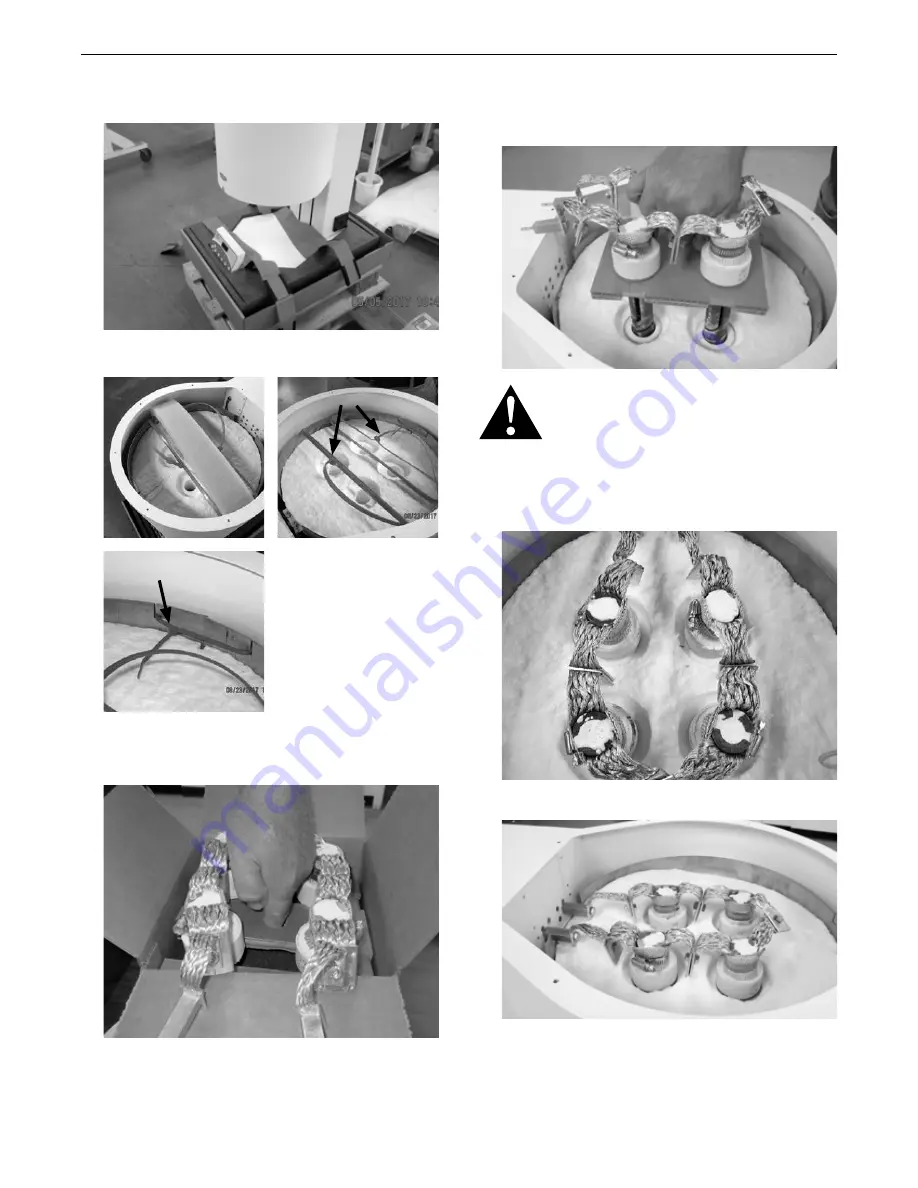
6
SinterPro
Furnace Operator’s Manual
6. Remove both the Accessory box (small) and the Heater
Element box (large) from the unit.
7. Remove foam and wire ties (both long and short).
Remove
Remove
8. Open the Heater Element box from the end as noted on
the box and remove the 4 heater rods by pulling up the
cardboard insert.
9. Lower the heater rods into the wells with the two
electrical plugs oriented towards the rear of the oven.
Carefully remove the cardboard insert from the side.
IMPORTANT! REMOVE THE CARDBOARD CARRIER BY
SLIDING IT SIDEWAYS. YOU MAY HAVE TO GRASP THE
BRAIDED STRAPS AND MOMENTARILY RAISE TWO OF
THE HEATER RODS A COUPLE INCHES TO WITHDRAW
THE CARDBOARD. DO NOT APPLY POWER UNTIL THE
CARDBOARD IS REMOVED!
10. Heating rod insertion after removing the cardboard
insert.
11. Insert the two plugs into the receptacles.