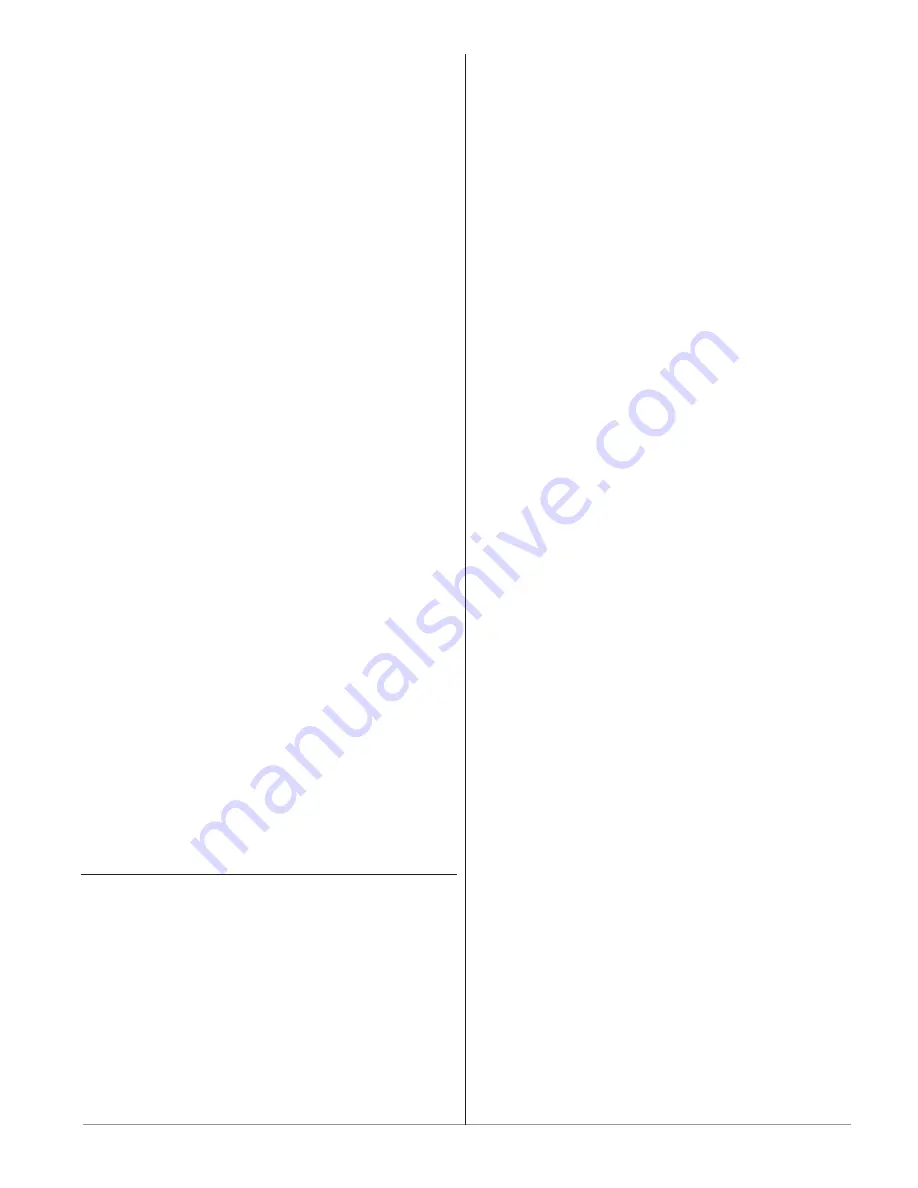
Wa t l o w E Z - Z O N E
®
P M I n t e g r a t e d C o n t r o l l e r
•
5 5
•
C h a p t e r 9 F e a t u r e s
Manual Tuning
In some applications, the autotune process may not
provide PID parameters for the process characteris-
tics you desire. If that is the case, you may want to
tune the controller manually.
1. Apply power to the controller and establish a set
point typically used in your process.
2. Go to the Operations Page, Loop Menu, and set
Heat Proportional Band
[`h;Pb]
and/or Cool Pro-
portional Band
[`C;Pb]
to 5. Set Time Integral
[``ti]
to 0. Set Time Derivative
[``td]
to 0.
