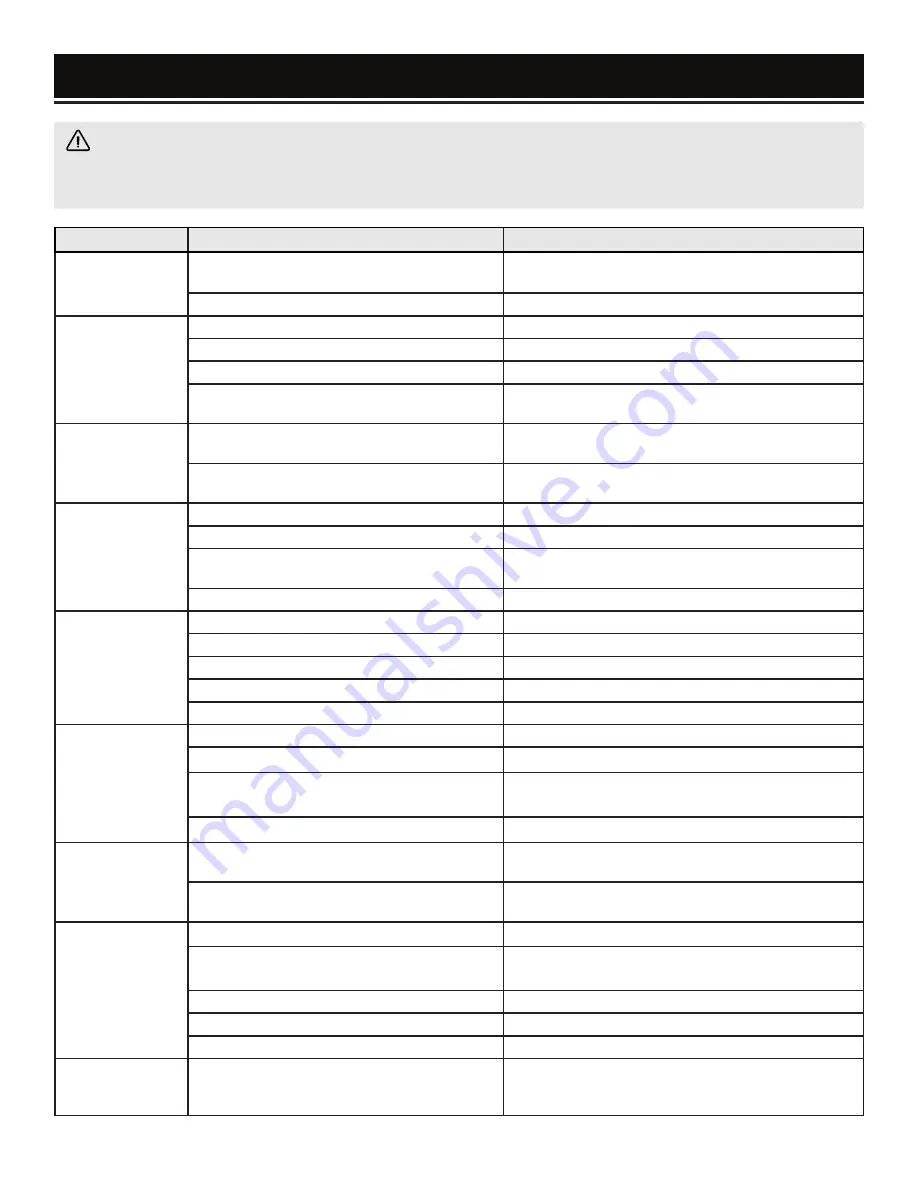
14
TROUBLESHOOTING GUIDE
WARNING!
Stop using the tool immediately if any of the following problems occur. Repairs and replacements
should only be performed by an authorized technician. For any questions, please contact our customer service
at (800) 232-1195, M-F 8-5 CST or email us at
techsupport@wenproducts.com.
PROBLEM
CAUSE
SOLUTION
Sanding grains
easily rub off.
1. Sanding belt / sleeve has been stored in the wrong
environment.
1. Store sanding accessories away from extremely hot/dry
temperatures.
2. Sanding belt / sleeve has been damaged or folded.
2. Call customer service (1-800-232-1195) for assistance.
Deep sanding
grooves or scars in
workpiece.
1. Sanding belt / sleeve grit is too coarse.
1. Use a finer-grit sanding accessory.
2. Workpiece sanded across the grain.
2. Sand with the grain of the wood.
3. Too much sanding force on workpiece.
3. Reduce pressure on workpiece while sanding.
4. Workpiece held still against sanding surface for too
long.
4. Keep workpiece moving while sanding on the sanding
accessory.
Sanding surface
clogs quickly
1. Too much pressure against belt/spindle.
1. Clean sanding belt / sleeve and then reduce pressure on
workpiece while sanding.
2. Sanding softwood.
2. Use different stock / sanding accessories or clean / remove
sanding sleeves frequently.
Burns on
workpiece
1. Use a sanding grit that is too fine.
1. Use a coarser-grit sanding accessory.
2. Using too much pressure.
2. Reduce sanding pressure on workpiece.
3. Work held still for too long.
3. Keep workpiece moving while sanding on the sanding
accessory.
4. Sanding belt / sleeve loaded with debris.
4. Clean or replace the sleeve or belt.
Sander does not
turn on
1. Not plugged in to an electrical outlet.
1. Connect the unit to an outlet.
2. Defective power switch.
2. Call customer service (1-800-232-1195) for assistance.
3. Onboard circuit breaker tripped.
3. Press circuit breaker to reset.
4. Carbon brushes worn down
4. Call customer service (1-800-232-1195) for assistance.
5. Motor or wiring problem.
5. Call customer service (1-800-232-1195) for assistance.
Motor will not
start—fuses or
circuit breakers
tripping/blowing
1. Short circuit in line, cord or plug.
1. Inspect cord / plug for damaged insulation / shorted wires.
2. Short circuit or faulty circuit breaker.
2. Call customer service (1-800-232-1195) for assistance.
3. Incorrect fuses or circuit breakers in power line.
3. Install correct fuses or circuit breakers or switch tool to an
appropriately sized circuit.
4. Carbon brushes worn down.
4. Call customer service (1-800-232-1195) for assistance.
Motor overheats
1. Motor overloaded.
1. Reduce sanding pressure on workpiece and take more
frequent breaks.
2. Extension cord too long with an insufficient gauge. 2. Refer to section “Guidelines and Recommendations for
Extension Cords” on page 8.
Sander vibrates
excessively or has
noisy operation.
1. Sanding belt / sleeve out of balance/loose.
1. Ensure sleeve / belt is properly installed.
2. Motor or component loose.
2. Inspect / replace damaged bolts / nuts and retighten with
thread-locking fluid.
3. Pulley loose.
3. Re-align / replace shaft, pulley set screw and key.
4. Machine incorrectly mounted to bench.
4. Adjust anchor bolts. Tighten mounting hardware.
5. Faulty motor bearings.
5. Call customer service (1-800-232-1195) for assistance.
Sander turns on but
spindle does not
spin / oscillate.
1. Broken / worn belt.
1. Call customer service (1-800-232-1195) for assistance.
Summary of Contents for HA5932
Page 19: ...19 NOTES ...
Page 20: ...THANKS FOR REMEMBERING ...