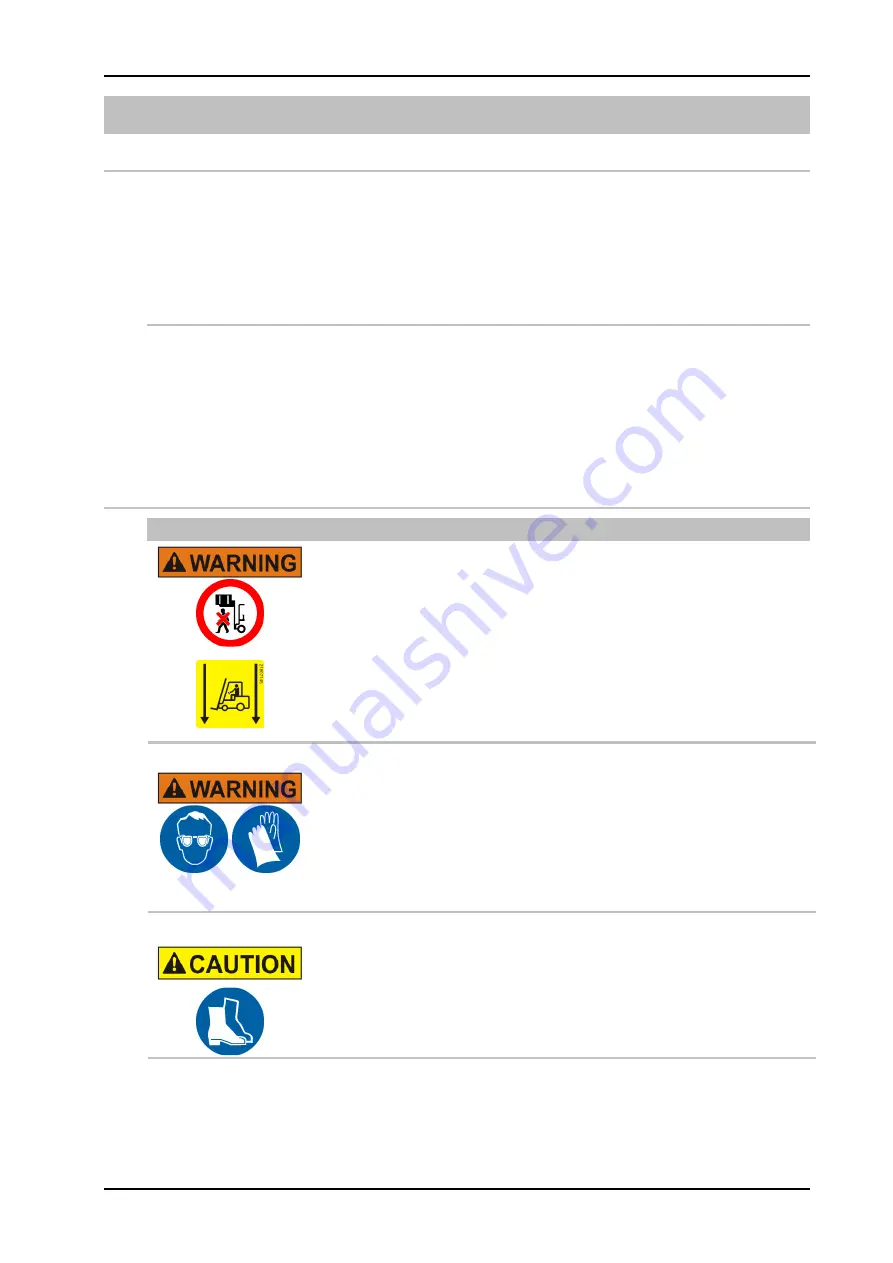
Chapter 5
Transport
32708885 Geset 100
Version: 16.07.13
Page 28 of 77
GB
5. Transport
Delivery
The labeling station is normally delivered by a haulage contractor. Check the package for
any damage. If you notice anything unusual, notify the haulage contractor immediately
and note it on the delivery slip.
Scope of the delivery
The elements of the system delivery depend on the selected options and the customer's
specific application. When the system is delivered, check to see if everything is there
against the delivery slip.
Transportation and unpacking
Safety instructions
Hazard from lifted loads.
Falling loads can cause severe injury or death.
- Do not walk under a lifted load. The load may not be tilted.
- The location of the center of gravity must be taken into account
when transporting the system. Loads with displaced center of
gravity have special markings for the targeted placement of ma-
terial handling equipment.
Hazard from tight straps.
The straps are secured tightly and can snap off if they are cut and
cause severe injury.
- Wear protective glasses and gloves.
- Stand to the side outside of the hazard zone.
Hazard from falling parts.
- Wear protective footwear.
The transport will be arranged by a Technician of the Bluhm Weber Group or by authori-
zed specialists.
Summary of Contents for Geset 100
Page 2: ...Blank page ...