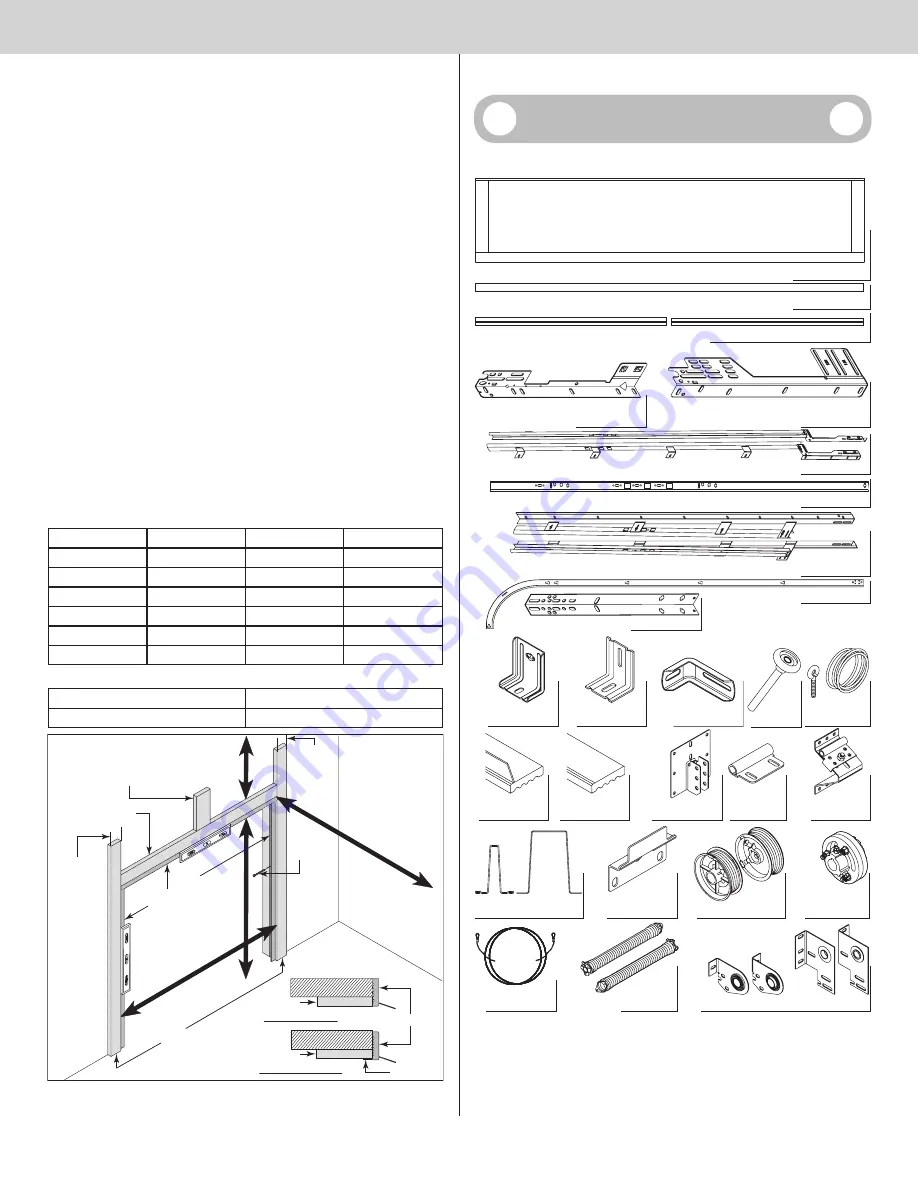
NOTE:
Drill a 3/16” pilot hole in the mounting surface to avoid splitting the lumber. Do not
attach the mounting surface with nails.
WEATHERSTRIPS (MAY NOT BE INCLUDED):
Depending on the size of your door, you may have to cut or trim the weatherstrips (if neces-
sary) to properly fit into the header and jambs.
NOTE:
If nailing product at 40°F or below, pre-drilling is required.
NOTE:
Do not permanently attach weatherstrips to the header and jambs at this time.
