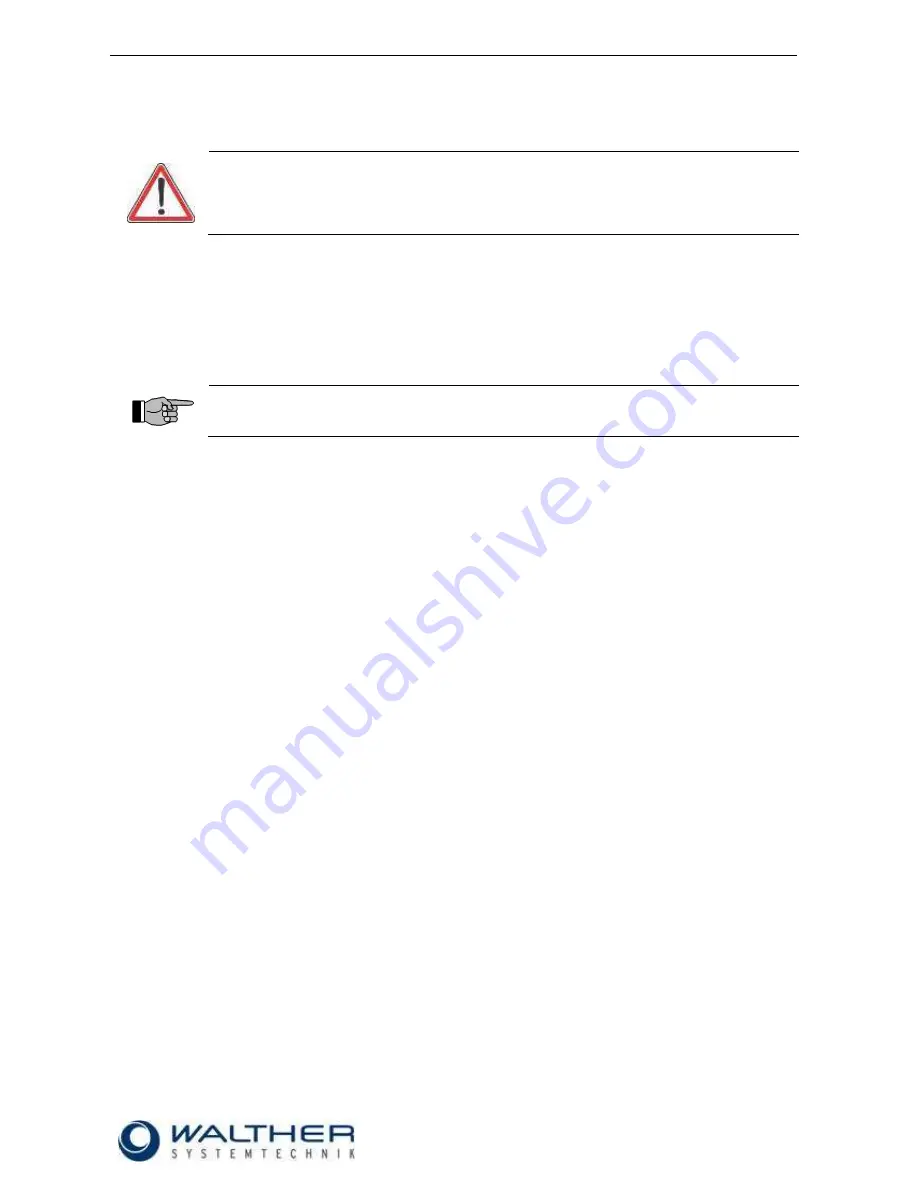
Rev. 1.2
Assembly Instructions - MPP-02 Micro Point Pulse Valve
Page 11 of 20
Walther Systemtechnik GmbH
– D 76726 Germersheim
phone: +49 (0)7274-7022-0 fax: +49 (0)7274-7022-91
http://www.walther-2000.de
– info@walther-2000.de
7 Maintenance and Repair
7.1 General Information
CAUTION
Before starting any maintenance or repair work, ensure that all air-operated tools are
depressurized and disconnected from the air supply.
Before opening the spray valve it must be disconnected from the air and fluid supply.
Otherwise, ejected components can cause injuries
The
MPP-02
Micro Point Pulse Valves are high precision tools. Always keep clean and observe minimum
instructions to maintain a long life of the valve. We recommend lubricating moveable parts regularly and
greasing threads, especially the nozzle threads, when replacing or cleaning the nozzle. Always use clean
and filtered material only. The control air must also be clean and should be slightly oiled, if necessary.
Maintenance also depends on the individual operating conditions and the type of media used.
7.2 Cleaning
IMPORTANT
Only use soft brushes for outside cleaning of the nozzle tips. Never use metal tools with
sharp edges.
Wash incomplete device thoroughly after use to remove residues and dirt; especially if needle (5.0), sealing
screw (4.0) or nozzle (1.0) are to be exchanged
.
7.3 Replacing Needle (5.0) and Nozzle (1.0)
Completely unscrew ratchet needle lock (7.0) and nozzle (1.0). Pull out needle spring (6.0) and carefully
push out the needle (5.0) towards the nozzle end. Slightly grease replacement parts and re-assemble them
in reverse order. Do not reuse old needles. Even slightly dirty needles and needle shafts can cause leakage
in the special form gasket (3.3).
7.4 Replacing Sealing Screw (4.0)
Completely unscrew ratchet needle lock (7.0) and nozzle (1.0). Pull out needle spring (6.0) and carefully
push out the needle (5.0) towards the nozzle end. Then unscrew the sealing screw (4.0) from the thread with
a screwdriver. Since the outer O-ring (3.1) prevents the sealing screw from falling through the mounting
thread of the valve body (2.0), it is necessary to push the sealing screw together with O-ring (3.1) carefully
backwards through the thread using a thin strip of metal (0.5
– 1.0 mm) which you push between the recess
in the body and flat in front of the front end of the sealing screw. You can then take the sealing screw out of
the enclosure.
7.5 Replacing Gaskets and O-rings
If a complete sealing screw (4.0) with an inserted gasket set (3.0) is not available as a replacement, the old
gaskets must be removed and replaced with new ones. In order to do so, the sealing screw must be thor-
oughly cleaned so that no particles of the previous spraying fluid impair the installation of the new gaskets.
The O-ring seats should be lightly greased with a lubricant (technical Vaseline). First insert O-ring (4.2) into
the rear hole of the sealing screw until it reaches the end. Then insert O-ring (3.1) into the outermost groove.
Insert the special form gasket (3.3) into the front seat. Since this form gasket is not symmetrical, the side
with the larger outer diameter must be inserted facing forwards, i.e. it must point in the direction of the nozzle
after the complete sealing screw has been installed. Lightly grease the sealing screw (4.0) and insert it back
into the valve body (2.0). Use a screwdriver to carefully push it through the mounting thread together with the
outer O-ring (3.1) without twisting it. Then screw the sealing screw into the thread (gently tighten).
Do not use any metallic or sharp-edged aids or tools when you insert the O-rings and the special form gas-
ket. Despite all its outstanding sealing qualities, the special form gasket is a sensitive precision component,
which cannot tolerate impacts or pressure.