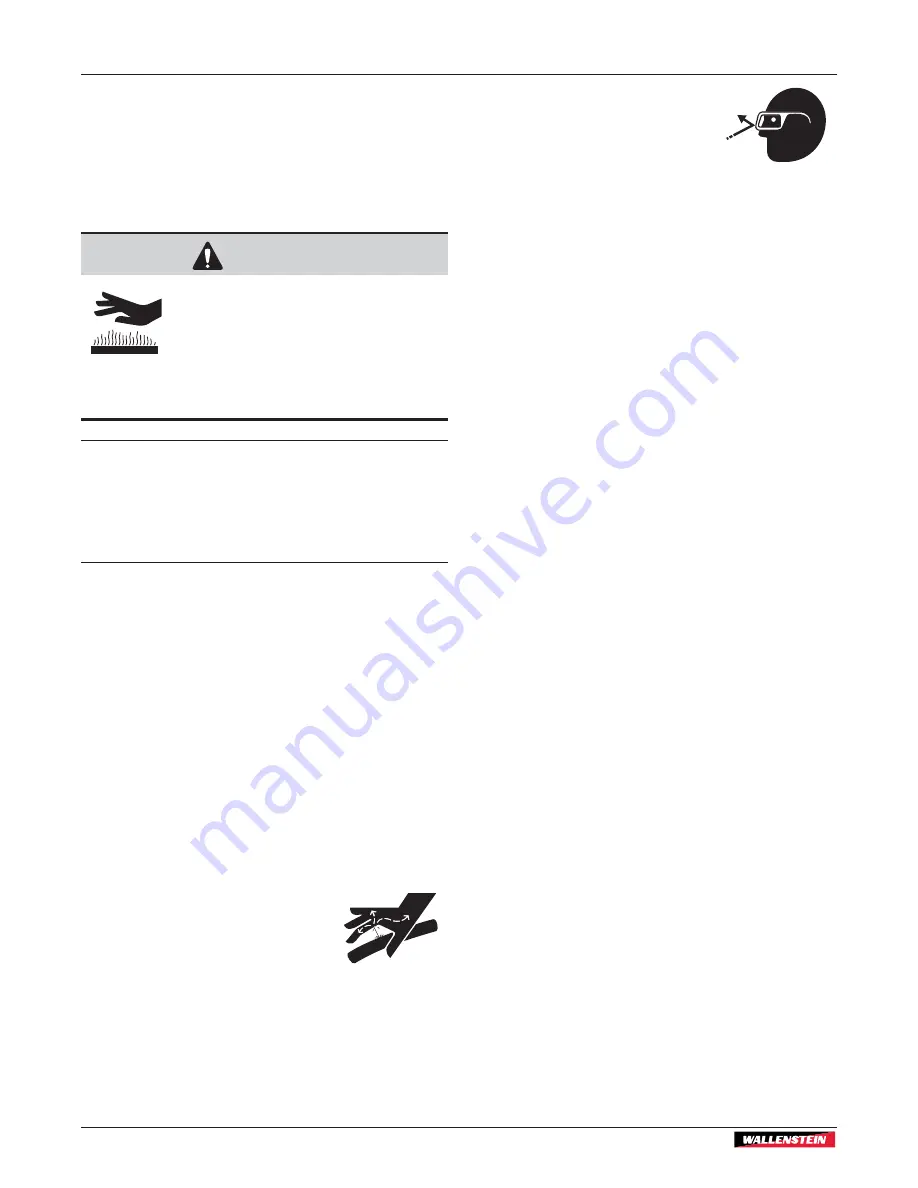
Service and Maintenance
WX900 Series
Log Splitter
38
9.5 Hydraulic System Maintenance
The hydraulic system controls the splitting wedge and log lifter
shelf.
9.5.1 Hydraulic System Maintenance
Safety
CAUTION!
Risk of burns to exposed skin.
Hydraulic fluid gets hot during
operation, which makes hoses,
lines, and other parts hot as well.
Wait for the fluid and components to
cool before starting maintenance or
service.
IMPORTANT! Optimal hydraulic fluid temperatures
are between 120° F and 140° F (50° C and 60° C). If the
hydraulic fluid temperature is higher than 180° F (82° C),
it can cause seal damage and degrade the hydraulic fluid.
High hydraulic fluid temperatures often indicate that there is
a problem.
For more information, see
Hydraulic System Operation Safety on
•
Make sure that all hydraulic system components are kept
clean and in working condition.
•
Relieve pressure on the hydraulic system before working
with it. The hydraulic system operates under extremely high
pressure.
•
Before applying pressure to the hydraulic system, make
sure that all the connections are tight, and the hoses and
fittings are not damaged.
•
Replace hydraulic hoses that show signs of swelling,
wear, leaks, or damage. A swollen, worn, damaged, or
leaking hose can burst and cause a hazardous and unsafe
condition.
•
High-pressure hydraulic fluid leaks:
• Do not use your hand to check
for hydraulic fluid leaks. Hydraulic
fluid that leaks under pressure
can penetrate the skin and cause
serious injury or death. Use a piece
of cardboard, wood, or plastic
to check for leaks. Put on heavy
gloves.
• Put on the correct eye protection
when doing an inspection for a
high-pressure hydraulic leak.
• Get medical attention immediately if you are injured by
a concentrated high-pressure stream of hydraulic fluid.
Serious infection or a toxic reaction can occur after
hydraulic fluid pierces the skin.
•
Do not make any temporary repairs to the hydraulic hoses
or fittings. Do not use tape, clamps, or cements to attempt
a repair. This can cause sudden failure and create a
hazardous and unsafe condition.
•
Do not bend or strike high-pressure hoses or reinstall them
in a bent or damaged condition.
•
Make sure that hydraulic hoses are routed to avoid chafing.
•
Never adjust a pressure relief valve or other pressure-
limiting device to a pressure that is higher than the
specified rating.
Summary of Contents for WX900 Series
Page 48: ...WallensteinEquipment com...