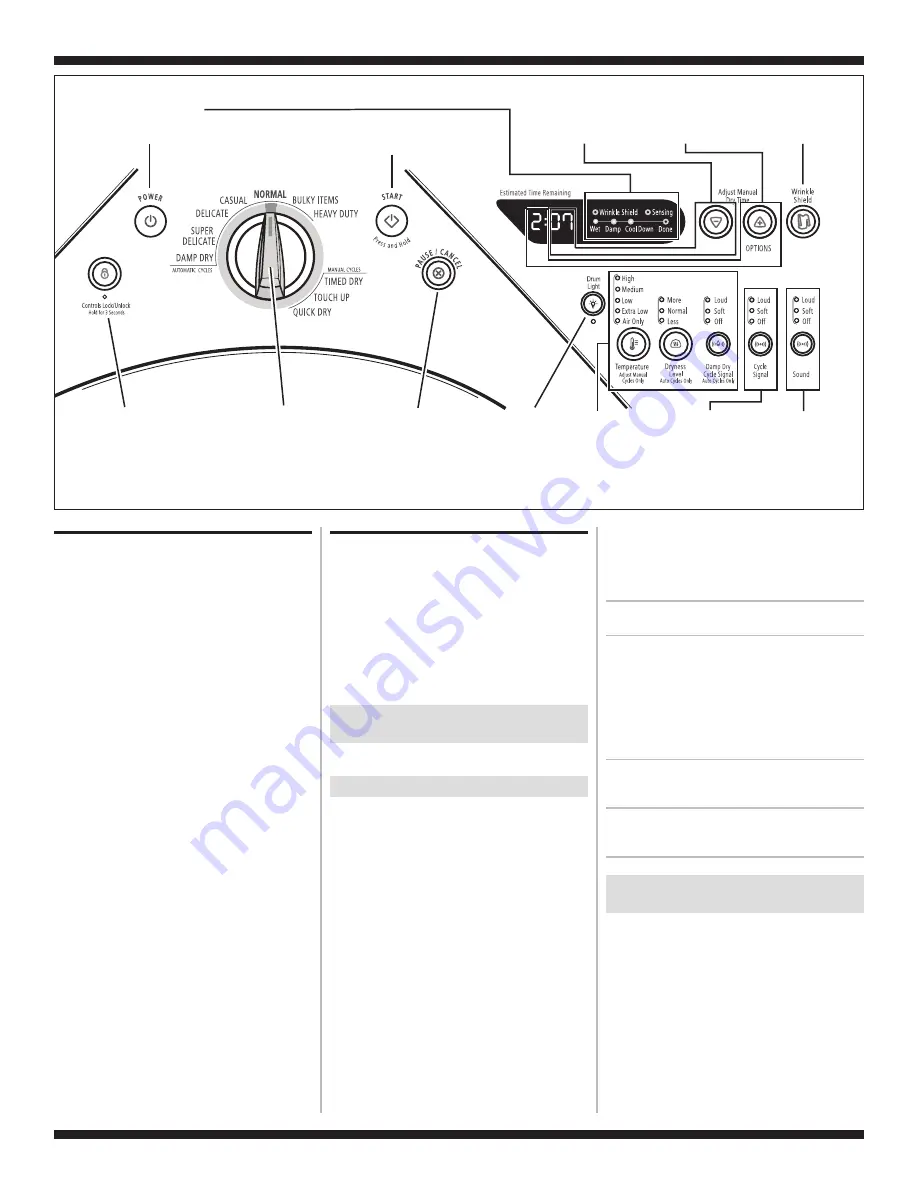
FOR SERVICE TECHNICIAN’S USE ONLY
PART NO. W10177459A
TECH SHEET - DO NOT DISCARD
PAGE 2
Button
Rotating this Cycle
Selector turns cycle
LEDs on or off.
Start button controls its own indicator,
starts dryer and displays version information.
