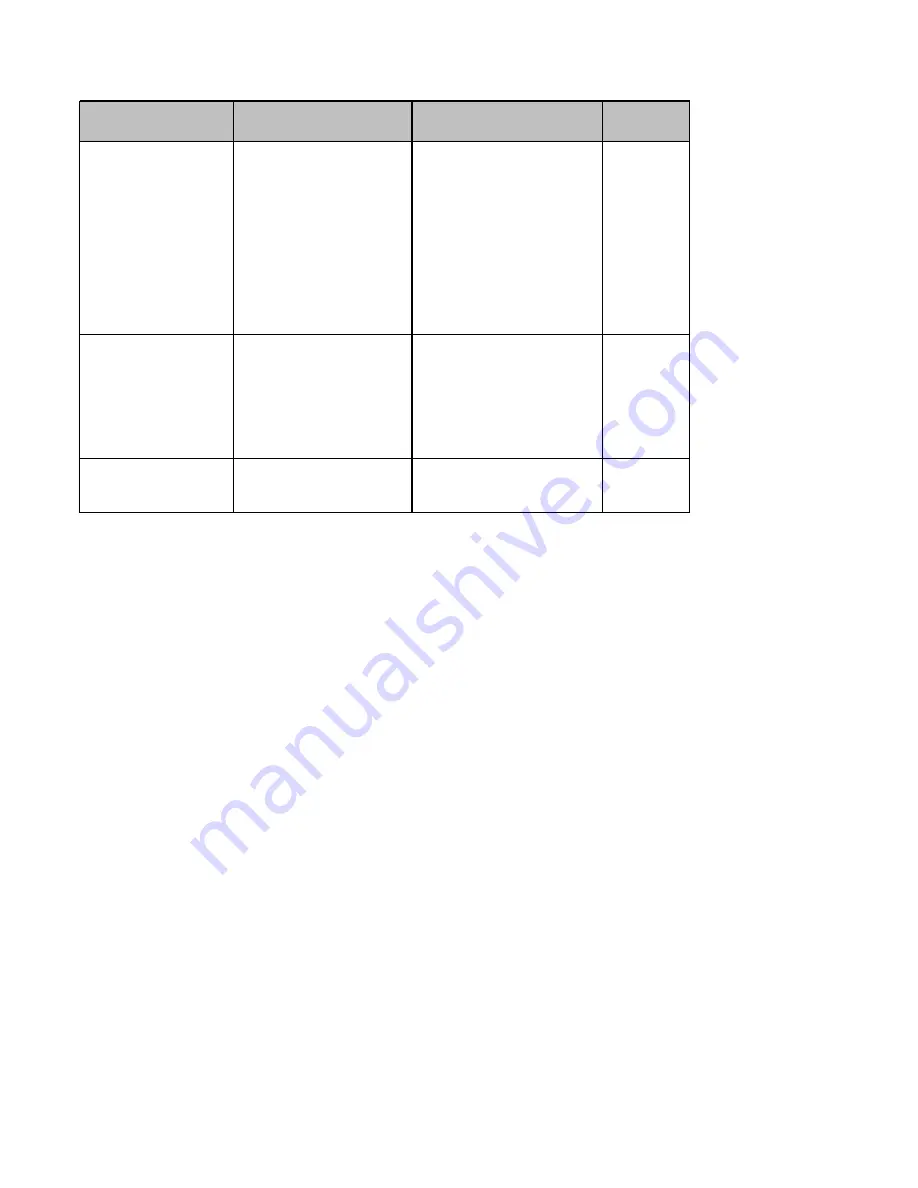
29
CR7
4.2 Trouble Shooting
Failure
Possible Cause
Remedy
Remarks
Soil compactor does
not start
Mistake in operating the unit Perform the starting procedure
as described
# 2.5
Lack of fuel
Check the fuel level
# 2.4.1
Dirty fuel filter
Replace the fuel filter
# 3.3.3
Dirty air filter
Clean/replace the air filter
cartridge
# 3.3.2
No vibration/no or
insufficient forward
travel
Defective vibrator V-belt
Replace the vibrator V-belt
# 3.3.5
Delayed control
Air in the hydraulic control
system
Bleed the control system
# 3.3.7
Summary of Contents for CR 7
Page 2: ...2 CR7 ...