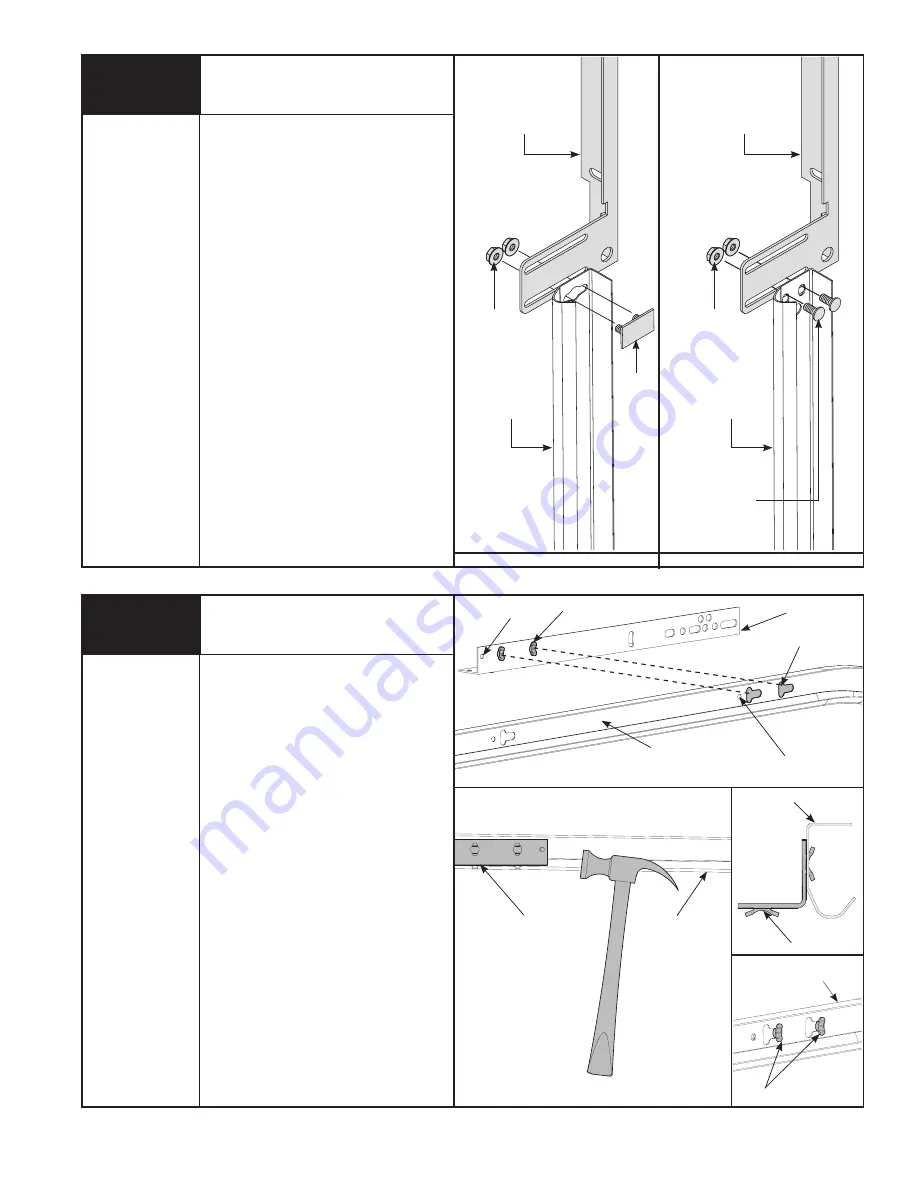
Tools Needed:
8
Tools Needed:
Please Do Not Return This Product To The Store.
Contact your local Wayne-Dalton dealer. To find your local Wayne-Dalton dealer, refer to your
local yellow pages/business listings or go to the
Find a Dealer
section online at
www.wayne-dalton.com
Position the horizontal angle as shown.
Place tabs of horizontal angle in the key
slot of horizontal track. using a hammer,
tap the horizontal angle towards the
curved end of the track until the hole in
track and angle are aligned. set tracks
aside.
NOTE:
for larger doors, a full length
horizontal angle may be spot welded
to the horizontal track. If the horizontal
angle is not welded, the horizontal angle
must be installed as shown.
horizontal Angles
hammer
hORIzONTal
TRaCk
hORIzONTal
aNGlE
hORIzONTal aNGlE
hORIzONTal TRaCk
hOlE
hOlE
Tabs
kEy slOT
3
hORIzONTal
TRaCk
Tabs
hORIzONTal
TRaCk
hORIzONTal
aNGlE
Attaching Fully Adjustable
Flagangles to vertical Track
None
2
NOTE:
If quick install flagangles were
installed in step 1, skip this step and
continue with step 3. If not, complete
this step.
If you have quick install vertical track,
hand tighten the flagangle to the
vertical track using (1) stud plate and
(2) 1/4” - 20 flange hex nuts. Repeat for
other side.
secure the flange nuts after flagangle
spacing is complete (step 15).
If you have fully adjustable vertical
track, hand tighten the flagangle to the
vertical track using (2) 1/4”- 20 x 9/16”
track bolts and (2) 1/4”- 20 flange hex
nuts. Repeat for other side.
secure the flange nuts after flagangle
spacing is complete (step 15).
1/4”- 20
flaNGE hEx
NuTs
fully aDjusTablE
flaGaNGlE
sTuD
PlaTE
quICk INsTall
VERTICal TRaCk
quICk INsTall TRaCk
(2) 1/4”- 20 x 9/16”
TRaCk bOlTs
1/4”- 20
flaNGE hEx
NuTs
fully aDjusTablE
flaGaNGlE
fully aDjusTablE
VERTICal TRaCk
fully aDjusTablE TRaCk