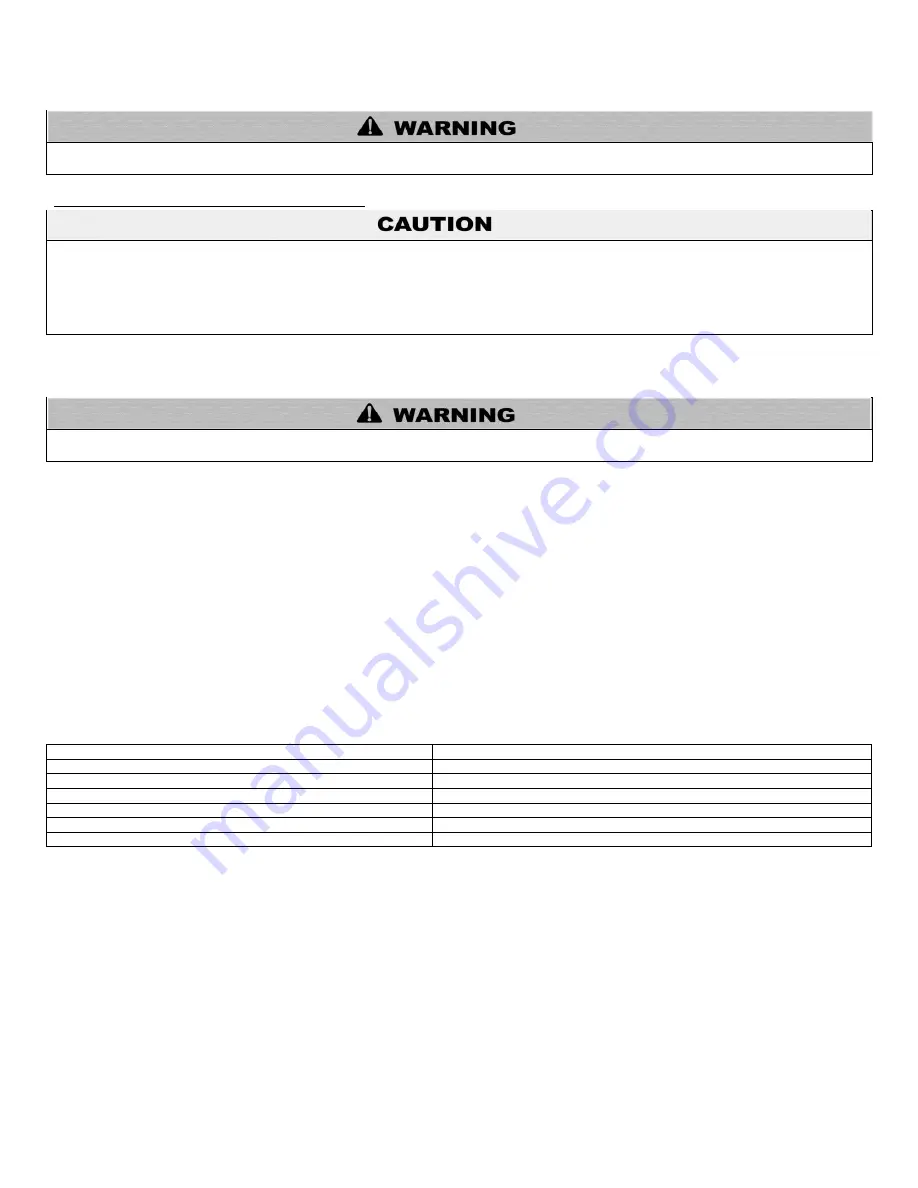
61
WHL-016 REV. 12.18.14
PART 9 – START-UP PREPARATION
Thoroughly clean and flush any system that has used glycol before installing the boiler. Provide the customer with a material safety
data sheet (MSDS) on the fluid used.
A. CHECK / CONTROL WATER CHEMISTRY
Chemical imbalance of your water can cause severe damage to your boiler and associated equipment, and may also affect efficiency.
You may have to have your water quality professionally analyzed to determine whether you need to install a water softener. It is
important that the water chemistry on both the domestic hot water and central heating sides are checked before installing the boiler, as
water quality will affect the reliability of the system. Outlined below are those water quality parameters which need to be met in order for
the system to operate efficiently for many years.
Failure of a heat exchanger due to lime scale build-up on the heating surface,
low pH or other imbalance IS NOT covered by the warranty.
To assure good extended service life, it is recommended that you test your water quality prior to installation. Listed below are some
guidelines.
Do not use petroleum-based cleaning or sealing compounds in the boiler system. Damage to elastomer seals and gaskets in the
system could occur, resulting in substantial property damage.
Sodium less than 20 mGL
Water pH between 6 and 8
1. Maintain boiler water pH between 6 and 8. Check with litmus paper or have chemically analyzed by water treatment company.
2. If pH differs from above, consult local water treatment company for treatment needed.
Hardness less than 7 grains
Consult local water treatment companies for unusually hard water areas (above 7 grains hardness).
Chlorine concentration less than 100 ppm
1. Filling with chlorinated fresh water should be acceptable since drinking water chlorine levels are typically less than 5 ppm.
2. Do not use the boiler to directly heat swimming pool or spa water.
3. Do not fill boiler or operate with water containing chlorine in excess of 100 ppm.
ACIDITY
6 to 8 pH
CONDUCTIVITY
Less than 400 uS/cm at 25
o
C
CHLORIDE
Less than 100 ppm
IRON
Less than 0.5 mg/L
COPPER
Less than 0.1 mg/L
SODIUM
Less than 20 mg/L
HARDNESS
Less than 7 Grains
Table 16
Clean system to remove sediment*
1. You must thoroughly flush the system (without boiler connected) to remove sediment. The high-efficiency heat exchanger can be
damaged by buildup or corrosion due to sediment.
2. For zoned systems, flush each zone separately through a purge valve. (If purge valves and isolation valves are not already installed,
install them to properly clean the system.)
3. Flush system until water runs clean and you are sure piping is free of sediment.
*NOTE:
It is recommended you clean heat exchanger at least once a year to prevent lime scale buildup. Follow the maintenance
procedure to clean the heat exchanger in the Maintenance Section (Part 14 of this manual).
Test/replace freeze protection fluid
1. For systems using freeze pro
tection fluids, follow fluid manufacturer’s instructions to verify inhibitor level and that other fluid
characteristics are satisfactory.
Summary of Contents for WBCNG399W
Page 14: ...14 WHL 016 REV 12 18 14 SPECIFICATIONS AND DIMENSIONS Figure 2 Specifications and Dimensions ...
Page 24: ...24 WHL 016 REV 12 18 14 Figure 8 Piping Symbol Legend ...
Page 59: ...59 WHL 016 REV 12 18 14 Figure 32 Cascade Master and Follower Wiring ...
Page 60: ...60 WHL 016 REV 12 18 14 Figure 33 Internal Connection Diagram LP 293 J ...
Page 83: ...83 WHL 016 REV 12 18 14 055 080 110 PARTS BREAKDOWN Figure 36 Replacement Parts LP 387 J ...
Page 85: ...85 WHL 016 REV 12 18 14 155 199 285 399 PARTS BREAKDOWN ...
Page 86: ...86 WHL 016 REV 12 18 14 Figure 38 Replacement Parts LP 387 KK ...
Page 87: ...87 WHL 016 REV 12 18 14 155 199 285 399 MODEL PARTS BREAKDOWN ...
Page 91: ...91 WHL 016 REV 12 18 14 ...
Page 92: ...92 WHL 016 REV 12 18 14 ...