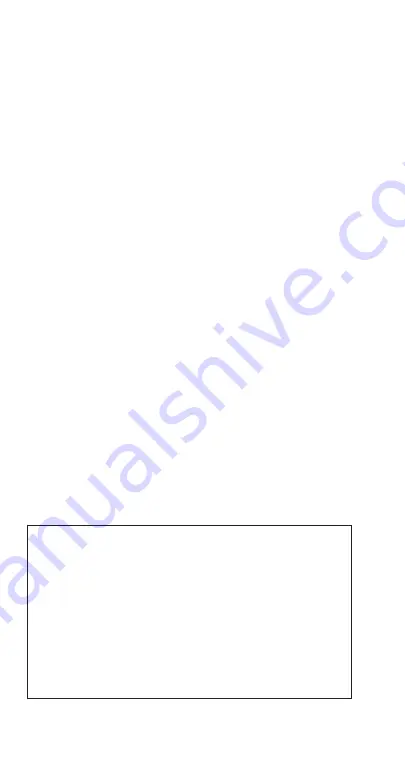
146
Flammable Refrigerant Procedures
Servicing Requirements
• It is recommended that only technicians specifically
trained in handling flammable refrigerants, service
or dispose of equipment containing hydrocarbon
refrigerants.
• Color-coded red process tubes indicate use of a
flammable refrigerant - Process tubes must be
replaced after brazing or other service procedures.
• An accessible fire extinguisher is required when
brazing.
• A combustible gas leak detector with a minimum
sensitivity of 8 grams per cubic meter is required. The
meter must be on while servicing the equipment.
Place the detector on the floor and set the detector to
beep at approximately heart beat rate.
• Equipment using hydrocarbon refrigerants have fittings
unique to flammable refrigerants.
• Work in well-ventilated, open spaces - A ventilation fan
can be used to disperse any residual refrigerant. Place
the fan a minimum of 10’ (3m) away from the work
area.
• Eliminate all ignition sources.
• The filter drier must be replaced whenever the system
is opened to the atmosphere.
Importar
• Remove piercing valves after charging.
• Unit is critically charged. Nitrogen must be purged
through the system while brazing to prevent build up
of copper oxide in the refrigeration system.
• Manifold gauge set must be removed properly to
ensure that no refrigerant contamination or loss
occurs. A quick disconnect is required for the high
side connection.
Summary of Contents for Manitowoc NEO UDP0080A
Page 2: ......
Page 18: ...18 Part Number STH098 06 19 THIS PAGE INTENTIONALLY LEFT BLANK...
Page 74: ...74 Part Number STH098 06 19 THIS PAGE INTENTIONALLY LEFT BLANK...
Page 166: ...166 Part Number STH098 06 19 THIS PAGE INTENTIONALLY LEFT BLANK...
Page 176: ...176 Part Number STH098 06 19 ELECTRONIC CONTROL BOARD UDP0080 1 2 3 4 5 6 7 8 9 10...
Page 179: ......