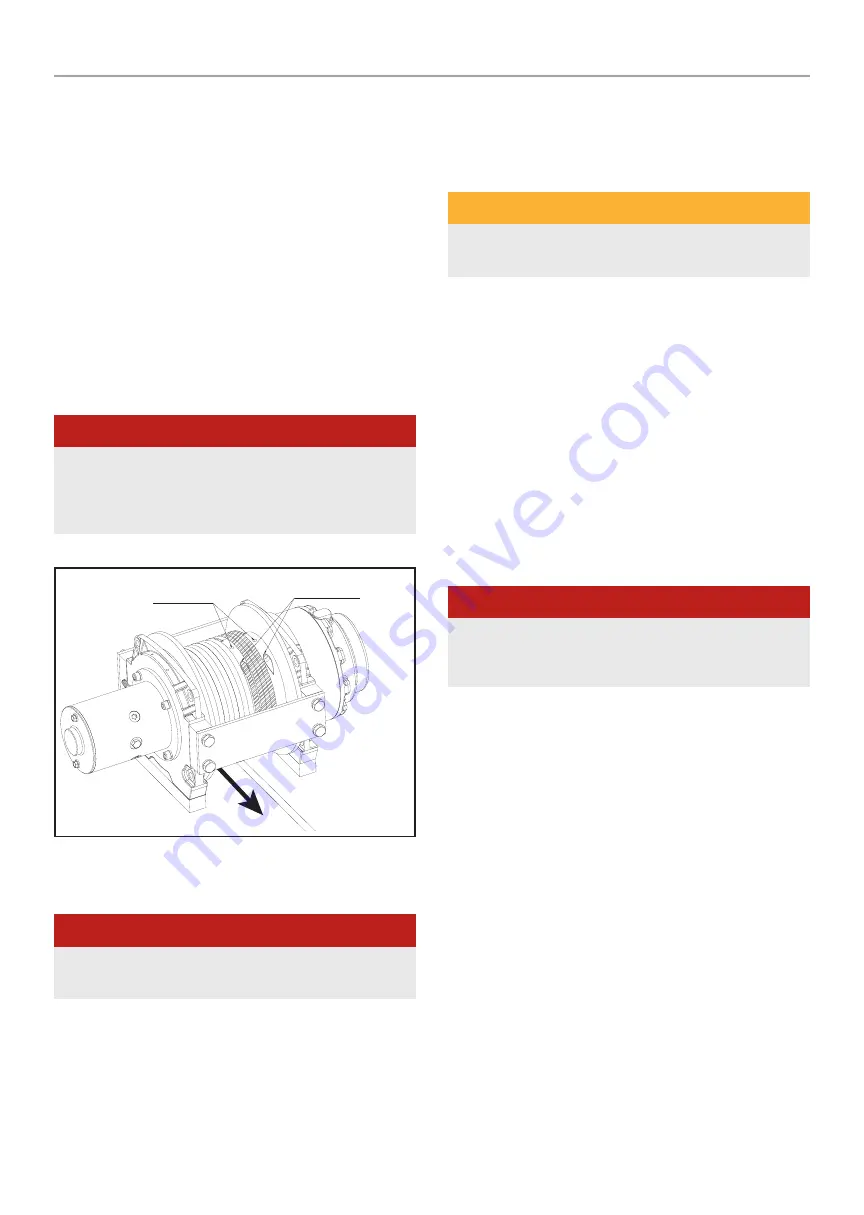
WINCH MANUAL
OpERATING INSTRUCTIONS
11
ROpE INSTALLATION
1. Power-in and/or power-out slightly to align hole in drum to a position
that is accessible for hoist rope installation.
2. Disconnect the positive cable from the battery.
3. Insert the hoist rope around the hoist drum from the bottom and
through the slot in the drum.
4. Release drum grub screw(s) located in drum cylinder and slide rope
through and secure. (On selective models use a loop and wedge
method to secure).
5. Ensure the cable does not protrude from the drum surface and that
the rope is held into place tightly and securely. With end of rope
installed and secured reconnect power and carefully power-in rope
evenly onto drum. Keep rope under some sort of tension at all times.
DANGER
A minimum of five wraps of cable around the drum barrel is necessary
for pulling and holding the rated load. The cable clamp is not designed
to hold the load without the 5 wraps of cable around the drum.
(usually marked red on the drum end of the cable)
Spool from underneath drum
Two fastening screws
Pass through two holes
OpERATING INSTRUCTIONS
DANGER
It is important to read ALL instructions and safety information before
installing and operating your hoist.
1. Take time to asses your situation and plan your pull.
2. Inspect mounting structure, hoist, slings and/or accessories for
signs of wear and damage. Replace any damaged parts.
3. Know the weight of your load you intend to lift and never exceed your
hoists rated load.
4. Connect the remote control lead to the hoist.
5. Ensure the load is directly under the hoist, and the rope is not
tangled or kinked.
6. Ensure the rope spools in the right direction.
WARNING
The spoolling direction may accidentally be reversed if rope is run all
the way out and re-spooled in with control switch in OUT direction.
7. Ensure the hook latch is functioning properly. Replace damaged
hook latch before operating hoist.
8. Double check your anchors and make sure all connections are
secure.
9. Inspect the wire rope. Make sure there are at least 5 wraps of wire
rope around the hoist drum.(usually marked with red)
10. Clear the area. Make sure all people, spectators are well back.
11. Begin hoisting. Be sure that the wire rope is winding evenly and
tightly around the drum. Avoid shock loading the wire rope under
tension.
12. The hoist is meant for intermittent use. Under full load with a single
line rig do not power in for more than 8 minutes without letting the
motor cool down for a few minutes and then resume the hoisting
operation.
DANGER
NEVER allow a crane to “two block.” Excess loads can create
undetectable damage, which may cause the hoist to fail even when
lifting loads within its rated capacity..
13. Once the load is secure - Release the tension and disconnect the
hook from the load. The hoist is NOT designed as securing device
and should NEVER hold a suspending load or used as securing device
whilst in transport, hoist cable MUST be released when equipment
is secure. Failure to follow these instructions will damage the brake
and hoist and void any warranty.
14. Rewind the wire rope under load. Make sure that any wire already
on the drum has spooled tightly and neatly. If not, draw out the wire
and re-spool from the point where the rope is tight.
15. Keep your hands clear of the hoist drum as the wire rope is being
drawn in.
16. Disconnect the remote control lead and store in a clean, dry place.
17. Clean and inspect connections and mounting hardware for next
hoisting operation.
Summary of Contents for EH800-CAD
Page 24: ...Winch Manual EH800 Exploded Diagram 24 EH800 EXPLODED DIAGRAM...
Page 26: ...Winch Manual EH1000 Exploded Diagram 26 EH1000 EXPLODED DIAGRAM...
Page 28: ...Winch Manual EH1000 SD Exploded Diagram 28 EH1000 SD EXPLODED DIAGRAM...
Page 30: ...Winch Manual EH1200 Exploded Diagram 30 EH1200 EXPLODED DIAGRAM...
Page 32: ...Winch Manual EH1600 Exploded Diagram 32 EH1600 EXPLODED DIAGRAM...
Page 34: ...Winch Manual EH2000 Exploded Diagram 34 EH2000 EXPLODED DIAGRAM...
Page 36: ...Winch Manual EH2500 Exploded Diagram 36 EH2500 EXPLODED DIAGRAM...
Page 38: ...Winch Manual EH3000 Exploded Diagram 38 EH3000 EXPLODED DIAGRAM...
Page 40: ...Winch Manual EH4000 Exploded Diagram 40 EH4000 EXPLODED DIAGRAM...