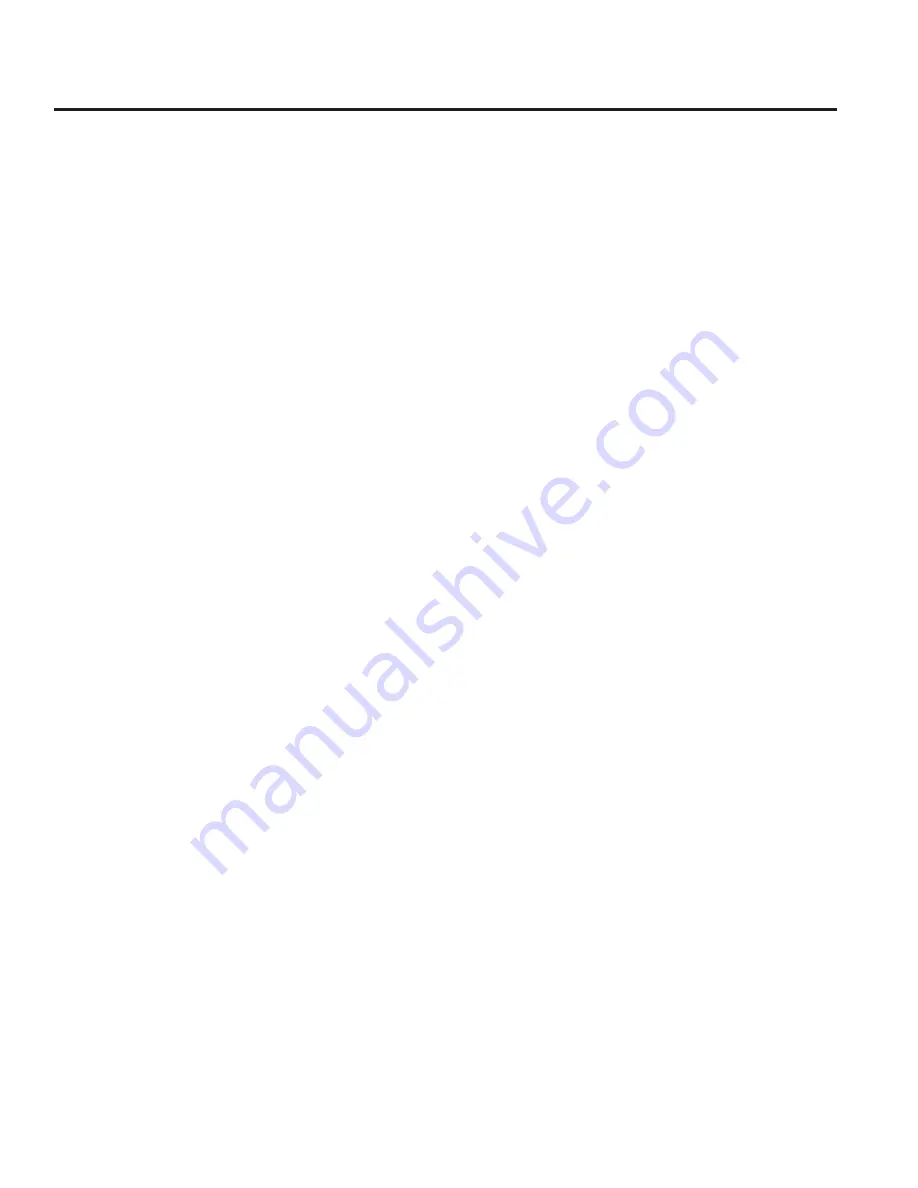
6
190-999 Rev G
Safety Precautions
General Remarks
These safety / installation instructions contain fundamental
information and precautionary notes and must be kept available
to all associated with the operation of the pump. Please read
them thoroughly prior to installation, electrical connection and
commissioning of the unit. It is imperative that all other operating
instructions relating to the components of individual units are
followed.
These safety / installation instructions do not take local
regulations into account. The operator must ensure that such
regulations are observed by all, including the personnel carrying
out the installation.
Each pump must be labeled by the end user to warn of any
hazards that the system process may produce; e.g. corrosive
chemicals or hot process etc.
All personnel involved in the operation, maintenance, inspection
and installation of the pump must be fully qualified to carry out
the work. The personnel’s responsibilities, competence and
supervision must be clearly defined by the operator. To the extent
that if the personnel in question is not already in possession of
the requisite know how, appropriate training and instruction must
be provided. In addition, the operator is responsible for ensuring
that the contents of the operating instructions are fully understood
by all the responsible personnel.
When installing a Hydra-Cell pump in conjunction with a motor
or motor and frequency controller the relevant manuals must
be referred to for electromagnetic compatibility. The installation
should conform to EN 61800 and EN 60204 as applicable.
All safety instructions in this manual and all relevant local health
and safety regulations must be followed.
Attention must be paid to the weight of the pump before either
lifting it manually or by selecting appropriate lifting equipment.
Inlet Piping
Provide for permanent or temporary installation of a compound
pressure gauge to monitor the inlet pressure. To maintain
maximum flow, the pump inlet should be under flooded suction
conditions at all times.
Do not supply more than one pump
from the same inlet line
.
Supply Tank
Use a supply tank that is large enough to provide time for any
trapped air in the fluid to escape. The tank size should be at least
twice the maximum pump flow rate.
Install a separate inlet line from the supply tank to each pump.
Place a cover over the supply tank, to prevent foreign objects
from falling into it.
Hose Sizing and Routing
To minimize acceleration head and frictional losses, size the
suction line at least one size larger than the pump inlet, and keep
the suction line as short and direct as possible.
Recommendations:
• Keep inlet lines less than 3 ft. (1 m) long
• Use at least 3/8” (9 mm) I.D. inlet hose
• Minimize fittings (elbows, valves, tees, etc.)
Support the pump and piping independently.
Inlet Piping (Pressure Feed)
Provide for permanent or temporary installation of a compound
pressure gauge to monitor the inlet pressure. To maintain
maximum flow, the pump inlet should be under flooded suction
conditions at all times.
Do not supply more than one pump
from the same inlet line.
Note: System back pressure must exceed the pump inlet
pressure by at least 15 psi (1 bar) in order to prevent flow
thru.
Discharge Piping
Hose and Routing
Use the shortest, most-direct route for the discharge line.
Select pipe or hose with a working pressure rating of at least 1.5
times the maximum system pressure. Example: Select a 1500 psi
(103 bar) W.P. rated hose for a system to be operated at 1000
psi (69 bar) gauge pressure.
Support the pump and piping independently.
Pressure Regulation
Install a pressure relief valve in the discharge line. Bypass
pressure must not exceed the pressure limit of the pump.
Size the valve so that, when fully open, it will be large enough
to relieve the full capacity of the pump without over pressurizing
the system.
Locate the valve as close to the pump as possible and ahead of
any other valves. Adjust the pressure relief valve to no more than
10% over the maximum working pressure of the system. Do not
exceed the manufacturer’s pressure rating for the pump or valve.
Route the bypass line to the supply tank.
CAUTION: Never install shutoff valves in the bypass line or
between the pump and pressure regulator or relief valve.
Provide for permanent or temporary installation of a pressure
gauge to monitor the discharge pressure at the pump.
Minimum Discharge Pressure
To ensure proper capacity control, a minimum discharge
pressure of 50 psi (3.5 bar) is required.