FOR QUICK INSTALL TRACK:
For the header, align the weatherstrip with the inside edge
of the header and temporarily secure it to the header with equally spaced nails. Starting
at either side of the jamb, fit the weatherstrip up tight against the temporarily attached
weatherstrip in the header and flush with the inside edge of the jamb. Temporarily secure
the weatherstrip with equally spaced nails. Repeat for other side. This will keep the bottom
section from falling out of the opening during installation. Equally space nails approximately
12” to 18” apart.
FOR FULLY ADJUSTABLE TRACK:
For the header, align the weatherstrip 1/8” to 1/4” inside
the header edge, and temporarily secure it to the header with equally spaced nails. Starting
at either side of the jamb, fit the weatherstrip up tight against the temporarily attached
weatherstrip in the header and 1/8” to 1/4” inside the jamb edge. Temporarily secure the
weatherstrip with equally spaced nails. Repeat for other side. This will keep the bottom sec-
tion from falling out of the opening during installation. Equally space nails approximately 12”
to 18” apart.
HEADROOM REQUIREMENT:
Headroom is defined as the space needed above the top of
the door for tracks, springs, etc. to allow the door to open properly. If the door is to be motor
operated, 2-1/2” (64 mm) of additional headroom is required.
NOTE:
6” low headroom conversion kit is available for 12” radius only. Contact your local
Wayne Dalton dealer.
BACKROOM REQUIREMENT:
Backroom is defined as the distance needed from the opening
back into the garage to allow the door to open fully.
*NOTE:
For door heights from 10’1” to 14’0”, refer to your operator manufacture installation
instructions for appropriate depth into room.
BACKROOM REQUIREMENTS
Door Height
Track
Manual Lift
Motor Operated
6’0” to 7’0”
12”, 15” Radius
102” (2591 mm)
125” (3175 mm)
7’1” to 8’0”
12”, 15” Radius
114” (2896 mm)
137” (3480 mm)
8’1” to 9’0”
12”, 15” Radius
126” (3200 mm)
168” (4267 mm)
9’1” to 10’0”
12”, 15” Radius
138” (3505 mm)
168” (4267 mm)
10’1” to 12’0”
12”, 15” Radius
162” (4115 mm)
See *NOTE
12’1” to 14’0”
12”, 15” Radius
186” (4724 mm)
See *NOTE
HEADROOM REQUIREMENTS
Track Type
Space Needed
15” Radius
14-1/2” (368 mm)
Weatherstrips
Level heade
r
Finished
Door width
Jamb
s
Backroo
m
Plumb
jambs
Finished
Door
Height
Nail
Headroom
Header board 2”x 6”
lumber preferred
Suitable mounting surface
2”x 6” lumber minimum
Weatherstrips
Jamb
Quick Install track
Other track systems
Jamb
1/8” to 1/4”
Min. Side
room
Clearance
is 3-1/2”
Min. Side
room
Clearance
is 3-1/2”
Package Contents
NOTE:
Depending on the door model, some parts listed will not be supplied if not required.
Rear Back Hangs may not be included with your door.
Door sections (as required)
Torsion shaft or Torsion keyed shaft (as required)
Torsion keyed shafts (as required)
Vertical tracks RH/LH (as required)
Riveted vertical track assemblies RH/LH (as required)
Wall angle track assemblies RH/LH (as required)
(2) Horizontal angles (as required)
Horizontal tracks RH/LH (as required)
Quick Install flag angles
RH/LH (as required)
Fully Adjustable flag angles
RH/LH (as required)
Weather seals &
nails (If included)
Door stop & nails
(If included)
Q.I. Jamb brackets
(as required)
F.A. Jamb brackets
(as required)
Drawbar operator
bracket (if included)
Track rollers
Pull down rope
(if included)
Windload Jamb
brackets (as required)
Top fixture
roller slides
(as required)
Top
fixture assemblies
(as required)
Hinge brackets
(as required)
Torsion springs RH/LH
Counterbalance
lift cables
Cable drums RH/LH
Center coupler
assembly
(as required)
Strut (U-shaped)
(if included)
End bearing bracket RH/LH (as required)
3