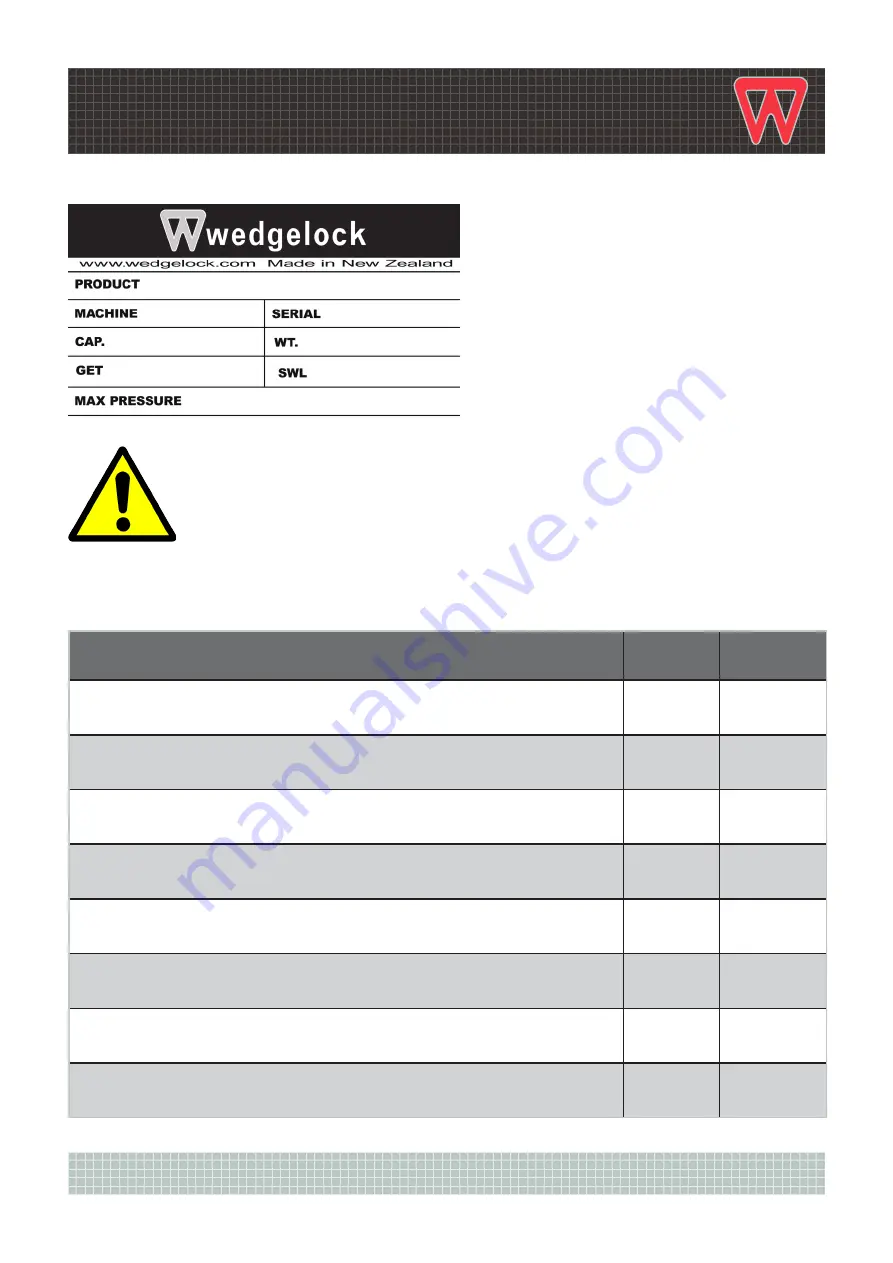
Parts & Service 21/09/2015
902-002-11 Rev 6
Page 11
SECTION 3:
Maintenance
3.0 COUPLER IDENTIFICATION
All Wedgelock Couplers are fitted with an Aluminium
Data Plate (FIG 3.0.1). Information pertains to the
product code, the carrier machine, product serial
number, working load limit (for lifting purposes) and
the maximum operating pressure. If any of the cells
are left blank it means that the information is non
applicable to this attachment
WARNING: Wedgelock Quick Couplers that incorporate a factory fitted lifting eye will be labeled
and marked with a Working Load Limit (WLL) of the lifting eye. The lifting eyes are designed in
accordance with NZS/BS2573:Part1. It is highly recommended that a Bow Type Shackle be used to
connect to the lifting eye. See page 15.
3.1 SERVICING SCHEDULE
Maintenance Required
Daily
Weekly
Check all pin retainers, bolts & nuts for tightness on the quick coupler and
the attachments
ü
Lubricate all greasing points – the attachment will have to be removed to
access all grease points.
ü
Check hydraulic hoses and fittings for any leaks or wear – replace
immediately if required
ü
Check the quick coupler switch and audible warning buzzer is operating
properly
ü
Check the full operation of all the moving parts within the quick coupler –
repair or replace immediately if required
ü
Check the hydraulic cylinder mounting bolts for tightness – remedy if
required
ü
Thoroughly clean the quick coupler and ensure there is no material build up
around locking cylinder, wedge or I-Lock™ safety system
ü
Check the quick coupler for evidence of fatigue, weld failure or stress – if
evident contact your Wedgelock dealer immediately for assistance
ü
Fig. 3.0.1
EXAMPLE