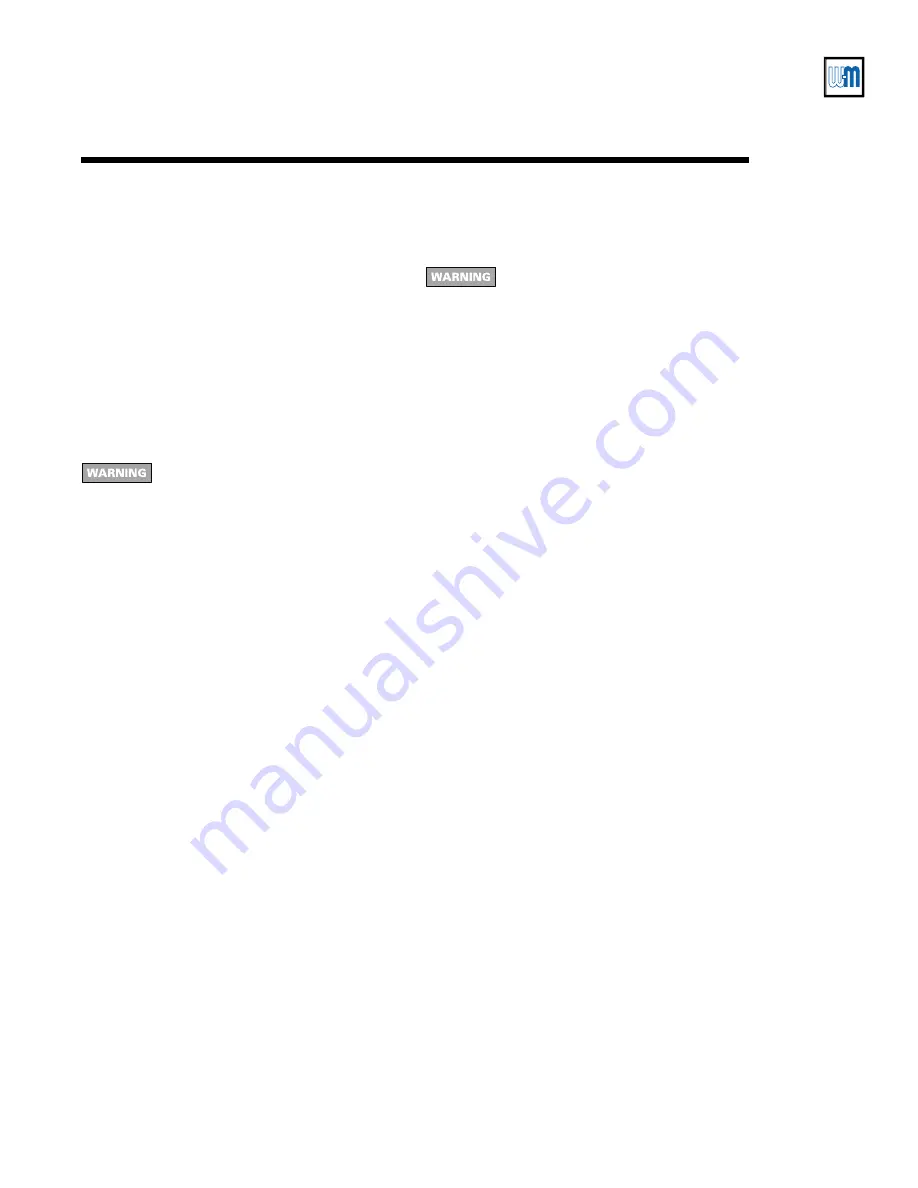
Part number 644-500-065/0200
11
QB-180/300 Oil Burners Series 2
— Burner Manual
Wiring, operation and service
4
Wiring
Wire the burner (and boiler) following instructions in
the burner
Control Supplement
and the
Boiler Manual
.
Service
Electrical shock hazard. Failure to shut
off electrical supply before servicing can
cause severe personal injury, death or
substantial property damage.
1. See
Boiler Service/Maintenance Guide
for details
of annual service call, including cleaning boiler
flueways.
2. Oil blower motor (if required). Refer to motor
name plate/specifications label for any instructions.
3. Replace oil filter cartridge once a year to prevent
fuel oil contamination from plugging fuel pump
and nozzle.
4. Replace nozzle once a year before start up of heat-
ing season. Always use proper nozzle. See
Table 1
on page 6.
5. Check electrode settings once a year. See page 5.
6. Clean fan and blower housing regularly to keep free
of dirt and lint.
7. Check and adjust burner according to
Start-up
pro-
cedures in
Control Supplement
after each servic-
ing.
8. Contact your Weil-McLain distributor for all
burner parts that need replacement.
When servicing a
NO HEAT
call:
Check each item below, making sure to complete
each check before going to the next one.
❏
Thermostat(s).
❏
Main fuse and power supply.
❏
Service switch on boiler.
❏
Oil level in oil tank.
❏
Oil valves.
❏
Limit control.
❏
Primary control.
❏
Motor.
When all of the above checks are made, then refer to
Troubleshooting
on pages 12 and 13.
Start-up
Read the sequence of operation and start-up proce-
dures in the burner
Control Supplement
.
Final Adjustments
You must use
test instruments
to
properly start, check and adjust burner.
Failure to do so could result in severe
personal injury, death or substantial
property damage.
1. Make sure combustion and ventilation air supply
is sufficient for normal appliance operation. Close
windows and doors in appliance area to simulate
normal job condition. Start boiler and allow for a
10-minute warm up.
2. Check for -.01" to -.02" W.C. draft in combustion
chamber. Adjust barometric damper as necessary.
3. Check for 0 smoke.
4. Check for CO
2
between 11% and 12 ½%.
• To
increase
CO
2
,
close
attenuating air band set-
ting.
• To
decrease
CO
2
,
open
attenuating air band set-
ting.
5. Check CO
2
, smoke and draft levels again.
6. Start and stop unit several times.
7. Check operation of limits, thermostats and timing
of combustion control.
8. Check for oil leaks.
9.
Recheck all installations
after one to two weeks of
operation.