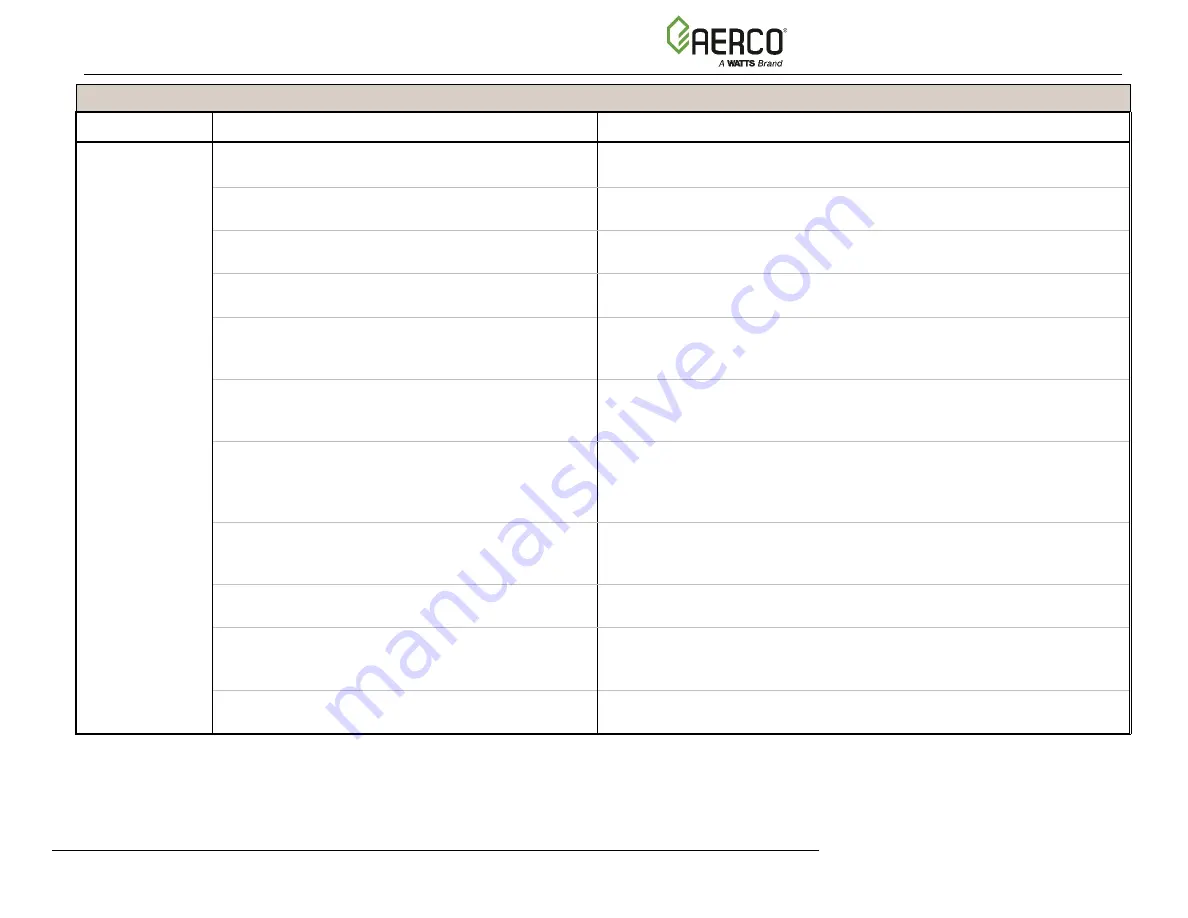
Benchmark Platinum-Edge: Operation-Service Manual
SECTION 6 – TROUBLESHOOTING
OMM-0137_D • GF-211
•
7/16/2019
Technical Support
•
(800) 526-0288
•
Mon-Fri, 8 am - 5 pm EST Page 133 of 146
TABLE 10-1: Boiler Troubleshooting Procedures
Fault
Probable Causes
Corrective Action
AIRFLOW
FAULT
DURING
IGNITION
1.
Blower stopped running due to thermal or
current overload.
1.
Check combustion blower for signs of excessive heat or high current
drain that may trip thermal or current overload devices.
2.
Blocked Blower inlet or inlet air filter.
2.
Inspect the inlet to the combustion blower including the air filter at
the air/fuel valve for signs of blockage.
3.
Blockage in Blower Proof switch.
3.
Remove the Blower Proof switch and inspect for signs of blockage,
clean or replace as necessary.
4.
Blockage in Blocked Inlet switch.
4.
Remove the Blocked Inlet switch and inspect for signs of blockage,
clean or replace as necessary.
5.
Defective Blower Proof switch.
5.
Check the continuity of the Blower Proof switch with the combustion
blower running. If there is an erratic resistance reading or the
resistance reading is greater than zero ohms, replace the switch.
6.
Defective Blocked Inlet switch.
6.
Turn off unit and check the continuity of the Blocked Inlet switch. If
there is an erratic resistance reading or the resistance reading is
greater than zero ohms, replace the switch.
7.
Bad inlet air temperature sensor.
7.
Check the actual inlet air temperature reading and measure
resistance at the Sensor Harness connection P1. Verify that the
reading conforms to the values shown in Section 2 of the
Benchmark Platinum-Edge: REFERENCE Manual
(GF-212).
8.
Defective temperature sensor.
8.
Refer to CORRECTIVE ACTION 7 and verify that the voltage
conforms to the values shown in Section 2 of the
Benchmark
Platinum-Edge: REFERENCE Manual
(GF-212).
9.
Loose wire connection between the the
Blower and the Controller.
9.
Check wire connection from the Blower motor to the Secondary
Power Panel.
10.
Defective Air-Fuel Valve potentiometer.
10.
Check Air/Fuel Valve position at 0%, 50% and 100% open
positions. The positions on the
Valve Position
bargraph should
match the readings on the Air/Fuel Valve dial.
11.
Hard light.
11.
Check igniter-injector for soot or erosion of electrode. Check
injector solenoid valve to insure proper open/close operation.