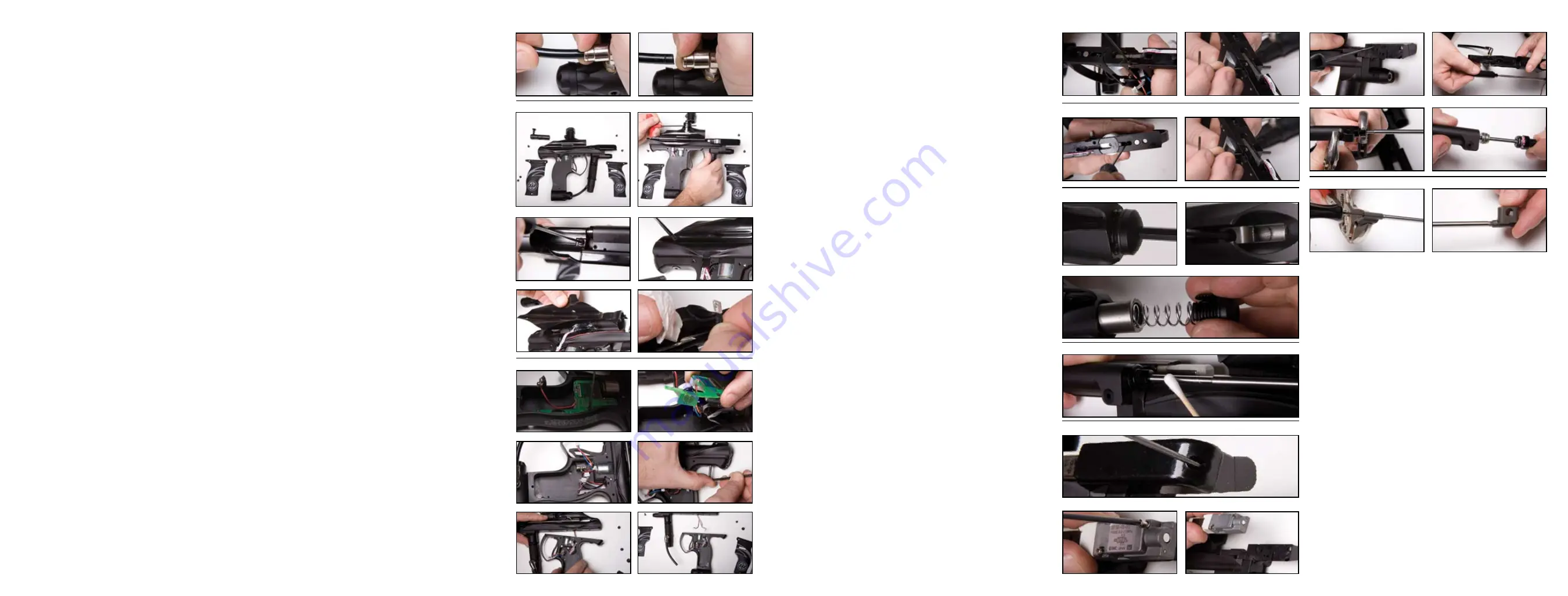
10
11
Maintenance
Your Autococker® SR Marker was thoroughly inspected and test-fired at the factory and should only require verifying the velocity adjustment with a chronograph before use. After extended use
and under varying conditions, your marker may require some adjustment.
When performing any adjustments on the marker, check for paintballs in the marker, breach and loader. Again, if you are not certain of your skills, have any adjustments performed by a qualified
technician. Any damage caused by improper adjustment is not covered under warranty.
It isn’t necessary to completely disassemble your marker to clean it. WGP recommends the following cleaning be done after each day of play. Note: Ensure all paintballs are out of the marker, air
source is removed and marker is degassed, and marker is OFF. Remove the barrel sock and then remove the barrel. Lightly spray marker down with a 50-50 mix of rubbing alcohol and water and
then wipe down. Wipe down the marker with a clean cloth, or blow off the marker with compressed air (NOT CO2). Remove bolt and lubricate bolt O-rings with petroleum jelly or lithium grease,
then reinstall. WGP recommends that after every 4-5 days of play, place 3-4 drops of 3 in 1 or other paintball marker specific oil in the air receiver and fire the marker 10-15 times without the
barrel. This will distribute the oil throughout the marker and lubricate the internals. Remove the battery and store the marker in a cool place.
