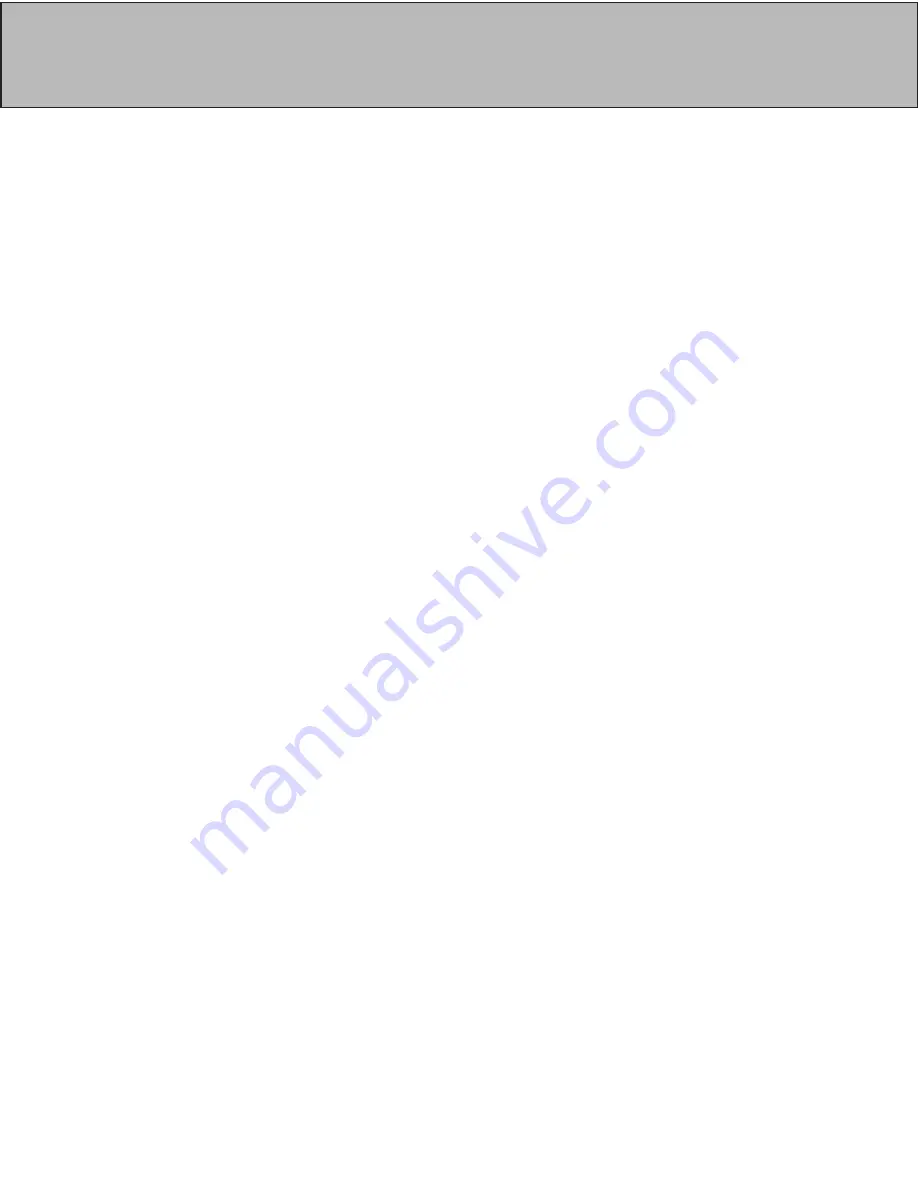
RS1
1. Set time of day.
2. Set a.m. or p.m.
3. Set water hardness in grains per gallon (gpg).
Note :
If the water contains iron and / or manganese, multiply the total parts per million (ppm) by “four” (4) and then add
to the grains per gallon (gpg) of hardness. Use this COMPENSATED HARDNESS level when programming the regenera-
tion frequency.
1. Set regeneration day override if other than (7) days is desired. (This is particularly useful when iron is being treated to
prevent fouling of the resin.)
2. Set regeneration time, if other than 2:00 a.m. is desired.
Warning :
Do not reduce salt settings below 9 lbs. as the water level in the brine tank will not reach the grid plate.
- Control Valve Operation -
1. Advance control valve to BACKWASH (cycle 1) position and allow water to run to drain for 3 to 4 minutes.
Warning :
Close valve on bypass prior to selecting the backwash position. After backwash position has been
established, slightly open bypass to evacuate air from the media tank. Fully open valve when all air
is depleted. This procedure will prevent media from being uplifted into control valve.
2. Advance control valve to BRINE REFILL (cycle 4) position and allow the brine tank to fill just over the salt grid plate.
3. Advance control valve to BRINE & RINSE (cycle 2) and allow the control valve to draw water from the brine tank until it
stops. If no draw is observed, check tightness of brine line compression fittings.
4. Advance control valve to RAPID RINSE (cycle 3) position and let run to drain for 3 - 4 minutes.
5. Advance control valve to BRINE TANK REFILL (cycle 4) position and allow the control valve to automatically fill the
brine tank.
Note :
Control valve will advance to service position automatically.
9
Installation