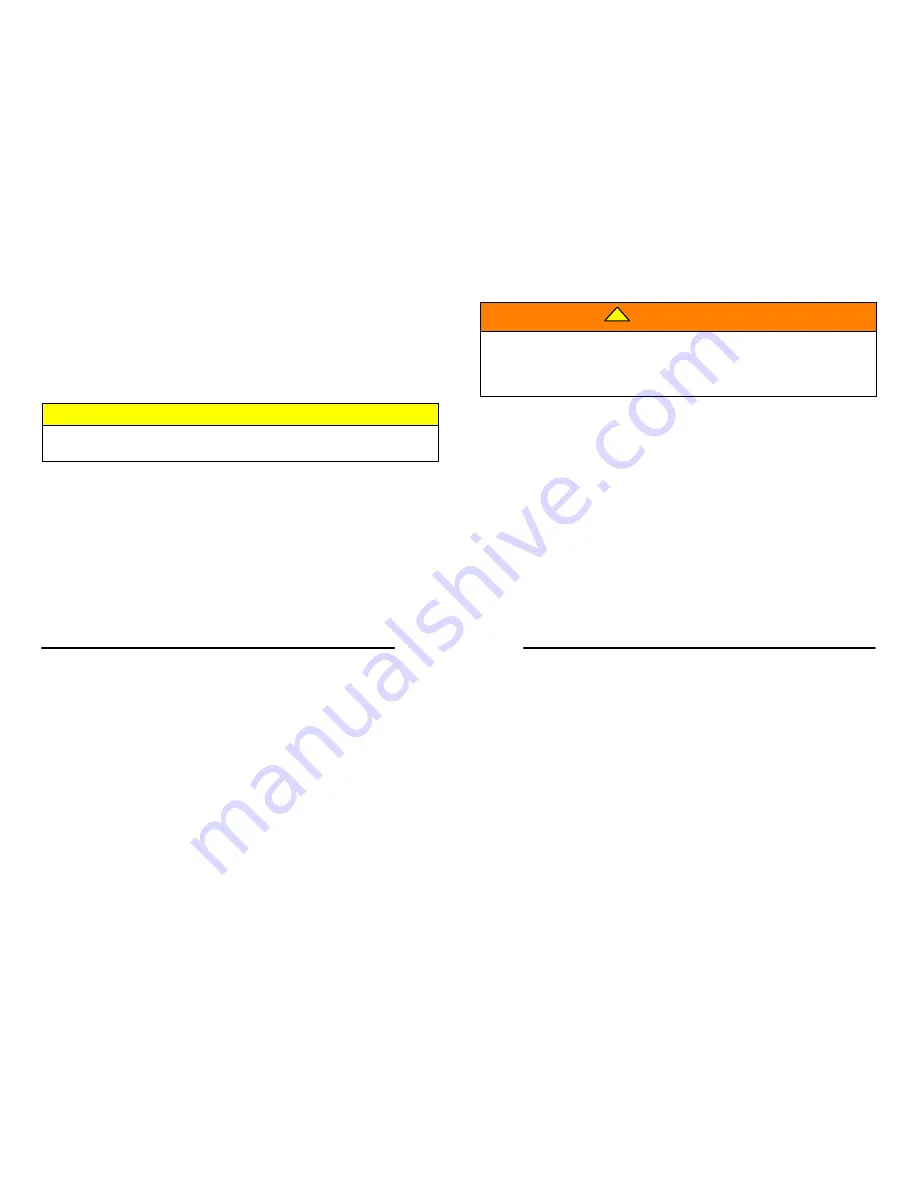
Page 7 of 7
F−1031, Section 4209
Rev: 01/03/07
3.
If drip rate is considered high, stop the engine and tighten the packing
gland nuts 1/2 to 1 flat (maximum of 1/6 of a revolution). Make appropri-
ate adjustments starting with 1 flat, when approaching the final adjust-
ment reduce to 1/2 flat. This reduces the possibility of over tightening.
Tighten the gland nuts equally to ensure that the packing gland
goes on straight. Gradually reducing leakage during the first hour of
operation will result in a better seal over a longer period of time.
CAUTION
Stopping the leakage entirely at this point will cause the packing to
overheat.
4.
Operate the pump at the capacity pressure shown on the serial plate for
two (2) minutes to let packing run in, then observe the drip rate.
WARNING
!
Packing Gland and Pump Body Temperature Hazard. May result in
serious burns.
Heat is dissipated through the cross−section of the packing, transferring
the heat to the packing gland and pump body.
5.
Repeat steps 3 and 4 until the drop rate is acceptable.
NOTE: After adjusting the packing, the pump must pass the follow-
ing vacuum test described below.
Vacuum Test
1.
Remove all caps except openings without valves. Close all discharge,
intake and drain valves and other similar openings. Operate priming de-
vice to create a vacuum of about 22 in. Hg/.735 atmosphere in pump,
then stop primer and engine.
2.
Watch the pressure gauge; if vacuum drops more than 10 in. Hg/.334
atmospheres in five (5) minutes, listen for air leaks around the packing
gland, gaskets, valves, etc.
3.
Replace gaskets, re−adjust packing, repack or otherwise repair source of
trouble.
4.
Repeat test.
Testing
Before a pump is returned to service, it is advisable to give it both hydrostatic and operational tests to check it for leaks and to make sure the pump operates properly.
Hydrostatic Testing
1.
Connect pump to a hydrant or other pressurized water supply.
2.
Close all drain lines and open discharge and priming valves.
3.
Open hydrant until water runs out through discharge valves and dis-
charge pipe in priming pump. Close all valves. Be sure to evacuate all air
from pump.
4.
Apply water pressure to pump for 15 minutes. Do not exceed 350 psi
(24.2 bar). With a portable light, check pump for leaks. If leaks are dis-
covered, tighten connections or attaching parts as necessary.
NOTE: If a mechanical seal is used, it may leak under hydrostatic pres-
sure. However, it should stop leaking after the seal faces are run−in
during operational testing.
5.
After all leaks are eliminated, shut hydrant valve, drain pump completely
and disconnect intake hose.
Operational Testing
1.
Operate pump at its maximum intended service pressure. Do not exceed
350 psi (24.2 bar) (450 psi, 31 bar with positive intake).
2.
With a portable light, check pump for leaks. If leaks are discovered, stop
pump and tighten connections or attaching parts as necessary. Repeat
until all leaks are eliminated.
3.
While pump is running, check for unusual noises, oil leaks, overheated
bearings, etc. If anything unusual is discovered, stop pump immediately
and determine the cause.