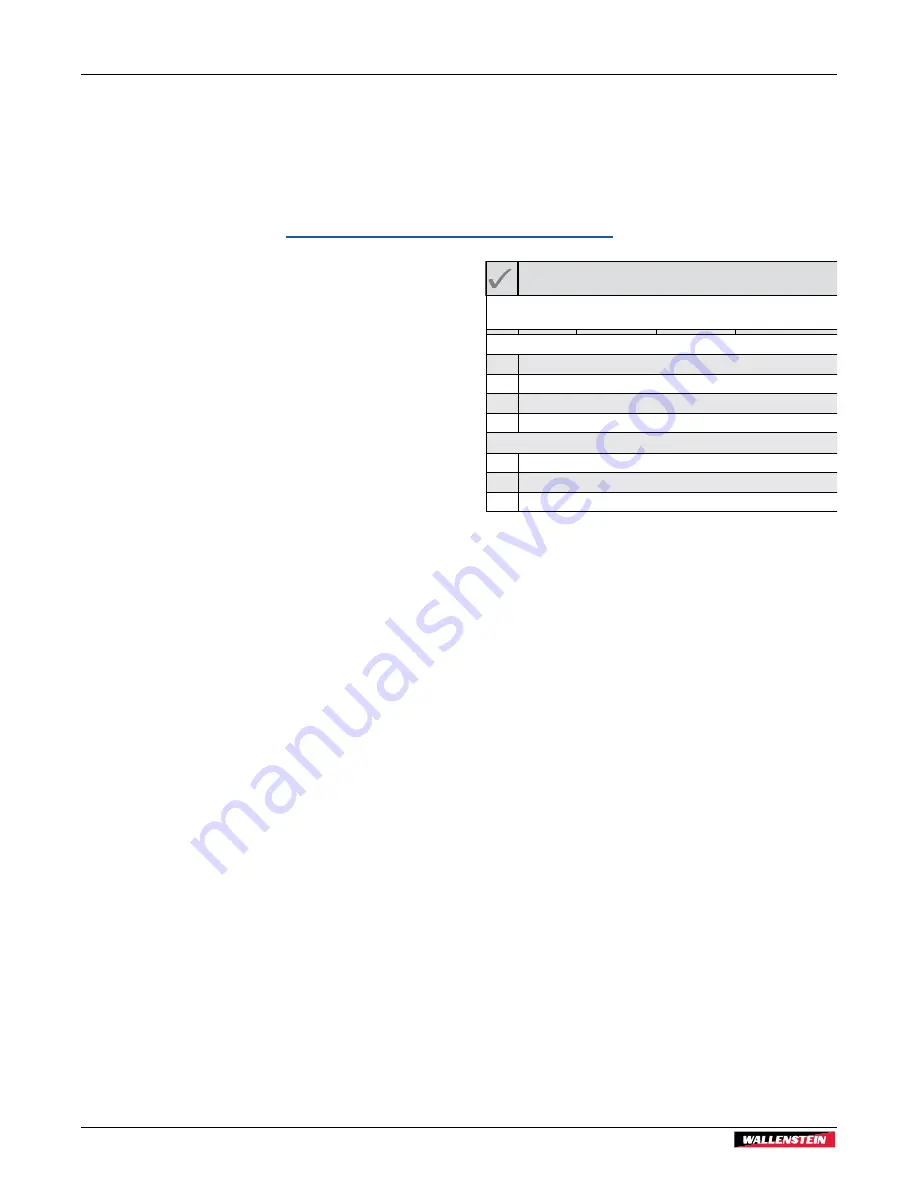
Introduction
WX310, WX320, WX330
3-point Hitch Wood Splitter
4
WALLENSTEIN
WX310, WX320, WX330, Three-point Hitch Wood Splitters
Pre-delivery Inspection
Inspect for damage from shipping. Immediately contact the
shipping company if damage is found.
Three-point Hitch Wood Splitter
Hydraulic Valve Control Function
Hydraulic Cylinder Function
All fasteners are Tight
Hydraulic Connections are tight
Safety Checks
All Safety Decals Installed
Guards and Shields Installed and Secured
Review Operating and Safety Instructions
_________________________________________
Customer’s Name
_________________________________________
Contact Name
_________________________________________
Dealer Name
(_________)_______________________________
Phone Number
_________________________________________
Serial Number
__________ /__________ /__________
Delivery Date
I have thoroughly instructed the buyer on the equip-
ment care, adjustments, safe operation and applicable
warranty policy and reviewed the manual.
_________________________________________
Dealer’s Rep. Signature
__________ /__________ /__________
Date
The product manuals have been received by me and
I have been thoroughly instructed as to care, adjust-
ments, safe operation and applicable warranty policy.
_________________________________________
Owner's Signature
__________ /__________ /__________
Date
1.2 Delivery Inspection Report
To activate warranty, register your product online at
http://www.wallensteinequipment.com
Summary of Contents for WX310
Page 34: ...www wallensteinequipment com ...