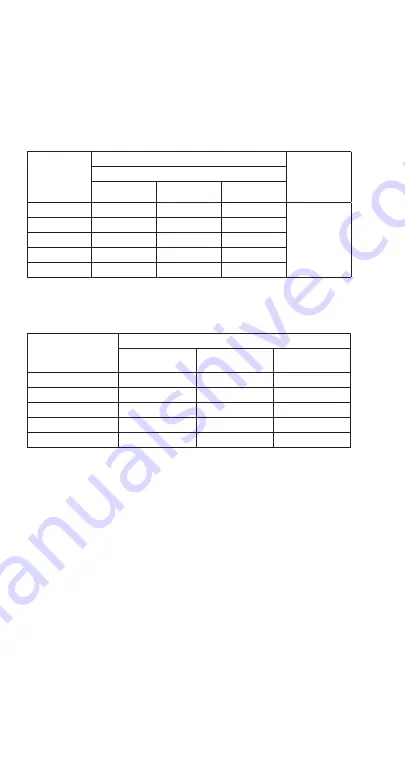
162
UDP0240 SELF-CONTAINED AIR-COOLED
NOTE: These characteristics may vary depending on
operating conditions.
Cycle Times
Freeze Time + Harvest Time = Total Cycle Time
Air Temp.
Around Ice
Machine
°F/°C
Freeze Time
Harvest
Time
Water Temperature °F/°C
50/10
70/21
90/32
70/21
14.1-16.1
17.0-19.3
18.6-21.1
1.0-2.5
80/27
15.2-17.4
18.0-20.5
20.5-23.3
90/32
16.5-18.8
20.5-23.3
22.7-25.8
100/38
19.2-21.8
21.9-24.9
23.6-26.8
110/43
21.9-24.9
23.6-26.8
24.5-27.8
Times in minutes
24 Hour Ice Production
Air Temp.
Around Ice
Machine °F/°C
Water Temperature °F/°C
50/10
70/21
90/32
70/21
225
190
175
80/27
210
180
160
90/32
195
160
145
100/38
170
150
140
110/43
150
140
135
Based on average ice slab weight of 2.44 - 2.75 lb (1107 – 1247 g).
Summary of Contents for Manitowoc NEO UDP0080A
Page 2: ......
Page 18: ...18 Part Number STH098 06 19 THIS PAGE INTENTIONALLY LEFT BLANK...
Page 74: ...74 Part Number STH098 06 19 THIS PAGE INTENTIONALLY LEFT BLANK...
Page 166: ...166 Part Number STH098 06 19 THIS PAGE INTENTIONALLY LEFT BLANK...
Page 176: ...176 Part Number STH098 06 19 ELECTRONIC CONTROL BOARD UDP0080 1 2 3 4 5 6 7 8 9 10...
Page 179: ......