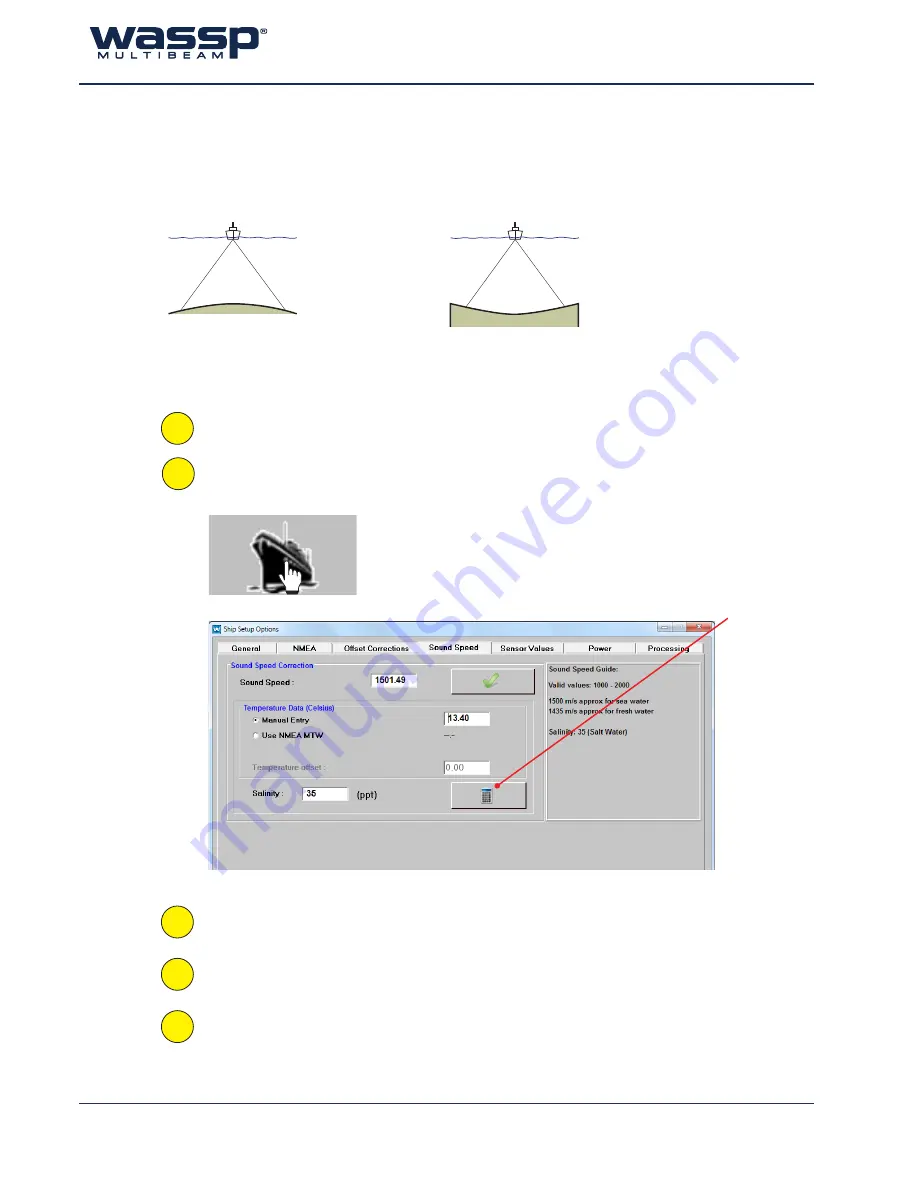
Doc. P/N:
WSP-009-005
Version: V1.5
Issue Date:
October 2013
www.wassp.com
Page 52 of 73
Installation Manual
10.2.4 Sea Trial - Commissioning Step 11 : Sound Speed
Sound speed varies with temperature so this changes throughout the year. Use a temperature sensor
to set the sound speed if possible. Otherwise, the operator should become familiar with this process
themselves and adjust on a regular (at least monthly) basis as necessary.
10.2.4.1
Option 1: Manual Sound Speed Correction:
Set the screen display (user interface) to
Sonar
view.
Set the sound speed computation method to
Manual Entry
in the
Ship Setup Options -
Sound Speed
Tab.
Find a section of seafloor that is known to be flat, preferably 20-100m deep.
Cross over the section of seafloor and adjust the sound speed value in the
Ship Setup Sound
Options - Speed Tab
until any curve in the seafloor has been removed.
In Manual Entry, Sound Speed can be entered directly or calculated from a known or
estimated Temperature and Salinity by clicking on the
Sound Speed Calculator
button. When
a Temperature Sensor is active a Temperature Offset can be applied to adjust for errors.
Figure 47. Ship Setup Sound Options - Manual Speed Correction
Seafloor Profile
Seafloor Profile:
Convex or flat
INCREASE
sound speed value
Seafloor Profile
Seafloor Profile:
Concave
DECREASE
sound speed
value
1
2
3
4
5
Sound Speed
Calculator