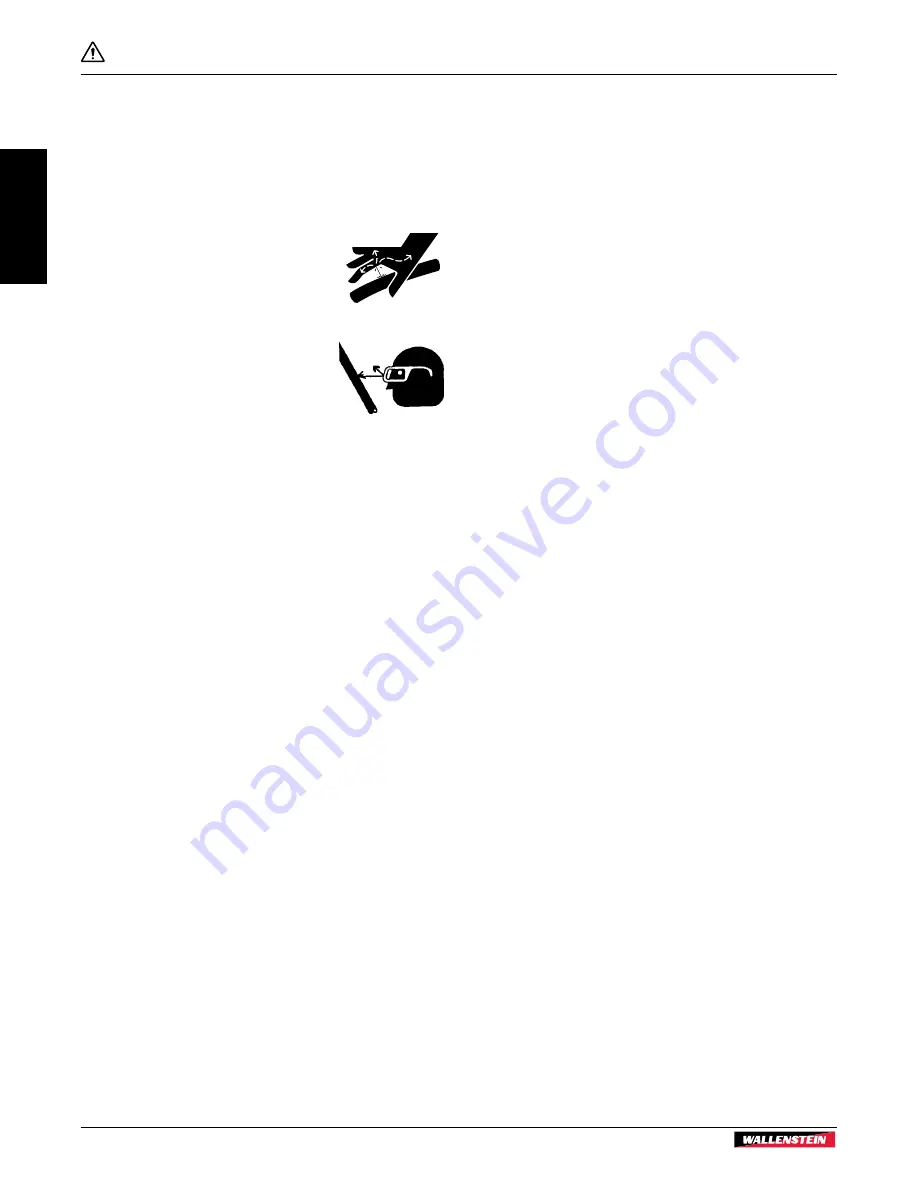
2.6.1 Hydraulic System Safety
•
Make sure that all the components in the hydraulic system
are kept clean and in good condition.
•
Make sure all components are tight, and that lines, hoses
and couplings are not damaged before applying pressure to
the system.
•
Do not use a hand to check for hydraulic
oil leaks. Hydraulic fluid escaping under
pressure can penetrate the skin causing
serious injury. Use a piece of cardboard.
•
Wear proper hand and eye protection
when searching for a high-pressure
hydraulic leak.
•
Seek medical attention immediately if injured by a
concentrated high-pressure stream of hydraulic fluid.
Serious infection or toxic reaction can develop from
hydraulic fluid piercing the skin surface.
•
Do not attempt any makeshift repairs to the hydraulic lines,
fittings or hoses by using tape, clamps or cements. Doing
so can cause sudden failure and create a hazardous and
unsafe condition.
•
Relieve pressure on the hydraulic system before working
it. The hydraulic system operates under extremely high
pressure.
•
Replace any hydraulic hose immediately that shows signs
of swelling, wear, leaks or damage before it bursts.
•
Check to make sure hydraulic hoses are not worn or
damaged and are routed to avoid chafing.
•
Never adjust a pressure relief valve or other pressure-
limiting device to a higher pressure than specified.
Safety
CT16 / CT24
Trailer Firewood Conveyor
Safety
10
Summary of Contents for CT162
Page 43: ......
Page 44: ...www wallensteinequipment com ...