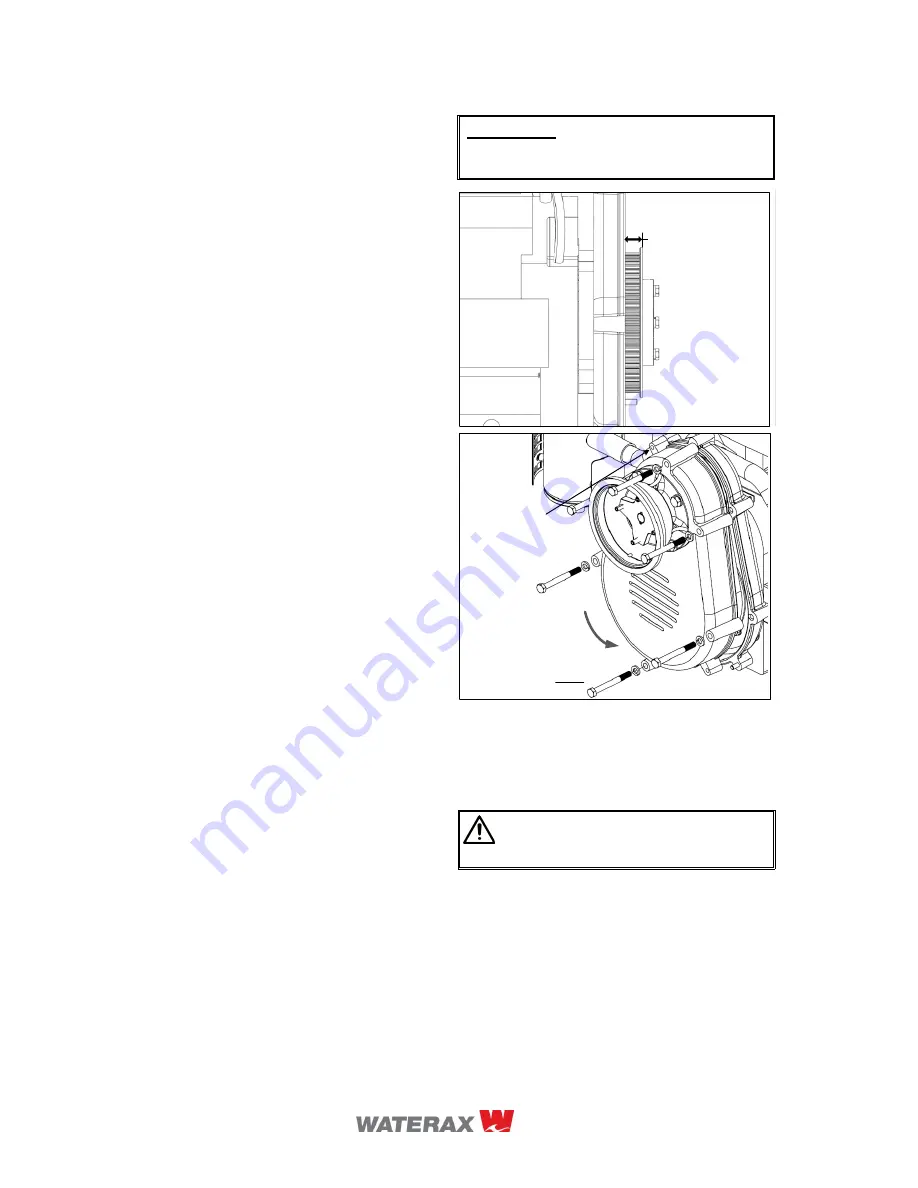
WATERAX
STRIKER-2/3 Owner's Manual
18
09/2015
8. Since tightening the cap screws will affect
the axial position of the pulley, make sure
pulleys are properly aligned:
D
R
= W - D
F
If adjustment is required, determine the
new position of the bushing and reposition
the pulley assembly. See page 19 for the
Removal of Pulley Assembly
procedure.
9. Loop the timing belt around the large driver
pulley.
IMPORTANT:
The torque value for the
driven pulley (small) cap screws is
108 in-lbs
, not 180 in-lbs.
D
R
10. To install the front cover, loop the timing
belt around the small driven pulley. Make
sure the timing belt is seated properly on
the pulleys.
11. Align the top dowel pin with the
corresponding hole on the front cover, and
partially insert the front cover onto the
dowel pin.
12. Using the top dowel pin as a pivot point,
swing the front cover and align the second
dowel pin with the corresponding hole.
13. Insert the front cover fully onto the dowel
pins and flat against the back cover mating
surface.
14. Fasten the front cover and the rear cover
using the six cap screws and lock washers.
To help seat the cover properly, tighten the
top screw, then the bottom screw, and then
alternate the screws on either side,
crisscrossing the cover. Securely tighten.
Align pivot
dowel and hole
in cover
Swing cover
into place
Secure cover
using cap
screws and
washers
15. Make sure the pulley assembly turns
smoothly by tugging on the recoil starter or
turning over the engine a couple of times
with the electric start.
Make sure you take all safety
precautions specified for your
engine.