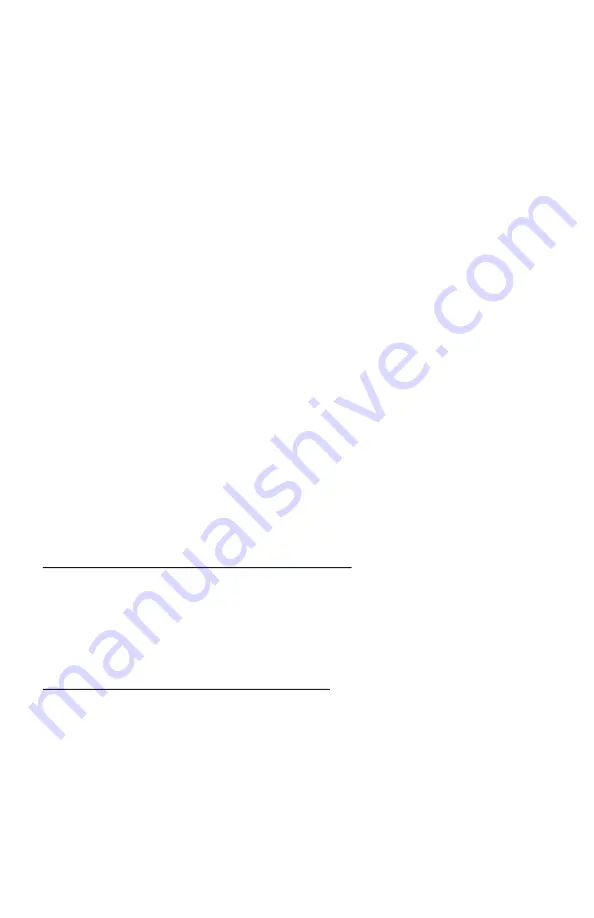
your dealer or mechanic if you don’t have the proper tools to cut the steerer tube.
6.
The star fangled nut must now be installed into the steerer tube. If you don’t
have the set tool we recommend dealer installation of this part.
(See Figure #3)
7.
Clean and grease all headset bearings and races to prepare them for assembly.
Note:
Replace the bearings if there is any sign of wear or corrosion.
8.
Now loosely assemble the headset, stem and handle bars as done in step four.
(See Figure #2)
9.
Install the headset top cap into the star fangled nut. Tighten until there is no play
in the steering. The fork should rotate freely in the head tube. Straighten the stem
in relation to the front tire and tighten the pinch bolts on the stem. Tighten the
pinch bolts on the upper clamp and double check that the lower clamp bolts are
tight. These can easily be over tightened. We recommend tightening to 8 foot
pounds. If there are any questions consult your dealer or mechanic.
10.
Slide the wheel in and line up the brake rotor with the brake caliper then line up
the hub with the axle feet. Slide the 20mm axle through the right side foot, hub and
into the left side foot. Tighten the pinch clamps after the axle is properly seated and
tight.
11.
Adjust your front brake according to the manufacture’s instructions.
12.
Check to see that the brakes are adjusted and properly working. Make sure the
brake line doesn’t interfere with any part of the bike when the fork is compressed
and released.
Warning:
When installing the wheel or a new tire, check for minimum
clearance. Measure from the highest point on the tire to the under side of the
crown. There must be 1/8” or 3mm more clearance than the fork’s travel to
ensure adequate clearance in all riding conditions. Any less clearance can cause
the tire to hit the crown resulting in serious injury or death.
The Groove 200 will not work on frames with head tubes longer than 5-1/2”.
To get the most from your White Brothers fork, it is important
that you tune the fork to fit your style of riding and the conditions you ride in.
INITIAL BREAK-IN PERIOD
Your new fork is designed to break-in over a period of 10 hours or more of riding.
As all the parts bed into each other, the stiction (friction) of the fork will diminish
and the fork will absorb the bumps better. After this initial break-in, fine tuning the
air spring and hydraulic damper may be beneficial to achieve the best possible fork
performance for your weight and riding style.
TUNING YOUR SPRINGS
1.
There are two ways to adjust your forks spring action. The first is by changing
the air pressure and the second is changing the springs for a completely different
rate. Your White Brothers fork comes equipped with a medium rate spring
adjusted with zero air pressure for minimum pre-load.
2.
The medium rate springs that are fitted in your White Brothers forks should
satisfy most rider weights and conditions. If you are a
lightweight rider
and feel
you are not getting the full travel out of your fork, see “Disassembly of the Spring
Leg”.
Remove the o-ring on the double sided spring guide
. This will increase
the air volume size and decrease the ramping of the fork. A good way to test the
travel you are using with your fork is to tie a zip tie around fork stanchion and
slide it up to the bottom of the wiper seal. Go and ride a variety of conditions you
normally experience, including some conditions that you feel should use the full
fork travel. After the ride, inspect the position of the zip tie. Measure that position
from the fork wiper seal to the axle clamp. Next remove the fork cap and
compress the fork to full bottom out. If the zip tie moves more than 1/4”, your
spring rate is probably too stiff and a change to less pre-load may improve your
ride. Very heavy riders may note that the zip tie slides down the fork stanchion
quite far even over minor bumps and this could indicate the need for more pre-
load.
3.
Pre-load
is changed by adding or removing air from spring leg. More air pressure
will have less sag and a firmer feel. Less air pressure will have more sag and a
softer feel. The fork is designed to use zero pressure and should never exceed 40
lbs.
TUNING YOUR DAMPER
1. Rebound damping
is adjusted by turning the slotted brass adjuster on the top cap
of the right leg. The adjuster has 8 turns of adjustment. Turn the adjuster clockwise
for slower rebound. To speed up rebound, turn the adjuster counter-clockwise. Start
with a middle setting and fine tune the rebound from there. Proper rebound will
allow the tire to track the ground over consecutive bumps. Rebound that is set too
slow will pack-up (feel harsh over consecutive bumps) while rebound set too fast
will cause the fork to top out harshly. If the fork is topping out and you have the
correct spring for your weight, turn the adjuster one turn at a time until the top-out
stops.
2. Compression damping
can be changed two ways: (1) by adjusting the
compression damping screw on the back of the canister on the bottom of the right
fork leg. Threading it in slows compression and threading it out speeds up
compression; and (2) by adding or removing air pressure (or nitrogen)from the
canister at the bottom of the right leg. Pop off the dust cap and adjust between 50
psi min. and 175 psi. max.
WARNING: Exceeding the maximum recommended
damper pressure can result in catastrophic rupture of the reservoir canister,
causing serious injury or death.
Adding air will increase the compression
damping (slow it down) and removing air will decrease compression damping
(faster compression). Less compression damping will increase the fork dive but
will feel smoother over small bumps. More compression damping will feel stiff
over small bumps but will be more resistant to bottoming. Never run less than 50
psi in the canister.
Your White Brothers fork requires periodic maintenance to ensure peak performance
and long life. Neglecting proper maintenance will reduce the fork’s life. Internal
build up of water and dirt or a lack of lubrication will cause excessive wear and
void the warranty.
BEFORE EVERY RIDE:
Visually inspect your fork for bent or broken parts, loss
of oil, abnormal sounds or other indications of possible fork failure. Compress you
fork to verify proper function. Check all other bicycle components to ensure proper
working order.
Page 4
Page5