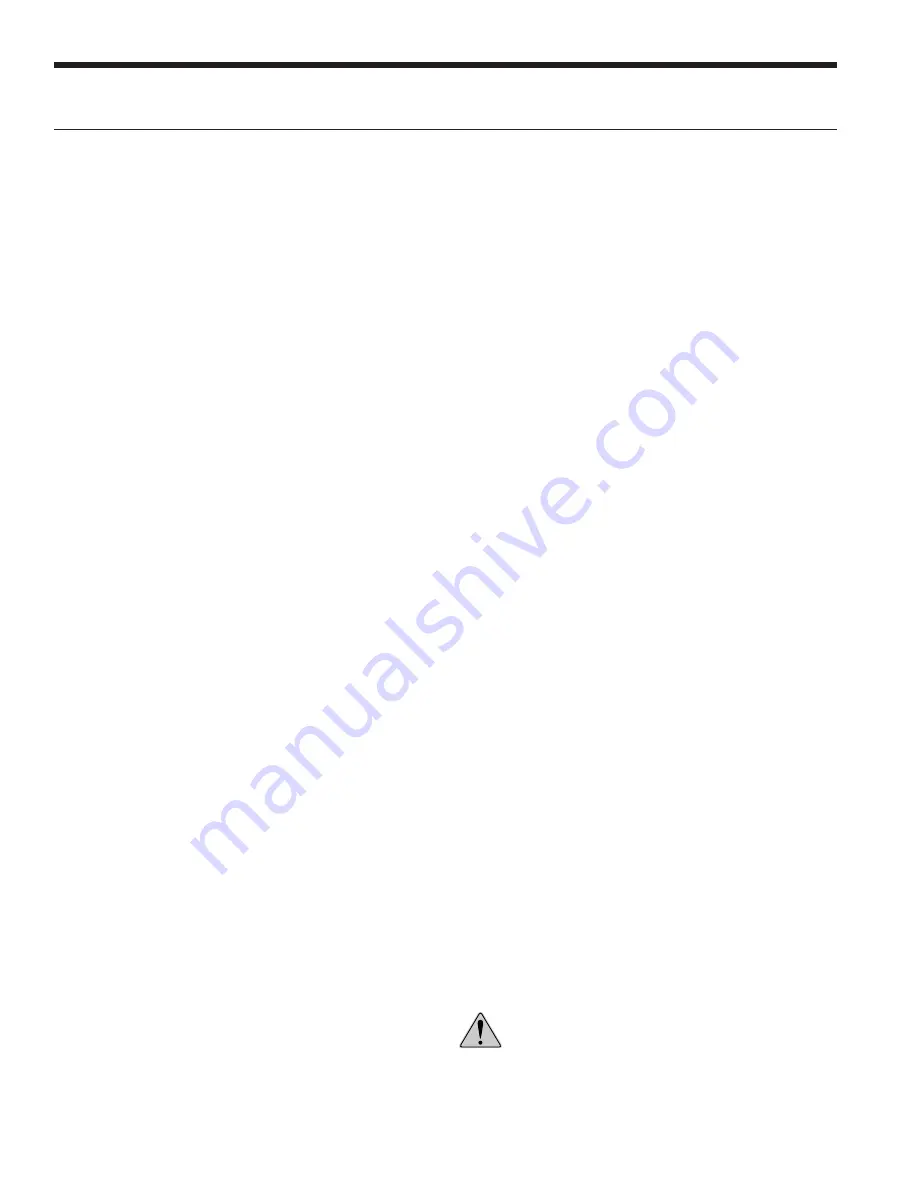
20
TRUCLIMATE 700 90-140 TON INSTALLATION MANUAL
Water Quality
1.0. Minimum Fluid Volume
A. Water-to-water heat pumps require a minimum amount
of source and load side fl uid volume to ensure accurate
and stable temperatures during system operation.
For normal air conditioning type applications, it is
recommended to use at least 7 gallons/ton.
B. Applications that require more precise temperature
control or low loading will occur the minimum
fl uid volume shall be no less than 10 gallons/ton.
Installation of a buff er tank that will properly mix the
fl uid is recommended.
1.1. Water-to-Water Heat Pump Sizing
A. Heat pumps should be adequately sized for optimal
system effi
ciency and run time. Oversizing by more
than 15% can diminish performance resulting in higher
power consumption, short cycling of compressors, and
unstable conditioning temperatures.
