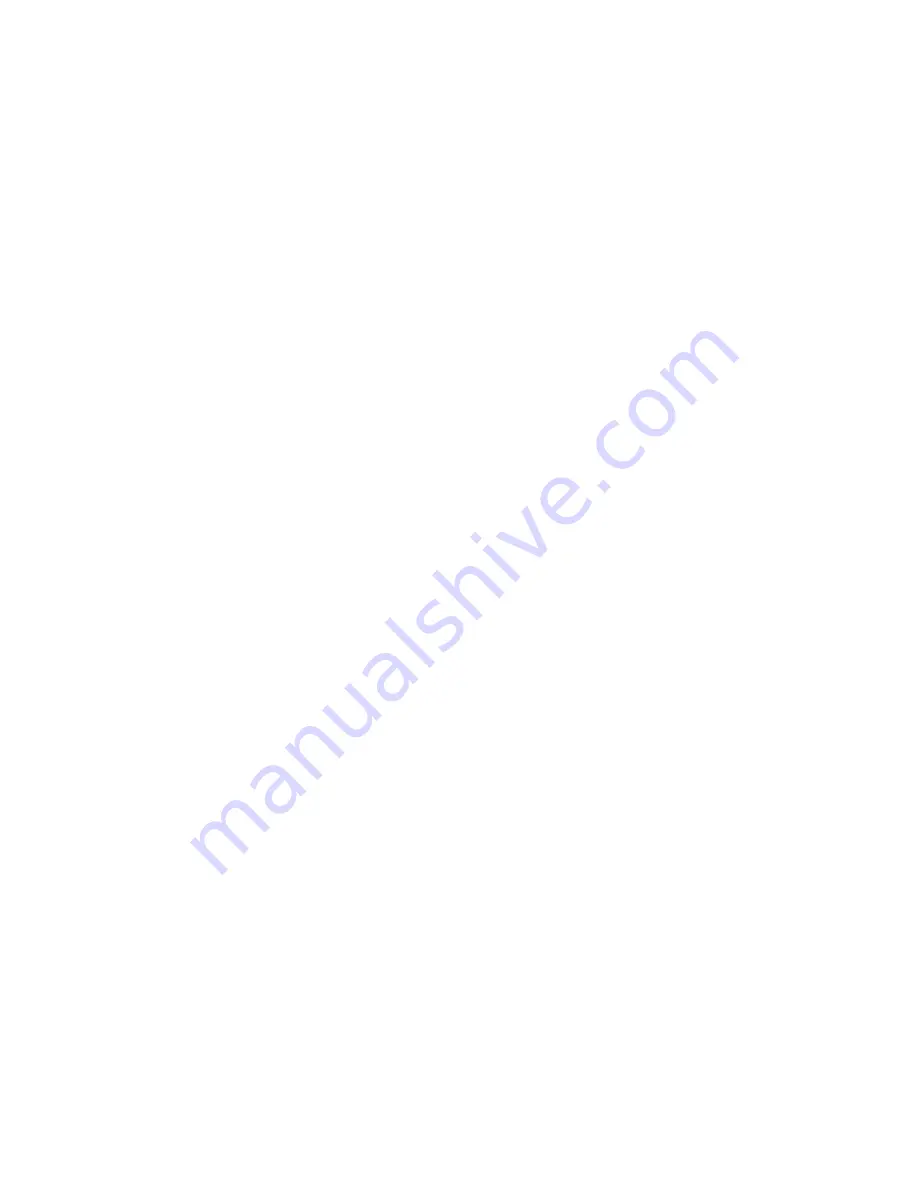
19
Machine Brushes
Should be checked to make sure there is no abnormal wear present (this should be checked at least
once a week if used frequently). If the brush has worn more than 2/3 of the original length, the brushes
should be changed. Failure to do so may cause damage to the machine.
Magnetic base
Before every operation the magnetic base should be checked to make sure that there is no damage
present. An uneven magnet base will cause the magnet not to hold as efficiently and may cause injury to
the operator.
Adjustment of slide and bearing bracket alignment.
An essential requirement of the machine is that the slide can move in a smooth and controlled manner,
free of lateral movement and vibration.
This situation can be maintained by periodic adjustment of the slide and is accomplished in the following
manner:
1.
Place the machine in an upright position and, by means of the capstan, raise the slide to its
highest position. Clean the brass gib strips and apply a small amount of light machine oil to the
wear surfaces.
2.
Now lower the slide back to its lowest position. Bring the slide into the center of the dovetail
slide housing and loosen screws thus allowing free movement of the arbor support bracket.
3.
Commencing with the middle screws, gently feed in all the screws until slight resistance is
encountered.
4.
Operate the slide up and down a few times to test the movement and make any further
necessary adjustments. Try to ensure that all the screws are exerting a uniform pressure on the
slide from top to bottom. A perfectly adjusted slide will operate freely up and down without any
sideways movement.
5.
Now raise the slide to its highest position. Slightly undo the arbor bearing bracket and, using
fingers only, tighten the screws.
6.
Place the machine on a steel plate, connect to power supply and switch on the magnet. Start up
the motor. If the arbor is incorrectly aligned, the arbor support bracket will be seen to oscillate.
Make any necessary further adjustments to the bracket to ensure correct alignment of the
spindle and finally tighten the screws using a spanner. Lastly tighten the arbor bearing bracket.
Check machines grease.
The gearbox grease should be checked once a month to ensure all moving components are covered to
prevent wear. The grease should be changed at least once a year to ensure you gain the best usage from
your machine.
Check Armature of the machine.
This should be checked at least once a month to check that there are no visual signs of damage to the
body or to the commutator. Some signs of wear will be seen on the commutator over a period of time
but this is normal (this is the part that comes into contact with the brushes) however, if there are any
signs of abnormal damage the part should be replaced.
Summary of Contents for ICECUT 250 Auto
Page 1: ...ICECUTTM 250 Auto Magnetic Drilling Unit 39 D 252 120V This Machine is CSA UL certified...
Page 21: ...21...
Page 22: ...22 ICECUTTM 250 Auto Perceuse base magn tique 39 D 252 120V Cette machine est certifi e CSA...
Page 50: ...50 7A OPERACI N DEL PANEL DE CONTROL...
Page 63: ...63...
Page 64: ...64...
Page 71: ...71...