3. When the system stabilizes, watch the process
value. If it fluctuates, increase the Heat Propor-
tional Band or Cool Proportional Band value in 3
to 5° increments until it stabilizes, allowing time
for the system to settle between adjustments.
4. When the process has stabilized, watch Heat
Power
[`h;Pr]
or Cool Power
[`C;Pr]
(Operations
Page, Monitor Menu). It should be stable ±2%. At
this point, the process temperature should also
be stable, but it will have stabilized before reach-
ing the set point. The difference between the set
point and actual process value can be eliminated
with Integral.
5. Start with an Integral value of 6,000 and allow
10 minutes for the process temperature to reach
the set point. If it has not, reduce the setting by
half and wait another 10 minutes. Continue re-
ducing the setting by half every 10 minutes until
the process value equals the set point. If the pro-
cess becomes unstable, the Integral value is too
small. Increase the value until the process stabi-
lizes.
6. Increase Derivative to 0.1. Then increase the set
point by 11° to 17°C. Monitor the system’s ap-
proach to the set point. If the process value over-
shoots the set point, increase Derivative to 0.2.
Increase the set point by 11° to 17°C and watch
the approach to the new set point. If you increase
Derivative too much, the approach to the set
point will be very sluggish. Repeat as necessary
until the system rises to the new set point with-
out overshoot or sluggishness.
For additional information about autotune and PID
control, see related features in this chapter.
Autotuning with TRU-TUNE+
®
The TRU-TUNE+
®
adaptive algorithm will optimize
the controller's PID values to improve control of dy-
namic processes. TRU-TUNE+
®
monitors the process
variable and adjusts the control parameters auto-
matically to keep your process at set point during set
point and load changes. When the controller is in the
adaptive control mode, it determines the appropriate
output signal and, over time, adjusts control param-
eters to optimize responsiveness and stability. The
TRU-TUNE+
®
feature does not function for on-off
control.
The preferred and quickest method for tuning a
loop is to establish initial control settings and contin-
ue with the adaptive mode to fine tune the settings.
Setting a controller's control mode to tune starts
this two-step tuning process. (See Autotuning in this
chapter.) This predictive tune determines initial,
rough settings for the PID parameters. Then the loop
automatically switches to the adaptive mode which
fine tunes the PID parameters.
Once the process variable has been at set point for
a suitable period (about 30 minutes for a fast process
to roughly two hours for a slower process) and if no
further tuning of the PID parameters is desired or
needed, TRU-TUNE+™ may be turned off. However,
keeping the controller in the adaptive mode allows it
to automatically adjust to load changes and compen-
sate for differing control characteristics at various
set points for processes that are not entirely linear.
Once the PID parameters have been set by the
TRU-TUNE+™ adaptive algorithm, the process, if
shut down for any reason, can be restarted in the
adaptive control mode.
Turn TRU-TUNE+™ on or off with TRU-TUNE+™
Enable
[t;tUn]
(Setup Page, Loop Menu).
Use TRU-TUNE+™ Band
[t;bnd]
(Setup Page,
Loop Menu) to set the range above and below the
set point in which adaptive tuning will be active.
Adjust this parameter only in the unlikely event
that the controller is unable to stabilize at the set
point with TRU-TUNE+™ Band set to auto (0). This
may occur with very fast processes. In that case, set
TRU-TUNE+™ Band to a large value, such as 100.
Use TRU-TUNE+™ Gain
[`t;gn]
(Setup Page,
Loop Menu) to adjust the responsiveness of the adap-
tive tuning calculations. Six settings range from 1,
with the most aggressive response and most poten-
tial overshoot (highest gain), to 6, with the least ag-
gressive response and least potential for overshoot
(lowest gain). The default setting, 3, is recommended
for loops with thermocouple feedback and moderate
response and overshoot potential.
Before Tuning
Before autotuning, the controller hardware must be
installed correctly, and these basic configuration pa-
rameters must be set:
•
Sensor Type
[`SEn]
(Setup Page, Analog Input
Menu), and scaling, if required;
•
Function
[``Fn]
(Setup Page, Output Menu) and
scaling, if required.
How to Autotune a Loop
1. Enter the desired set point or one that is in the
middle of the expected range of set points that
you want to tune for.
2. Enable
TRU-TUNE+
®
.
Summary of Contents for Integrated Controller Rev C EZ-ZONE PM
Page 79: ......