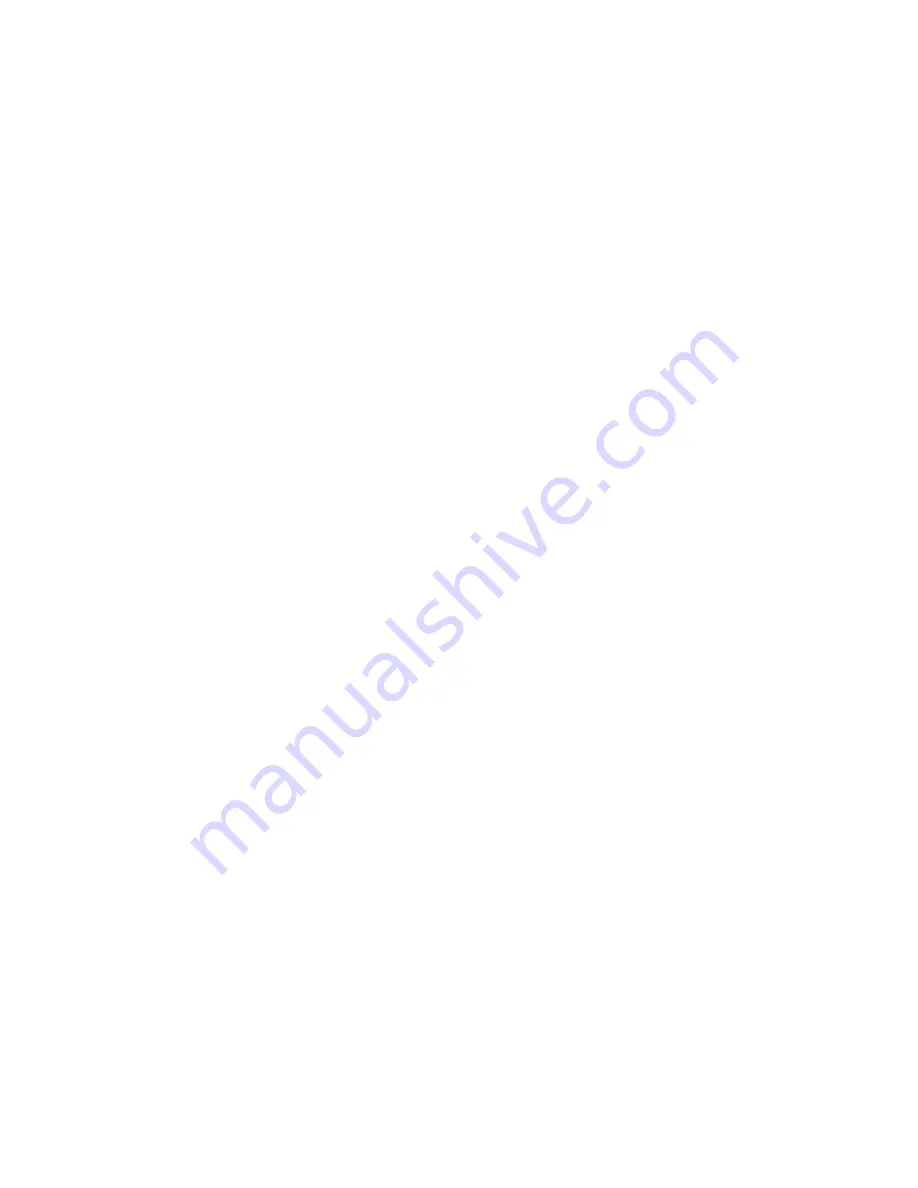
10
3.203 Forced Oil Flushing Procedure
1. Check the oil level, if the oil level is well above the fi ll mark (This may indicate either the pump has been
overfi lled with oil or has ingested a liquid or a large amount of vapor water or organic solvents). Please go to step
2. If the oil level is even with the fi ll mark and you do NOT suspect corrosive gases or particulates (hence forth
called contaminants) ingested have damaged the mechanism, run the pump for 15 minutes to allow the pump oil
to warm up before going to step 2.
2. Turn off motor for the vacuum pump. Drain the oil into a clear plastic container (may need pliers to open drain
valve). Look for contaminations settling to the bottom of container. If you see contaminants, you will need to
repeat step 3 through 5 several times until the oil comes out clear. The oil you drained from the pump came from
the oil case only. There may be contaminants in the pumping mechanism. To be sure all contaminants have
been removed, the pump mechanism needs to be fl ushed.
3. Make sure the belt guard is installed before proceeding further. Attach a short hose to the drain valve which
runs into a clear plastic container.
4. Flushing the pump is carried out by adding a cup of DUOSEAL vacuum pump oil through the intake port (IN)
while the pump is turned on for 15 to 20 seconds. While adding the pump oil, the palm of your hand is placed
lightly over the exhaust port (OUT). Look for water coming out of the drain. Turn off the pump.
5. Repeat step 4 until clean oil comes out of the drain hose.
6. Close the drain valve and fi ll the pump with the amount of DUOSEAL vacuum pump oil your pump needs.
7. Plug the intake (IN) port with a rubber stopper. Turn the pump on and run the pump for 10 minutes. Close the
gas ballast.
8. Check the vacuum reading of the pump by connecting a thermocouple gauge tube to the pump’s intake. If the
pump is running nearly as good as when it was new, the total pressure reading you will read on wither of these
two gauges will be at least 10 micron.
A simple way to connect the gauge tube to the pump is to run the threaded tip of tube through a hole in a rubber
stopper. Use pump oil as a lubricant for inserting the tube. The stopper chosen should be bigger than the outer
diameter of the intake fl ange.
3.204 Refi lling The Pump
After you are satisfi ed that the pump has been thoroughly fl ushed, refi ll the pump by pouring new DUOSEAL oil
into the exhaust port. Fill to the indicated level and start the pump with the intake closed. A gurgling noise is
characteristic when high pressure air is drawn through the pump. It should disappear quickly as the pressure
within the pump is reduced. If gurgling continues, add suffi cient additional oil through the exhaust port until
gurgling ceases.
3.30
Shaft Seal Replacement
To replace the shaft seal of a pump, drain the oil and remove the pump pulley and key. Remove the screws
securing the old seal and pry it loose with a screwdriver or similar wedge, being careful not to mar the surface of
the pump body against which the seal fi ts. Discard the seal and its gasket, inspect all surfaces and repair any
damages with a fi ne abrasive stone. Wipe all sealing areas clean and place a fi lm of DUOSEAL oil on both the
shaft and the inside bore of the new shaft seal. Using a new gasket, carefully slide the new seal into position
and center it on the shaft. It is not necessary to apply any sealant to the gasket. Tighten the mounting screws
uniformly and refi ll the pump with DUOSEAL oil. Follow instructions included in repair kit.