Factory approved lubricants:
• Petroleum Jelly
• Lithium Grease
• 3 in 1 Oil
The ASR is made to withstand paintball shots from 10 feet away. Paint may sometimes enter the marker. If excess paint is present and can not be cleaned using a clean cloth, disassembly may be
required. Before any disassembly, confirm marker is OFF and degassed properly.
Macro Line Quick Disconnect hose (Figure 10): The ASR is equipped with a Macro Line Quick Disconnect hose. (see diagram) This hose can be easily disconnected when not under pressure (when
no cylinder is attached) Simply push the macro line ring towards the fit-ting and pull on the hose at the same time. This feature is designed for quick and easy mainte-nance and upgradeability.
Check the hose for any visible damage or cuts. If damaged, replace immediately. Reassembly is easy, press the hose all the way into the fitting. Note: If the user is not familiar with a Macro Line,
WGP does not recommend removal. Take the marker into an approved service center for maintenance.
Eye cleaning and ball detent repair: The ASR has been designed with new light weight body covers to protect the marker’s vital components from paint and debris. These covers help retain the
break beam eyes and ball detents. They protect the wires and enclose the pump rod and side cock block. If paint or debris get inside, removal and cleaning may be required. Start by removing the
left and right side grip panels (Figure 11). Remove the barrel and bolt. Use a 5/32” Allen key to loosen the bottom feed neck screw. Pull the feed neck up and off of the feed port adaptor. Use you
5/32” Allen key to remove the feed port adaptor by putting it thru the hole in the adaptor and turning it out counterclockwise (Figure 11.2). Now pull the Upper Panel Retaining Ring up and off.
Use a 5/64” Allen key to remove the front panel retaining screw (Figure 11.3). Remove the rear retaining screw. Carefully remove both left and right side panels (Figure 11.4). Clean the eyes and
examine the ball detents nubs (Figure 11.5). Use alcohol and a q-tip. Be very careful since the eyes are delicate. Reassemble the eyes into position and use the provided round tape to retain and
aid in reassembly. When reassembling, make sure wires are not kinked or in a position that they can be cut.
Frame (Figure 12): The ASR frame has been designed to be trouble free but still may require some minor maintenance. The new PCBA cover helps protect the PCBA and reduce paint contamina-
tion. It is still possible to have paint or debris get into the frame and PCBA section. To disassemble and clean, first start by removing the left and right side panels. Unplug the break beam eye and
pneumatic valve connectors from the right side of the frame (Figure 12.2). Disconnect macroline hose (see instructions above). Use a 1/8” Allen key to remove the screws (Figure 12.4). From
above, clean any debris from the sear and solenoid section.
If sear removal is required, use a 1/16” Allen key to loosen locking set screw (Figure 13). Carefully push the sear pin out form right to left (Figure 13.2). Remove the sear return spring and clean
the area with a q-tip. Clean the sear and carefully reassemble. Tighten sear set screw and lube the sear with petroleum jelly. Note: Make sure sear return spring is reassembled, if not marker will
not operate properly.
PCBA removal and cleaning: Note: This should not be done unless the user is very familiar with electronic care. Be very carefully with the PCBA, static can damage the sensitive electronics.
If excess debris is inside the PCBA area and needs cleaning, use a 1/16” Allen key to remove the 2 screws that retain the PCBA cover on the right side of the frame and remove the top screw on the
left side (Figure 12). Carefully remove the PCBA cover. Use a 5/64” Allen key to remove the PCBA screw and carefully pull the PCBA out (Figure 12.2). Carefully unplug the connectors to the rear
LED, microswitch, and solenoid (Figure 12.3). Clean area with alcohol and reassemble.
Trigger removal: Use a 1/16” Allen key to loosen the trigger set screw (Figure 14). Slide the trigger pin out and remove the trigger (Figure 14.2). Clean the trigger and trigger pin hole on the
frame. Reassemble, confirm that the pin is centered and lock the set screw down. Lubricate all moving parts with Vaseline, and reassemble.
Hammer Removal and installation: Debris and dirt can enter the lower tube and contaminate the hammer and slow down the movement. This will affect your function and velocity. The hammer
should float and move smoothly even with out the spring pushing it. To check this, remove the rear IVG and spring. Note: Confirm marker is degassed properly and always practice safe paintball
marker handling and procedures. Confirm Barrel sock is attached and secured correctly. Cock the hammer back and point the marker down. Now turn the marker on and fire the marker releasing
the hammer. If the hammer moves freely and strikes the valve, then disassembly is not required. If the movement is slow and obstructed by excess debris and dirt, you will need to remove the
hammer and clean the inside of the lower tube and hammer. Remove the bolt and use a 1/8” Allen key and loosen the lug locking screw at the rear of the hammer (Figure 15). The hammer will
be held in by the lug and will not fall out. Now point the marker up and use your 1/8” Allen key to unscrew the lug out turning it counterclockwise (Figure 15.2). Note: Keep track of how far you
turn the lug out because you will have to reset the lug when reassembling.
