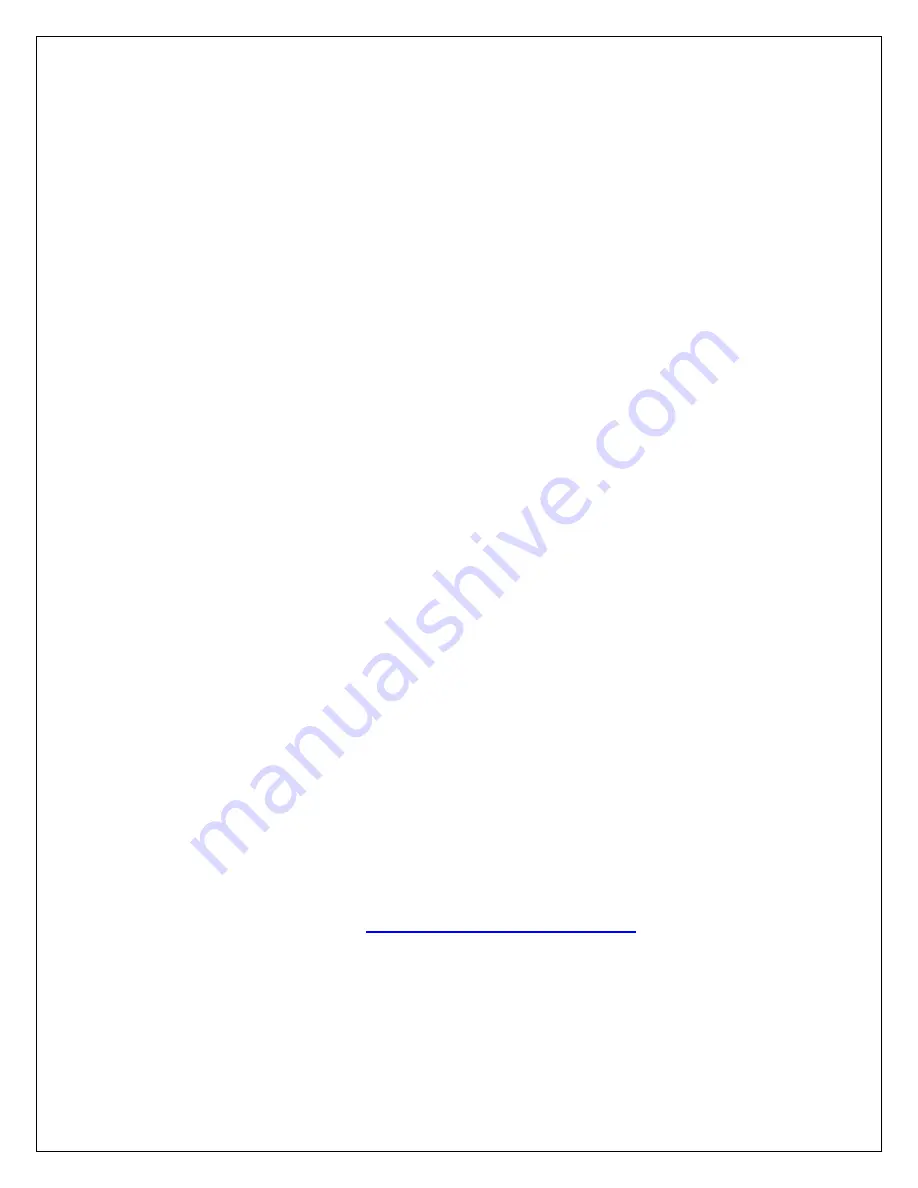
42
7 Year Limited Warranty
Williams & Hussey Machine Co., Inc. warrants this molder for a
period of seven years from the original date of purchase.
This warranty
covers
any original parts that were improperly
manufactured and any malfunctions due to improper original
factory assembly of the molder.
The warranty
does not cover
damage due to; modifications,
misuse, improper maintenance, normal wear, or wood jams.
If your machine fails during the warranty period, contact Williams
& Hussey at
1 800 258 1380
for a return authorization. Once you
receive your authorization to return your machine or a part of your
machine you must return it to us with the freight
prepaid.
You
must also include a
proof of purchase
with the machine.
The warranty does not extend to anyone except the first purchaser.
The warranties set forth above are in lieu of all other warranties
expressed.
WILLIAMS & HUSSEY MACHINE CO.
70 POWERS STREET
MILFORD NH 03055
info@williamsnhussey.com
1 800 258 1380
FAX 603 732 4048