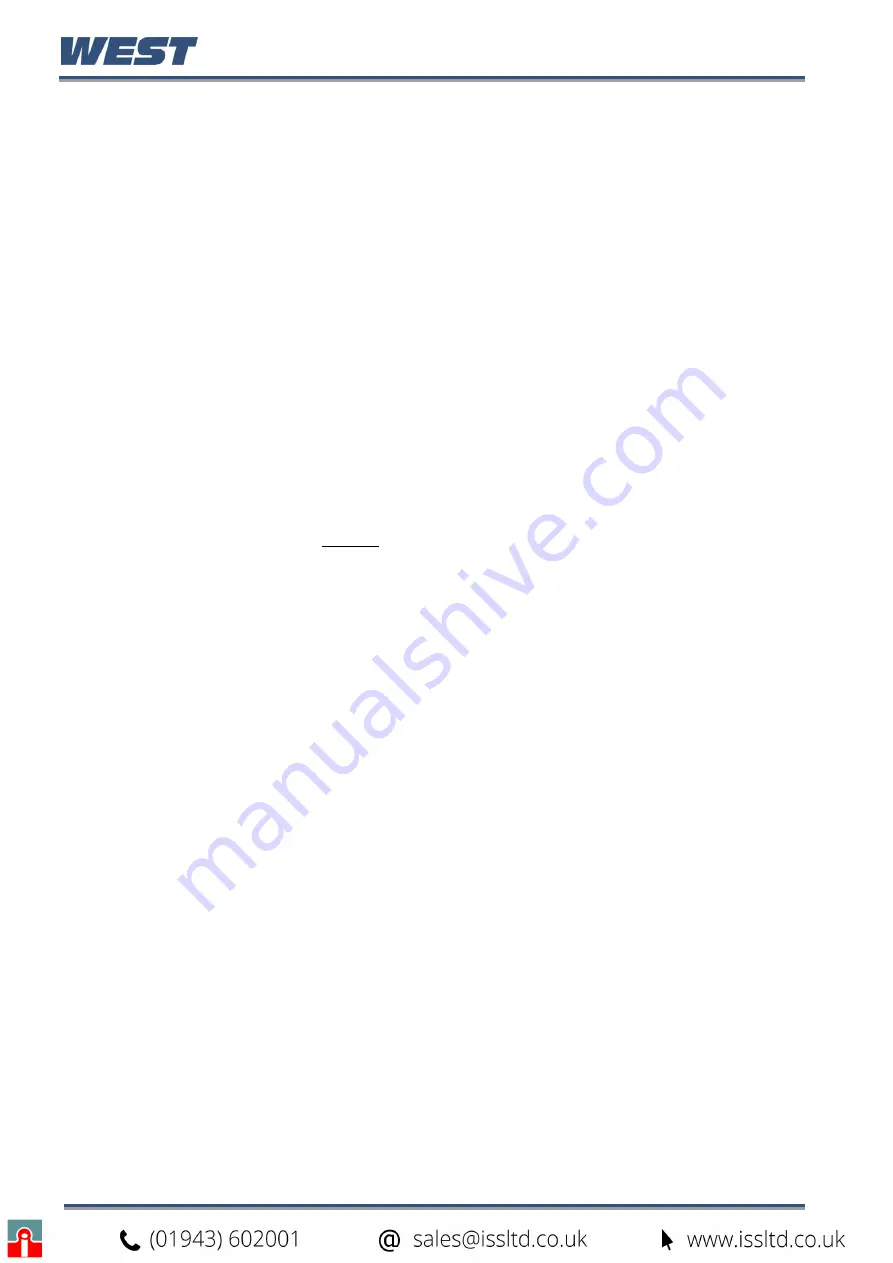
Pro-EC44 2-Loop Graphical Profile Controller & Recorder
Pro-EC44 Product Manual - 59540-2 September 2014
Page 234
Triac
A small internal solid state relay, which can be used in place of a mechanical relay for low
power AC switching (0.1 to 1 amp AC). Like a relay, the output is time proportioned.
However, as solid-state devices, triacs do not suffer from contact degradation so much faster
switching cycle times are possible, offering improved control and reliability. A snubber should
be fitted across inductive loads to ensure reliable switch off the triac.
Also refer to: Cycle Time; Relay; SSR and Time Proportioning Control.
USB Menu
A lock-code protected USB menu is offered from the main menu for the USB option. This
allows the user to read or write files to a USB memory stick. The current configuration of the
instrument can be copied to the stick, or the instrument can be reconfigured from a file
created using the PC software or copied from another instrument. Profiles can also be copied
from the instrument to a USB stick or you can upload pre-stored files created earlier from the
PC software or copied from another instrument.
Data recordings can be copied to the stick for later analysis on a PC.
Refer to the USB Menu information in the Configuration & Use section.
Also refer to: Data Recorder; Lock Codes; Main Menu; PC Software and Profiler
Valve Motor Drive Control (VMD)
This control mode is used when directly controlling the motor of a modulating valve or
damper. It uses a 3-point stepping Valve Motor Drive control algorithm to open or close the
valve. VMD mode is not suitable if the modulating valve has its own positioning circuit (use
standard control with a continuous current proportioned linear output) or solenoid valves (use
standard control with a time proportioned output).
Also refer to: Continuous Control; Linear Output; Modulating Valve; Solenoid Valve; Three
Point Stepping Control and Time Proportioning Control.
Valve Position or Flow Indication
The valve motor drive control mode does not require any kind of position feedback in order to
correctly control the process. However, where potentiometer feedback or (mA or VDC) flow
signals are available, they can be connected to the 2
nd
input to indicate valve position or flow
level. The display is a percentage (0 to 100%) shown as a bar-graph in the main operator
mode screen.
Even if position feedback is provided, it is not used by the VMD control algorithm when
positioning the valve, thus avoiding problems associated with faulty feedback signals.
Also refer to Auxiliary Input; Bar-graph; Display Strategy; Open Loop VMD; PID; Set Valve
Closed Position; Set Valve Open Position; Setpoint; and Valve Motor Control.
Valve Open & Closed Limits
When valve position indication is used in VMD control mode, the valve limit parameters can
be used to
“clamp” the maximum and minimum valve positions. The controller will not
attempt to drive the valve past these points.
The position indication input must correctly scaled using
“set valve open” and “set valve
closed
” before using the valve limits.
Also refer to Set Valve Closed Position; Set Valve Open Position; Valve Motor Control and
Valve Position Indication.
Summary of Contents for Pro-EC44
Page 1: ...Pro EC44 2 Loop Graphical Profile Controller Recorder Pro EC44 User Guide 59540 2 ...
Page 2: ......
Page 6: ......