Power button controls
its own indicator and
Cycle Status LEDs.
Controls Lock/Unlock button
controls LED below button.
Turns off all
LEDs and exits
diagnostics.
Drum Light button
controls LED
below button.
“Less Time” button
turns the middle and
right digit of the
display on or off.
“More Time” button
turns the left digit
and colon of the
display on or off.
Wrinkle Shield button
controls its own indicator
and starts Inlet
Air Flow Diagnostic.
Button Sound button
controls all LEDs
above button
(Green-Amber-Off).
Cycle Signal button
controls all LEDs
above button
(Green-Amber-Off)
and starts displaying
Line Voltage Diagnostic.
Each button
controls all LEDs
above button
(Green-Amber-Off).
Figure 1.
Console Diagnostics.
DIAGNOSTIC: Displaying Inlet Air Flow
(Electric Models Only)
Used to display the air flow value at the inlet of the
heater box being measured by the machine
control.
After entering the Diagnostic Test Mode, waiting
for the 5 second delay, and cycling through any
saved fault codes, press the Wrinkle Shield button
to activate air flow detection. A 30 or 50 second
countdown timer will start and the dryer will
turn on.
➔
If the dryer is cold, the countdown will start at
50 seconds.
NOTE:
If the dryer is extremely cold (less than
40°F [4.4°C]) the air flow may not be detected
properly, and “--” will be displayed.
➔
If the dryer is hot, the countdown timer will
start at 30 seconds (cool down period)
followed by an additional 50 second
countdown.
A Dryness Level modifier LED will also be
illuminated to indicate the air flow range
corresponding to the number displayed.
■
The More LED will be illuminated for air flow
readings above 40 cfm.
■
The Normal LED will be illuminated for air flow
readings between 29 and 40 cfm.
■
The Less LED will be illuminated for air flow
readings less than 29 cfm.
➔
If air flow value is low (Less LED is lit),
check to make sure the lint screen is clean,
the door seal is in place and the vent is not
obstructed.
DIAGNOSTIC: Displaying Line Voltage
Used to display the line voltage currently being
measured by the machine control:
After entering the Diagnostic Test Mode, waiting
for the 5 second delay, and cycling through any
saved fault codes, press the Cycle Signal button.
The voltage value will be displayed.
➔
If the line voltage is not seen on L2, the display
will flash
L2
. Go to TEST #1, page 4.
DEACTIVATING THE DIAGNOSTIC
TEST MODE
Press the Pause/Cancel button to exit diagnostics.
ACTIVATING THE MANUAL LOAD TEST
1.
Be sure the dryer is in standby mode (plugged
in with all indicators off, or with only the Done
indicator on).
2.
Select any one button (except Pause/Cancel
and Controls Lock/Unlock) and follow the steps
below, using the same button (remember the
button):
a.
Press/hold 2 seconds
b.
Release for 2 seconds
c.
Press/hold 2 seconds
d.
Release for 2 seconds
e.
Press/hold 2 seconds
f.
Release for 2 seconds
g.
Press/hold 2 seconds
The motor starts right away, the “Sensing”
Status LED comes on, and “0” (zero) is
displayed (this step starts the Manual Load
sequence):
1.
Motor turns
on.
➔
“Sensing” Status
LED turns on.
➔
0:00 is
displayed.
Now press any key (except Pause/Cancel and
Controls Lock/Unlock) and the control will
advance through each step of the following
sequence:
2. Motor + heater.
➔
“Damp”
Status LED
turns on.
➔
0:02 is
displayed.
3.
Motor + heater
+ drum light.
➔
“Cool Down”
Status LED
turns on.
➔
0:03 is
displayed.
4.
All loads turn
off.
➔
“Done”
Status LED
turns on.
➔
0:04 is
displayed.
DEACTIVATING THE MANUAL
LOAD TEST
Press the Pause/Cancel button to exit this mode.