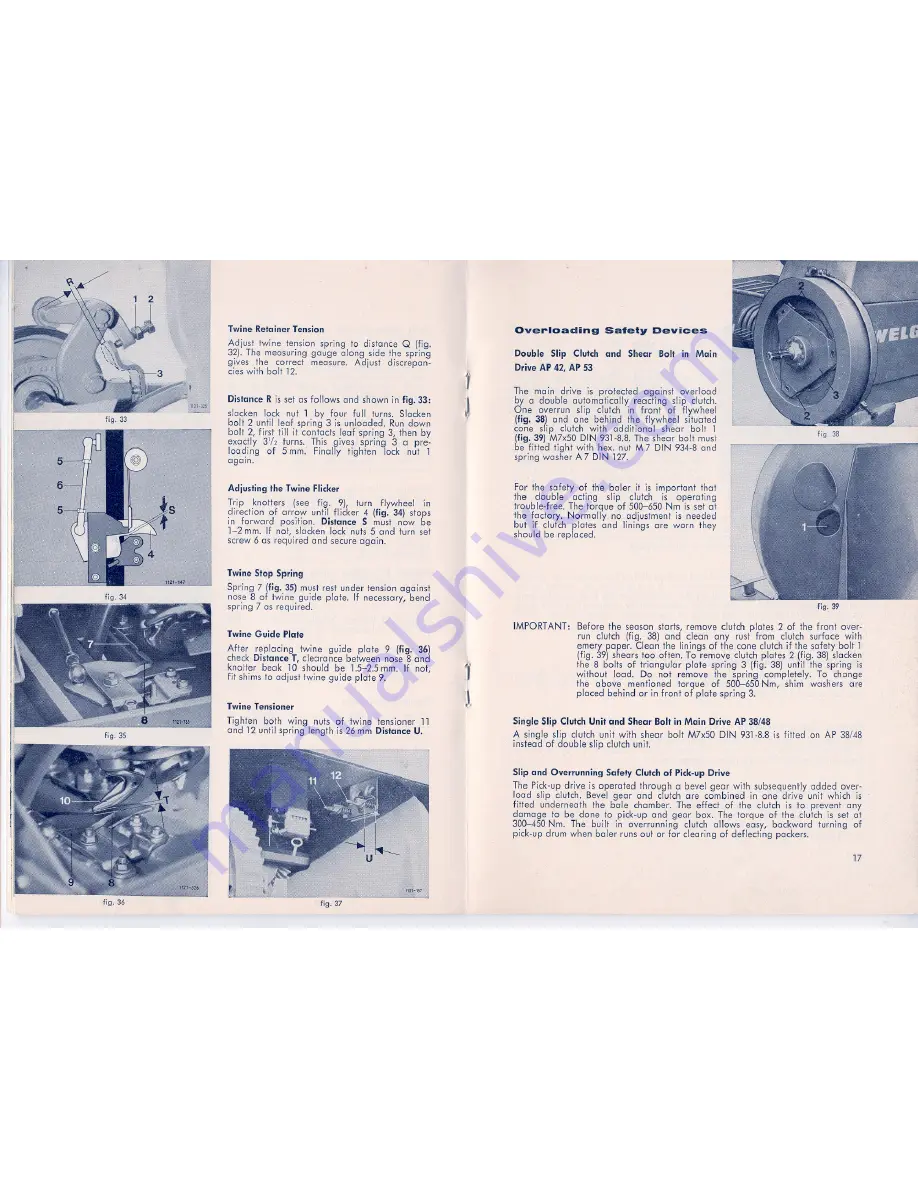
~
fig.36
Twine Retainer Tension
Adjust twine tension spring to distance
Q (fig.
32).The
measuring gauge along side the spring
gi,ves the correct measure. Adjust discrepan-
eies with holt 12.
Distance R is set as fellows end shown in fig.33:
glocken lock nut 1 by tour full turns. Slacken
holt 2 until leGt spring 3 is unloaded. Run down
holt 2, first till it contacts leGt spring 3, then by
exactly 3'/2 turns. This gives spring 3 a pre-
loading
of 5 mm. Finally fighten lock nut 1
again.
Adjusting the Twine Flicker
Trip knotters
(see fig. 9), turn flywheel in
direction of arrow until flicker 4 (fig. 34) stops
in forward position. Distance S must now be
1-2 mm. If not, glocken lock nuts 5 end turn set
screw 6 as required end secure again.
Twine Stop Spring
Spring 7 (fig. 35) must rest under tension against
nase 8 of twine guide plate.
If
necessary, bend
spring 7 as required.
Twine Guide fiale
After replacing twine guide plate 9 (fig.
36)
check
DistanceT, clearance between nase 8 end
knotter heck 10 should be
1.5-2.5
mm. If not,
fit shims to adjust twine guide plate 9.
Twine Tensioner
Tighten both wing nuts of twine tensioner 11
end 12 until spring length is 26 mm Distance U.
fig. 37
j
~~
~
~
Overloading
Safety
Devices
Double Slip Clutch and
ShearBolt
in Main
Drive
AP 42, AP 53
The mein drive
is
protected
against overload
by d double automatically
reacting slip clutch.
. One
overrun
slip clutch in front
of flywheel
(fig.
38) end one behind ihe flywheel
situated
cone slip clutch with
additional
shear holt
1
(fig.
39) M7x50 DIN 931-8.8. The shear holt musr
.be fitted light with hex. nut M 7 DIN
934-8
end
spring washer A 7 DIN 127.
For the safety of the baler it is important
thaI
the
double
acting
slip
eluIeh
is
operating
trouble-free. The torque of
500-650
Nm is se,t at
the factory. Normally
no adjustment is needed
hut if clutch plates end linings are warn they
should be replaced.
IMPORTANT:
fig. 38
fig..39
Before the sepsen starts, remove clutch plates 2 of the front. over-
run clutch (fig. 38) end clean any fUgt from
clutch surface with
emery paper. Clean the linings of the cone eluIeh if the safety holt 1
(fig. 39) shears tao offen. T0 remove clutch plates 2 (fig. 38) glocken
the 8 halts of triangular
pfote spring 3 (fig. 38) until the spring is
without
load.
Do not remove the spring completely.
To chonge
the above
mentioned
torque
of
500,...650Nm, shim washers are
placed
behind or in front of plate spring 3.
Single Slip Clutch Unit and Shear Bolt in Main Drive AP
38/48
A single slip alutch unit with shear holt
M7x50
DIN
931-8.8is
fitted on AP 38/48
instead of double slip clutch unit.
Slip and Overrunning
Safety Clutch of Pick-up Drive
The Pick-up drive
is
operated through abevel
geer with subsequently added over-
load slip oIutch. Bevel geer end eluIeh are combined in one drive unit
which
is
fitted
underneath
the ba,le chamber. The effect of the clutch is to prevent any
damage to be düne to pick-up end geer box. The torque of the eluIeh is set at
300-450
Nm. The built in overrunning
cluleh pIlaws easy, backwardturning
of
pick-up drum when baler runs out or für clearing of deflecting packers.
17
Summary of Contents for AP 38
Page 1: ......