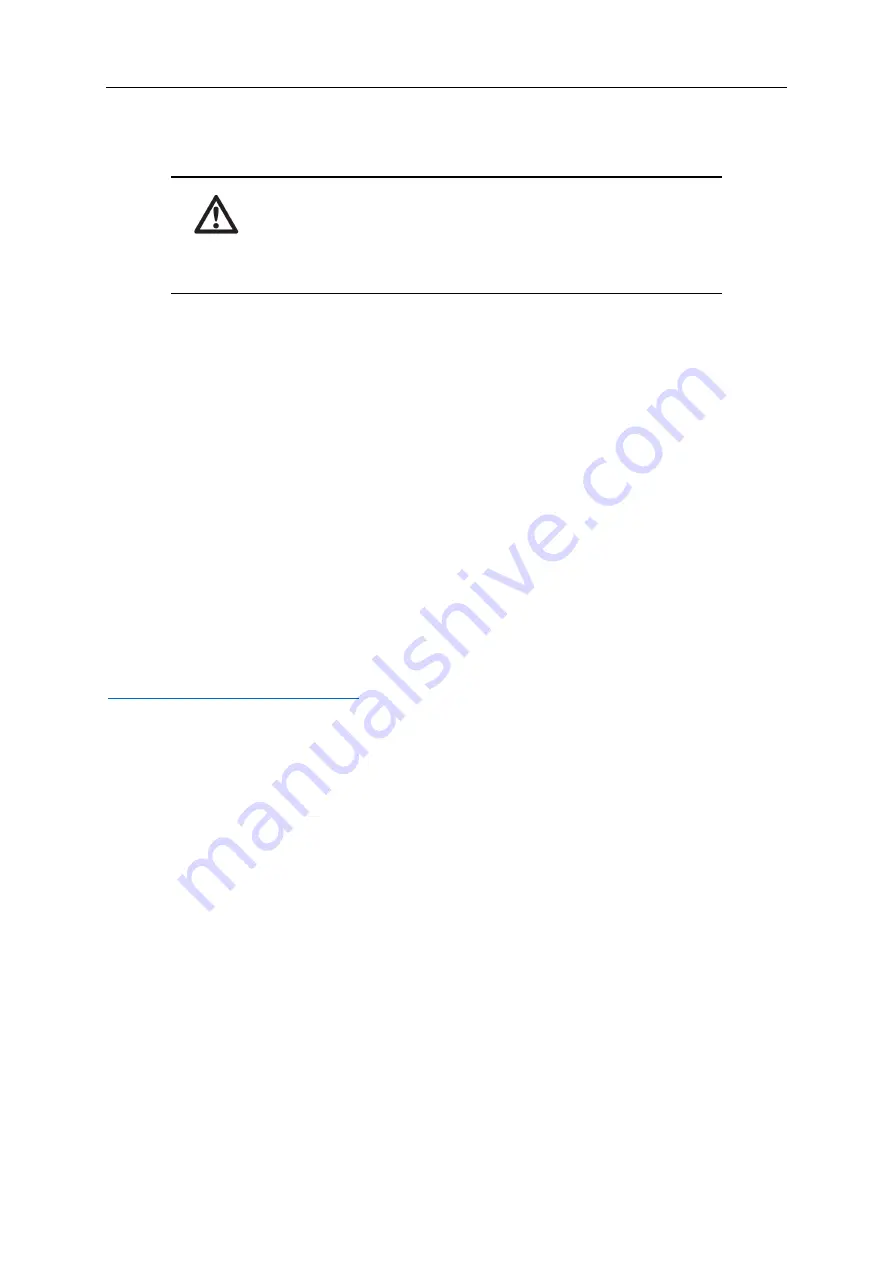
Weldforce 155
M &
175
MST
© Weldclass 2020 | E.&O.E.
67
15.4.9
Gas Cylinders
WARNING!
Gas cylinders contain gas under high pressure. If damaged, a
cylinder can explode. Since gas cylinders are normally part of the welding process, be
sure to treat them carefully.
1.
Protect compressed gas cylinders from excessive heat, mechanical shocks, and arcs.
2.
Install and secure cylinders in an upright position by chaining them to a stationary support or
equipment cylinder rack to prevent falling or tipping.
3.
Keep cylinders away from any welding or other electrical circuits.
4.
Never allow a welding electrode to touch any cylinder.
5.
Use appropriate shielding gas, regulators, hoses, and fittings designed for the specific application;
maintain them and their associated parts in good condition.
6.
Turn your face away from the valve outlet when opening the cylinder valve.
16
WARRANTY
16.1
Warranty Information
For full details on warranty period and terms and conditions, go to
www.weldclass.com.au/WarrantyInfo