Once the lug moves out far enough, the hammer will be able to be removed. Slide the hammer
out of the rear (Figure 15.3). Clean the hammer and lower tube. Lightly lube the hammer with
oil or petroleum jelly. Reassemble the hammer and adjust you lug to the right position (see
Lug adjustment process).
The front block manifold of the ASR has been completely redesigned. All air passages are inter-
nally ported to increase efficiency and reduce maintenance while increasing ROF. The manifold
is gasket sealed with no hoses. The pneumatic valve has been brought closer to the ram with
almost a direct connect for air flow making the ram faster. The new MP5 ram has been design
with 2 integrated turbo relief valves (TRV’s) that vents air directly out into atmosphere. Minor
maintenance may be required.
The ram is a two-sided piston and is powered by air. The ram pushes the pump rod back and
forth cocking the marker and loading paintballs. Keeping the ram lubed is very important and
will ensure long marker life. Use some petroleum jelly and apply some to the pump rod where
the ram end cap is (Figure 16). Manually cycle the pump rod to apply lubrication onto the end
cap o-ring. This will increase the life of the o-ring decreasing chances of air leaks. Putting oil in
the ASA and cycling the marker will also internally lube the ram.
Front manifold assembly repair should be done by qualified technicians only.
Pneumatic solenoid removal and adjustment should only be done if air is leaking from the
gasket. First remove the solenoid cover on the right side by unscrewing the screw with a 1/16”
Allen key. (Figure 17) Remove cover by pulling out. With a small flat head screw driver, unscrew
2 screws (Figure 17.2) and carefully inspect bottom gasket for cuts (Figure 17.3). Clean surface
on manifold and carefully reassemble.
Ram removal and cleaning should not be done if user is unfamiliar with marker assembly.
Advanced maintenance is required here and should be done by qualified technician. Start by
first removing the pneumatic valve (see above). Remove the left side panel and bolt. Use a
1/16” Allen key and remove the 3 screws (Figure 18). Pull ram away from body (Figure 18.2).
Check ram housing gasket for cuts or tears. If damaged, replace. Clean ram housing surface
and reassemble. Reassemble and check for leaks. To remove and replace ram shaft o-ring,
remove ram housing. Unscrew ram end cap with 1/4” wrench (Figure 18.3). Pull ram end cap
with pump rod and shaft out carefully (Figure 18.4). Clean internal ram housing and shaft.
Replace the ram shaft o-ring and re-lube assembly. Carefully reassemble and use loctite on the
ram end cap when reinstalling. Allow time to dry before use.
Side Cock Block adjustment: The ASR has been factory set to the best position and WGP does
not recommend making adjustments unless the user is familiar with autococker function and
slide position. If adjustment is required, first start by removing the left side receiver panel. This
will expose the slide. First check current position, in the forward and rear position, there should
be a gap between the front and back of the slide with the receiver slide cut out area. This can
be done manually. If the slide is hitting the receiver in the front or back, you could break the
pump rod because excess impact forces will translate from the slide to the pump rod. First
loosen the slide locking set screw with a 3/32” Allen key (Figure 19). Now rotate the pump rod
to adjust the position of the slide (Figure 19.2). Check position manually by cocking the slide
all the way back and forward. Once in the right position, use “Loctite” on the pump rod, set
screw and tighten. Allow time for Loctite to dry before use.
Figure 10
Figure 11
Figure 11.2
Figure 11.3
Figure 11.4
Figure 11.5
Figure 12
Figure 12.2
Figure 12.3
Figure 12.4
Figure 12.5
Figure 12.6
Figure 13
Figure 13.2
Figure 14
Figure 14.2
Figure 15
Figure 15.2
Figure 15.3
Figure 16
Figure 17
Figure 17.2
Figure 17.3
Figure 18
Figure 18.2
Figure 18.3
Figure 18.4
Figure 19
Figure 19.2
Summary of Contents for AUTOCOCKER SR
Page 1: ......
Page 9: ...12 13 SCHEMATIC s ...
Page 10: ...14 15 ...
Page 13: ...20 WORR GAME PRODUCTS 5818 El Camino Real Carlsbad CA 92008 800 587 2246 worr com ...