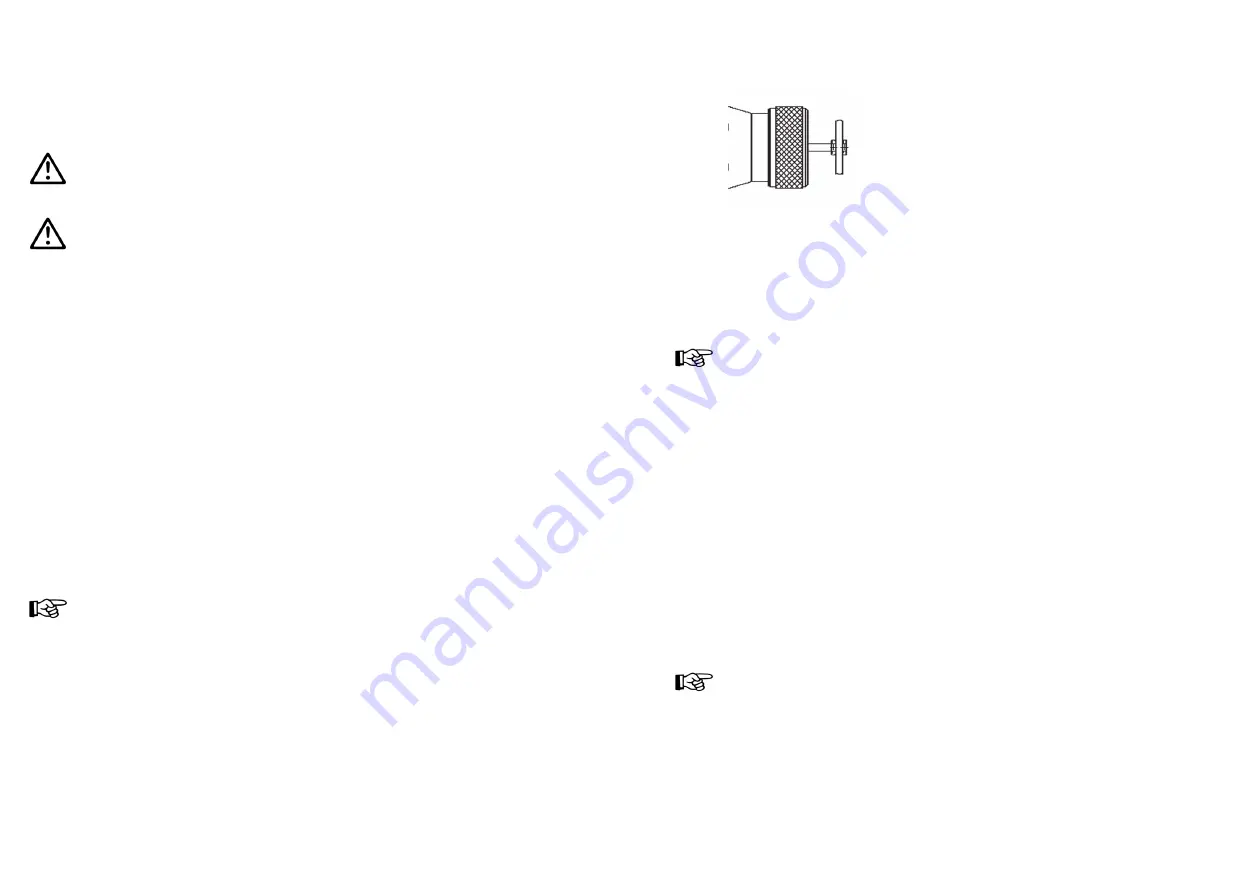
39
38
Clean the spray gun
•
prior to each change of the spraying medium.
•
at least once a week.
•
as often as may be required by the spraying medium handled and the resultant
degree of fouling.
Caution
Never immerse the spray gun in solvent or any other cleaning solution. The functio-
nal reliability and efficiency of the gun can otherwise not be guaranteed.
Caution
Do not use any hard, pointed or sharp-edged objects when cleaning the spray gun.
Any damage of the precision-made parts are likely to affect your spraying results.
1. Dismantle the spray gun in accordance with
5.6 Retooling the Spray Gun.
2. Use a soft brush together with a compatible cleaning sulotion to clean the air cap
and nozzle.
3. Clean the remaining parts and the spray gun body with a suitable cloth and
cleaning solution.
4. Apply a thin film of the appropriate grease to the:
•
sealing collar of the piston
•
O-ring of the piston
•
material control needle
•
needle spring
Make sure to use a non-acidic, non-resinogenic grease and a soft brush. The spray
gun is then reassembled in reverse order.
6.3
Cleaning - Routine
The spray gun need not necessarily be dismantled for cleaning if and when the
spraying medium is changed in regular intervals or upon termination of work (depen-
ding on the material used).
Notice
Clean and lubricate the spray gun frequently in accordance with Chapter
6.2 Cleaning - Complete
. This will ensure functional reliability of the spray gun.
The following requirements must be met before the routine cleaning work can be
performed:
1. The material tank must be clean and then be filled with a compatible cleaning
solution. Material pressure has to be available at the spray gun. The cleaning
solution should not be sprayed.
2. Take the spray gun into operation (see
5.2 Starting the Spray Gun
).
3. Do not stop the spray gun until clear cleaning solution emerges from the nozzle.
The material supply of the series PILOT WA 7XX
can be manually released so that
it is not necessary to operate the complete spraying system.
All pressures should then be removed from the complete spraying system until the
next operation.
7
Repairs / Replacements
Warning
Prior to any repairs / replacements: Make sure that the spray gun is in unpressurized
condition, i.e. all air and material inputs must be shut off - if not, imminent risk of
injury.
Notice
Please use the drawing at the beginning of these operating instructions to perform
the following procedures.
7.1
Replacement of defective Needle Packing
1. Remove all pressures from the gun.
2. Unscrew the 4 mounting screws in (item 6) from the front body in (item 7) (width
over flats of hex. nut 3).
3. Pull the front body in (item 7) off the piston casing in (item 18).
4. Unsrew the packing screw into (item 15) from the front part in (item 7) (screw
driver).
5. Remove the packing spring in (item 14) (replace, if damaged) and the pressure
ring in (item 13) from the threaded socket.
6. Pull out the needle seal packing (item 12) with an auxilliary tool. Use a strong
wire on which one end is bent making a small hook.
7. Lubricate the new needle seal with non-acidic, non-resinogenic grease
8. Install the new needle seal in the gun body.
Installation of the remaining parts is performed in reverse order.
Notice
Never reinstall a used needle seal packing (item 12) as otherwise the functional
sealing reliability of the spray gun will suffer.
7.2
Replacement of Nozzles, Needles, Springs and Seals
Dismantle the spray gun in accordance with Chapter
5.6 Repalcement of Material
Control Nozzle and Needle
, if the following components have to be replaced:
•
Material Nozzle
•
Pressure of the Piston
1. Pull back the draw bar of the spray gun. The mate-
rial inlet is now open and both material duct and
material nozzle will be cleaned.
2. Do not let go of the drawbar until clear cleaning
solution emerges from the nozzle.