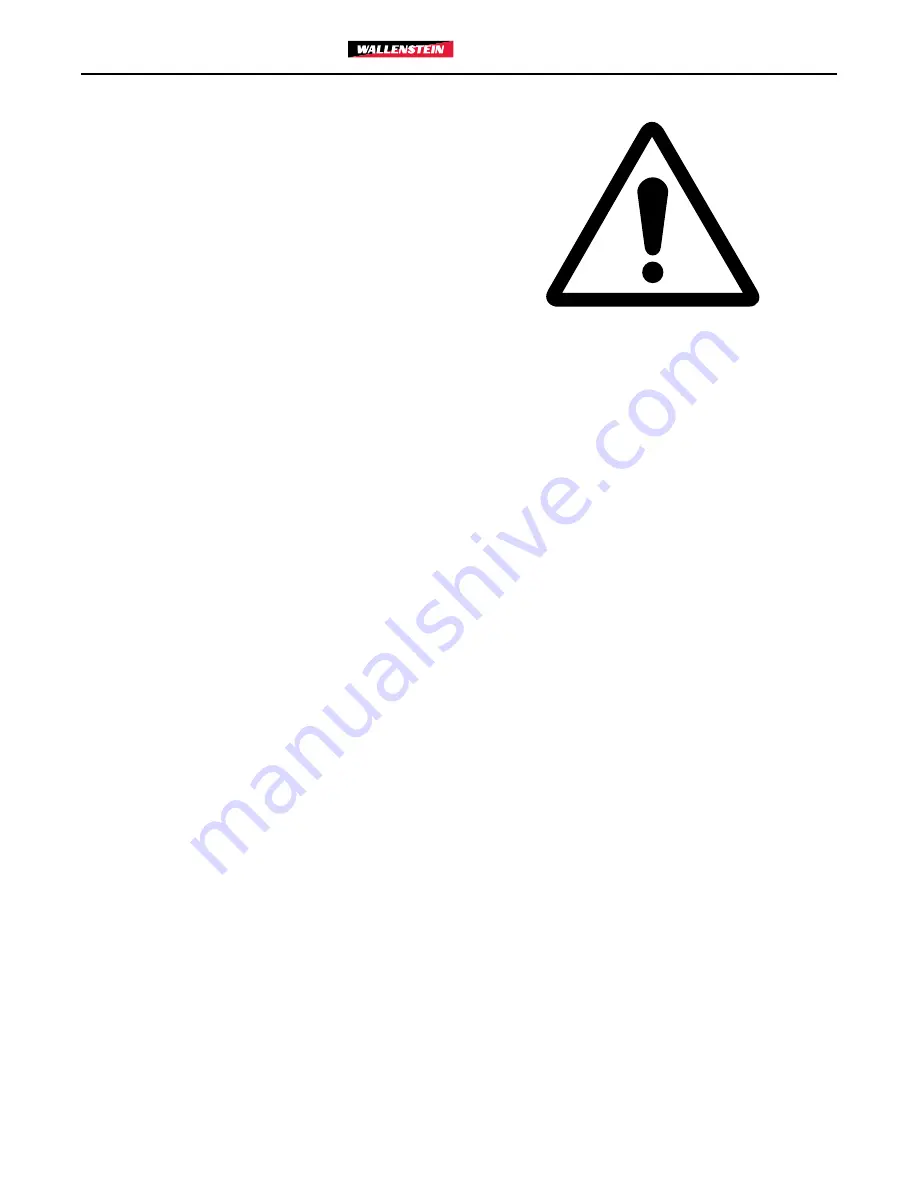
7
BXTR6438
2. Safety
2.1 Safety Alert Symbol
This Safety Alert Symbol means:
ATTENTION! BE ALERT!
YOUR SAFETY IS INVOLVED!
The
Safety Alert Symbol
identifies important safety
messages on the Wallenstein wood chipper and in
the manual. When you see this symbol, be alert to
the possibility of personal injury or death. Follow the
instructions in the safety message.
2.2 Signal Words
The signal words
DANGER
,
WARNING
and
CAUTION
determine the seriousness level of the warning
messages in this manual. The appropriate signal word
for each message in this manual has been selected
using the following guidelines:
DANGER –
Indicates an imminently hazardous situation that,
if not avoided,
will
result in death or serious injury.
This signal word is to be limited to the most extreme
situations typically for machine components which, for
functional purposes, cannot be guarded.
WARNING –
Indicates a potentially hazardous situation that, if not
avoided,
could
result in death or serious injury, and
includes hazards that are exposed when guards are
removed. It may also be used to alert against unsafe
practices.
CAUTION –
Indicates a potentially hazardous situation that, if not
avoided,
may
result in minor or moderate injury. It may
also be used to alert against unsafe practices.
IMPORTANT
– To avoid confusing equipment
protection with personal safety messages, a signal
word IMPORTANT indicates a situation that if not
avoided, could result in damage to the machine.
2.3 Why SAFETY is Important
Three Big Reasons:
•
Accidents Disable and Kill
•
Accidents Cost
•
Accidents Can Be Avoided
The policy of Wallenstein Equipment Inc. is to produce
products that are safe and reliable. However, even
when using well-engineered equipment, there is
always an element of risk. To minimize the risks
and promote safety at all times, this section of the
operator’s manual details a number of safety rules that
must always be followed and obeyed.
YOU
are responsible for the SAFE operation and
maintenance of your Wallenstein Trailer Wood Chipper.
YOU
must ensure that you and anyone else who
is going to use, maintain or work around the wood
chipper be familiar with the operating and maintenance
procedures and related
safety
information contained
in this manual. This manual provides good safety
practices that should be followed while using the wood
chipper.
Remember,
YOU
are the key to safety. Good safety
practices not only protect you but also the people
around you. Make these practices a working part of
your safety program. Be certain that
EVERYONE
using
this equipment is familiar with the recommended use
and maintenance procedures and follows all the safety
precautions.
Do not risk injury or death by ignoring good safety
practices.