B. In applications where the minimum load is signifi cantly
less than the design condition, it is better to install 2
smaller heat pumps for load matching rather than a
single large heat pump.
1.2. Heat Pump Piping
A. Multiple heat pumps can be installed in series or
parallel confi gurations. The preferred system design is
to pipe the equipment in parallel due to its simplicity
and fl exibility. In parallel systems, the heat pump
equipment can vary in size as long as fl ow rate and
system volume are accounted for.
B. Piping equipment in series is not desired; however,
it can be done if proper guidelines are followed.
Always observe proper temperature and fl ow rate
requirements for each unit. Sometimes this method is
desired to achieve larger temperature diff erences.
1.3. Strainers
A. All brazed-plate heat exchangers shall have a
strainer within 8 ft of the water/brine inlet. It is highly
recommended to use a minimum of 60 mesh in order
to provide maximum fi ltration. In any case, the strainers
should never have a mesh size less than 20.
B. Failure to install proper stainers and perform regular
service can result in serious damage to the unit, and
cause degraded performance, reduced operating life
and failed compressors. Improper installation of the
unit (which includes not having proper strainers to
protect the heat exchangers) can also result in voiding
the warranty.
C. Strainers should be selected on the basis of acceptable
pressure drop, and not on pipe diameter. The strainers
selected should have a pressure drop at the nominal
fl ow rate of the units; low enough to be within the
pumping capacity of the pump being used.
1.4. Flow Sensing Devices
A. A
fl ow switch or equivalent must be installed on the
evaporator for each unit to be installed. If the unit is to
operate as both modes (heating/cooling), a fl ow switch
is needed on both heat exchangers.
B. A
diff erential pressure switch can be used in place of a
fl ow switch. The diff erential switch must be capable of
pressure range as indicated in the pressure drop tables.
1.5. Water Quality
A.
General:
Reversible chiller systems may be successfully
applied in a wide range of commercial and industrial
applications. It is the responsibility of the system
designer and installing contractor to ensure that
acceptable water quality is present and that all
applicable codes have been met in these installations.
B.
Water Treatment:
Do not use untreated or improperly
treated water. Equipment damage may occur. The
use of improperly treated or untreated water in this
equipment may result in scaling, erosion, corrosion,
algae or slime. The services of a qualifi ed water
treatment specialist should be engaged to determine
what treatment, if any, is required. The product
warranty specifi cally excludes liability for corrosion,
erosion or deterioration of equipment.
The heat exchangers in the units are 316 stainless steel
plates with copper brazing. The water piping in the
heat exchanger is steel. There may be other materials
in the building’s piping system that the designer may
need to take into consideration when deciding the
parameters of the water quality.
If an antifreeze or water treatment solution is to be
used, the designer should confi rm it does not have a
detrimental eff ect on the materials in the system.
C.
Contaminated Water:
In applications where the
water quality cannot be held to prescribed limits, the
use of a secondary or intermediate heat exchanger
is recommended to separate the unit from the
contaminated water.
The following table outlines the water quality
guidelines for unit heat exchangers. If these conditions
are exceeded, a secondary heat exchanger is required.
Failure to supply a secondary heat exchanger where
needed will result in a warranty exclusion for primary
heat exchanger corrosion or failure.
WARNING: Must have intermediate heat exchanger
when used in pool applications.
Summary of Contents for TruClimate 700
Page 2: ......
Page 10: ...10 TRUCLIMATE 700 90 140 TON INSTALLATION MANUAL Dimensional Data...
Page 11: ...11 TRUCLIMATE 700 90 140 TON INSTALLATION MANUAL Dimensional Data Service Clearance...
Page 12: ...12 TRUCLIMATE 700 90 140 TON INSTALLATION MANUAL Dimensional Data Center of Gravity...
Page 13: ...13 TRUCLIMATE 700 90 140 TON INSTALLATION MANUAL Dimensional Data Rigging Data...
Page 25: ...25 TRUCLIMATE 700 90 140 TON INSTALLATION MANUAL Wiring Schematic next page...
Page 36: ...36 TRUCLIMATE 700 90 140 TON INSTALLATION MANUAL Evaporator Pressure Drop...
Page 37: ...37 TRUCLIMATE 700 90 140 TON INSTALLATION MANUAL Condenser Pressure Drop...
Page 39: ...39 TRUCLIMATE 700 90 140 TON INSTALLATION MANUAL Screw Refrigeration Cycle Analysis...