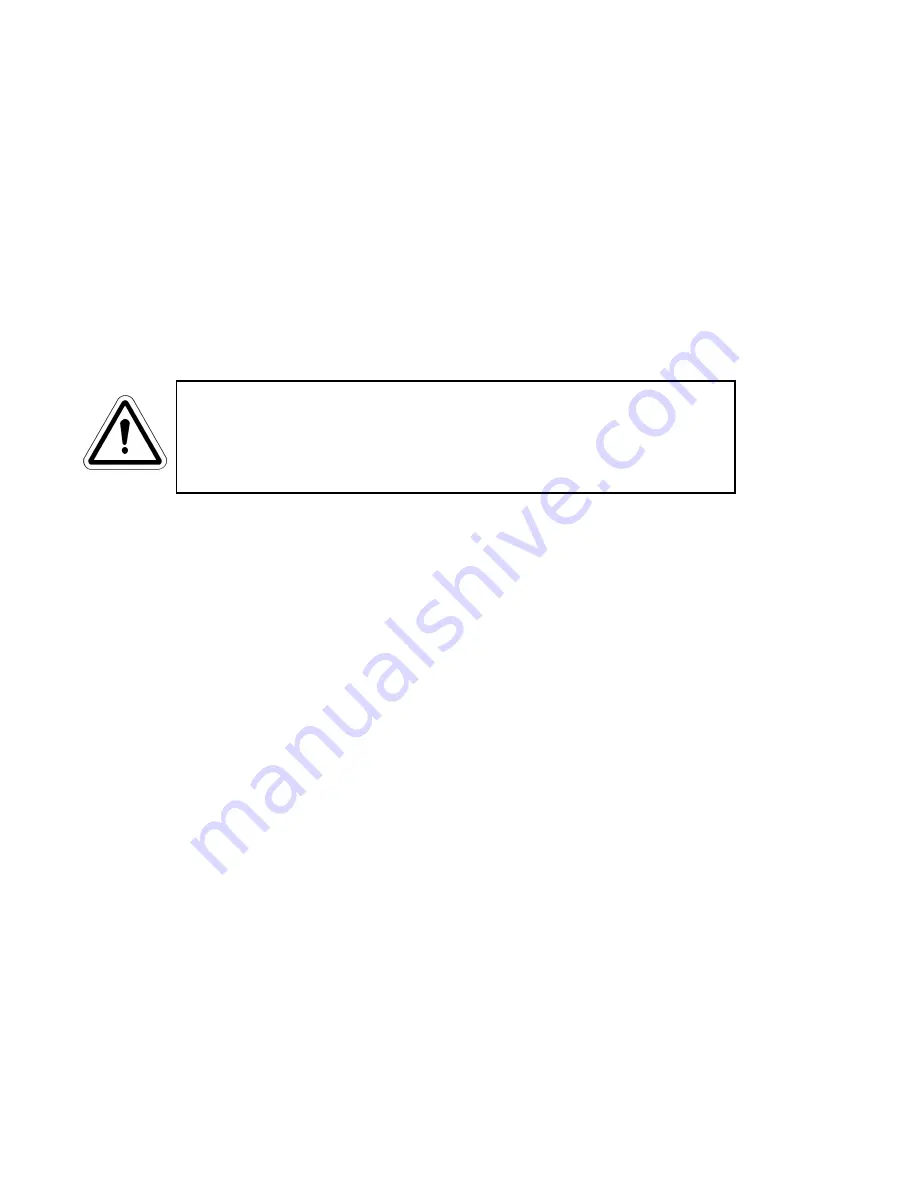
Section 3: OPERATION
3.10
Starting Procedures
3.11
Starting a Welch Dry Vacuum Pump
Before attaching the pump to a system it is well to familiarize yourself with the function and action of the
pressure vacuum pump that you have acquired. Review the power requirements as described in Section 2.6.
Welch recommends running the pump for a few minutes to warm up before use. The warm-up improves the
pump’s ability to handle humid air.
3.12
Cleanliness
Take every precaution to prevent foreign particulates from entering the pump. Particulates will damage the
pump’s performance. If you find that particulates will come off the process during evacuation, a particle trap
in the foreline will work. A simple, inexpensive trap may be made by placing glass wool in a glass or plastic
tube. Screens must be inserted to hold the glass wool in place.
WARNING
The Pump is not recommended for pumping acid, base or organic vapors or
gases. Serious damage to the pump will shorten the pump’s service life.
In addition, pumping flammable vapors or gases can lead to serious safety
hazard leading to fire or explosion.
3.13
Leak Detection
The importance of eliminating all leaks in a vacuum system is obvious. The pump must remove this added
volume of leaked gas to maintain the desired vacuum. Leaks for these pumps can be located by slightly
pressuring the system and painting the suspected area with a thick soap solution. Escaping air will produce
soap bubbles.
3.14
Operating Pressure Range
Models 2560, 2561, 2565, 2580, 2581 and 2585 Dry Vacuum Pumps are designed to be run from atmospheric
to their maximum vacuum level on the intake side. Consult the Specification Table in the back of this manual
for the ratings for your specific model.
3.15
Shutdown Procedures
After use, Welch recommends the pump be run for about 2 minutes disconnected from the vacuum process.
The air pumped through the mechanism will purge out water vapor or droplets of water condensate that may
have formed on the inside of the pump. This purge of the pump mechanism helps prevent corrosion.
Section 4: MAINTENANCE
Welch dry pressure\vacuum units are 100% oil-free. The pump employs a non-lube piston and cylinder. No
maintenance is necessary for the bearings. All bearings are sealed and permanently lubricated. Lubrication
should not be attempted. The units are built for continuous duty operation with the quietness and durability of
a diaphragm, but with piston p
8
Summary of Contents for 2560
Page 11: ...6 11 Pumping Speed Curves 11 ...
Page 21: ...21 ...