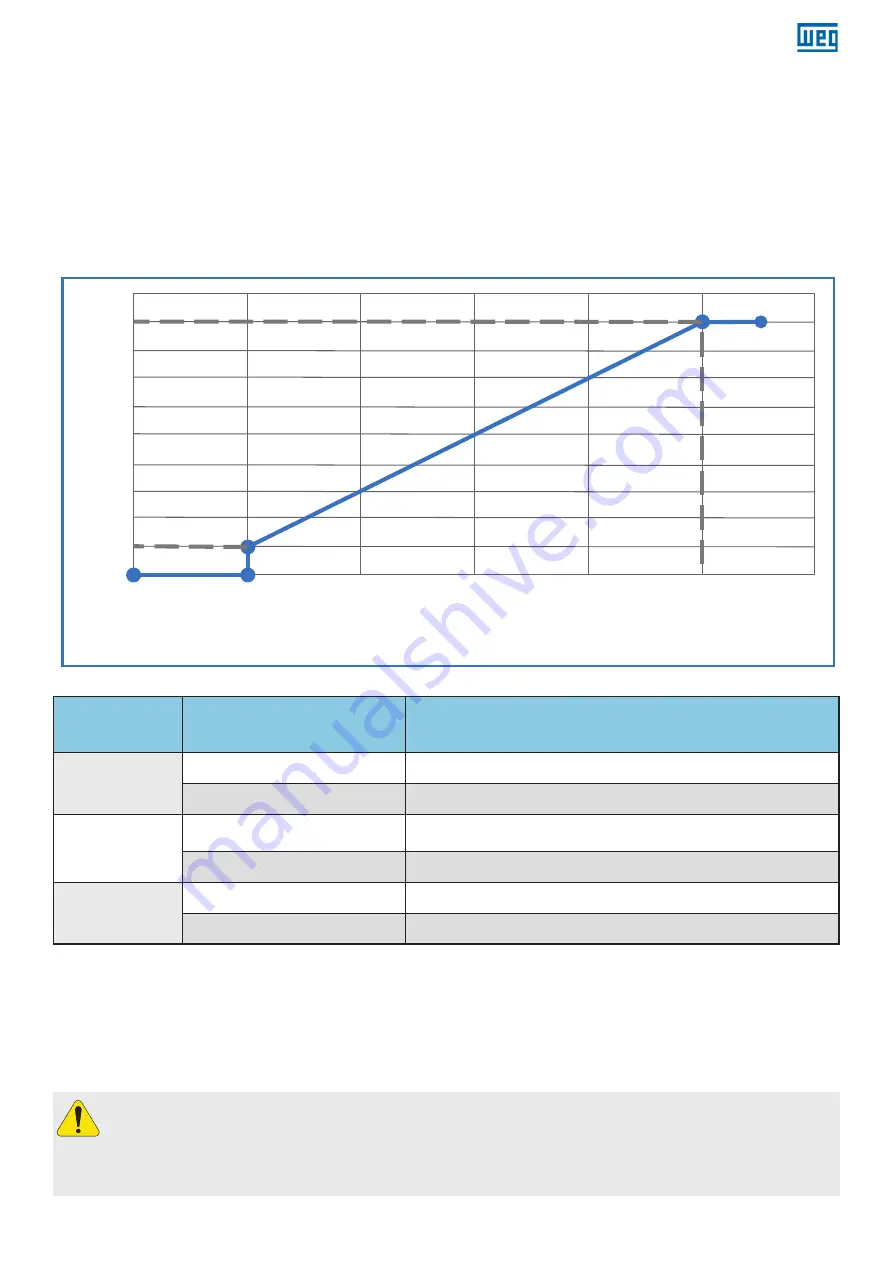
www.weg.net
WECM / Emerald eZA Manual | 9
Remote speed adjusts:
The speed can be adjusted by:
DC voltage: 2 to 10 VDC [tolerance: + 10%].
DC current: 4 to 20 mA DC [tolerance: + 10%].
Frequency duty-cycle / PWM: 10 to 95%
Voltage: 10 to 24 Vpk [tolerance: -5% / + 10%].
Frequency: 80 Hz [tolerance: -2,5% / + 2,5%].
When available, using the RS485 serial communication
(
see item6.7).
The speed can be adjusted using the external speed controller (see item 6.5).
The product will turn off if imposed signals lower than 2 V DC, 4 mA DC or 10%.
10 VDC
20 mA DC
95%
2 VDC
4 mA DC
10%
zero VDC ª
zero mA DC
zero %
min
speed
max
speed
b
c
INPUT SIGNAL
SPEED [rpm]
Figure 6 - Control input reference
Table 5 -
Signal type
Condition
Resulting speed value
DC voltage
a
Lower than 2 VDC
Zero (motor is off)
From 2 to 10 VDC
((Max
b
-Min
c
)/8)×(IS
d
-2)+Min
DC current
Lower than 4 mA DC
Zero (motor is off)
From 4 to 20 mA DC
((Max
b
-Min
c
)/16)×(IS
d
-4)+Min
Frequency
Lower than 10%
Zero (motor is off)
From 10 to 95%
((Max
b
-Min
c
)/85)×(IS
d
-10)+Min
Control input reference
Notes:
a.
The DC voltage signal can be applied by an external power supply or using the built-in 10VDC source and an additional
potentiometer (5 kΩ to 10 kΩ).
b.
Maximum speed adjusted (see item 6.4).
c.
Minimum speed adjusted (see item 6.4).
d.
Input signal (V DC, mA DC, %) supplied to the respective remote input.
ATTENTION!
g
The built-in power supplies have an output limit of:
g
Three-Phase: 10 mA for the 10 VDC and 350 mA for the 24 VDC.
The product can be permanently damaged if imposed signals out of the specification.
Make sure that all unused conductors in control cable are insulated to avoid product malfunction or damage.