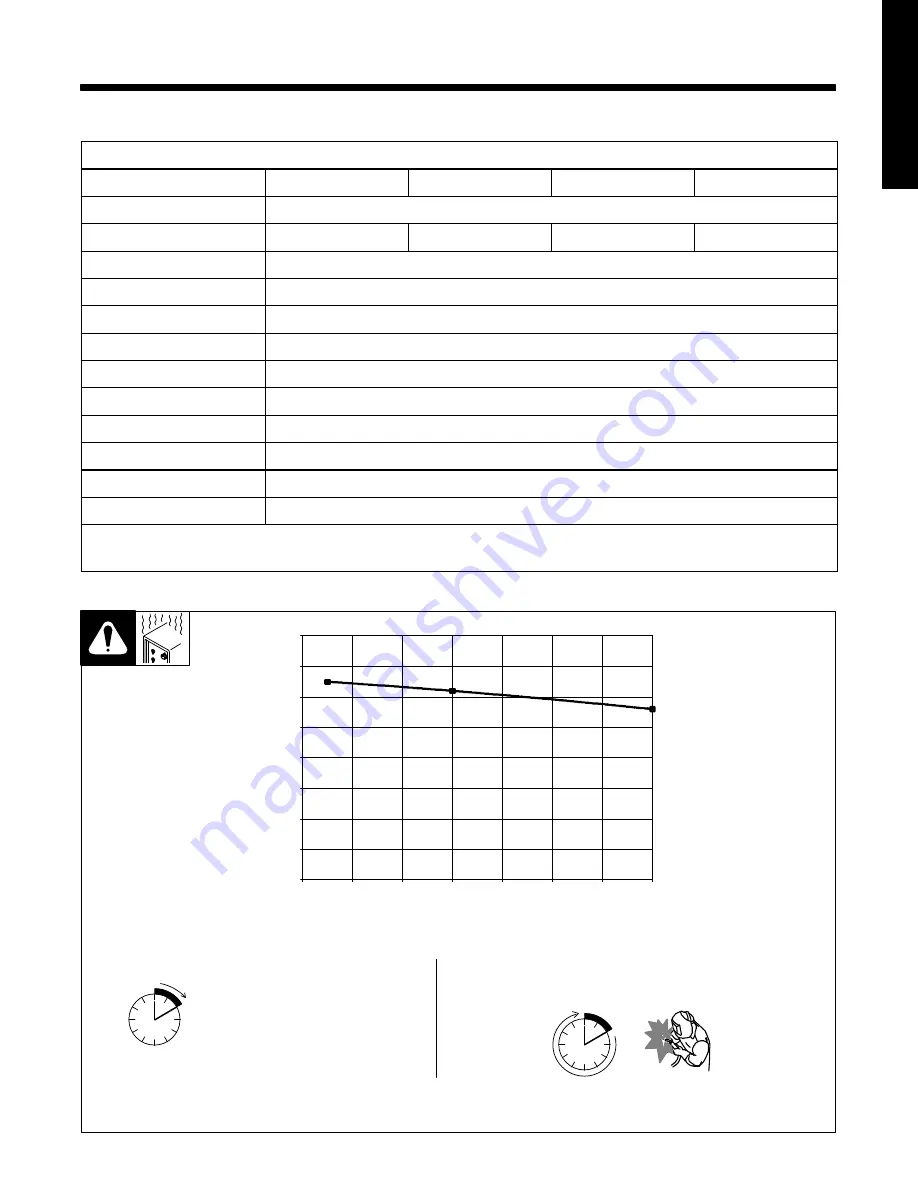
ENGLISH
OM-254 691 Page 3
SECTION 2
−
SPECIFICATIONS
2-1. Specifications
Model
WP-280-12-RM
WP28012RMD50
WP-280-25-RM
WP28025RMD50
Max Rating*
280 Amps
Length
12.5 Ft (3.7 m)
12.5 Ft (3.7 m)
25 Ft (7.6 m)
25 Ft (7.6 m)
Hose/Cable Options
Tri-Flex
Braided Rubber
Cooling Method
Liquid (Distilled/Deionized Water or Low Conductivity Coolant, Miller Part No. 043 810)
Electrode Range
.020 in. Thru 1/8 in. (0.5 Thru 3.2 mm)
Dimensions
Length 7 in. (178 mm); Handle Diameter 7/8 in. (22.2 mm); Weight 4.1 oz (117 g)
Method Of Guidance
Manual/Hand Held
Peak Voltage Rating
113 V
Peak Striking/Stability Voltage
15 KV
Min Flow Rate
.25 GPM
Min And Max Inlet Pressure
.379 MPa (55 psi) Min; .482 MPa (70 psi) Max
Min Cooling Power
2620 W
* Max rating based on 25
C (77
F) environment at maximum handle temperature rise of 30
C (86
F) or power cable temperature rise of 40
C (104
F). 100% Argon gas, 100% duty cycle, 1/8 in. (3.2 mm) 2% Ceriated electrode and Miller Coolmate
4.
2-2. Duty Cycle
Continuous Welding
sb1.5* 8/93
100% Duty Cycle At 280 Amperes Using Argon Gas For 25 Ft Models
Duty Cycle is percentage of 10
minutes that torch can weld at
rated load without overheating.
0
10
Minutes
Definition
NOTICE
−
Exceeding rated amperage can damage torch and void warranty (see Section 2-1).
100% Duty Cycle At 280 Amperes Using Argon Gas For 12 Ft Models
0
50
100
150
200
250
300
350
400
30
40
50
60
70
80
90
100
Amperage
A
Duty Cycle %
Summary of Contents for WP-280-12-RM
Page 4: ......
Page 17: ...OM 254 691 Page 13 Notes...
Page 21: ...ENGLISH Notes...
Page 22: ...ENGLISH Notes...
Page 23: ...ENGLISH Notes...