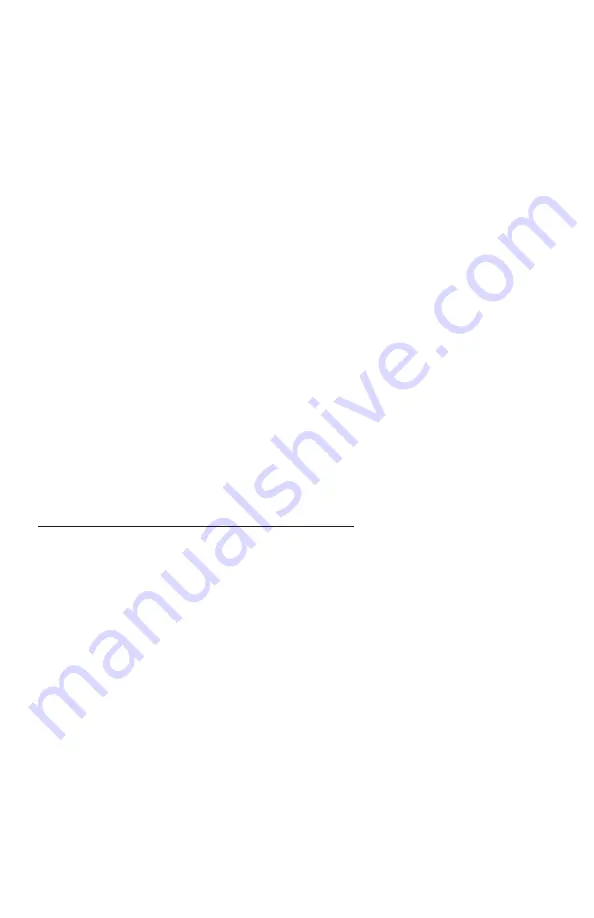
AFTER EVERY RIDE:
Clean and dry the exterior of your fork. When cleaning the
fork, do not direct the water spray at the seals. Visually inspect your fork for damage.
*EVERY 30 HOURS OF RIDING:
Your fork should be disassembled, inspect,
cleaned and re-grease. If the fork appears to be relatively clean, you can go 40 hours
between servicing. If the fork appears excessively dirty you should service it every
20 hours. The three things that will effect the service interval and performance of
your fork are water, mud and dust. How much you use your fork in those conditions
will determine how much service it requires.
*EVERY 100 HOURS OF RIDING:
Complete service should include removing
the upper fork legs cleaning and re-greasing all shafts, bushings and seals. Check
damper leg for proper function(see Disassembly of the Damper Leg). NOTE:
Disassembly of the hydraulic damper should be left for the White Brothers factory.
WARNING: Improper servicing of the damper leg can result in hydraulic lock
and catastrophic failure of pressurized parts, causing serious injury or death.
Servicing of the damper must be referred to the White Brothers factory or a
factory -authorized service center.
Tools needed for service
Quantity Part Number Description
1
WB-97-700 Clamp block
1
SH-EDL-04 Suspension Lube
1 9 mm. Open End wrench
1 25 mm. Socket
1 3mm. Allen Wrench
1 25 mm. Open End Wrench
*White Brothers recommends that you consult a tech before performing the
following:
BASIC FORK DISASSEMBLY
Removal of the Leg Assemblies
1.
Disconnect the front brake and loosen the pinch clamp bolts at the bottom of each
leg. Un-thread the axle with a 17mm wrench and remove the wheel.
2.
Loosen the four M6 upper clamp bolts. Before loosening the lower clamp bolts,
start to loosen the top caps using a 25mm socket. Then loosen the lower clamp
bolts and slide the legs out of the clamps.
Disassembly of the Spring Leg Assembly (Left Hand)
1.
Unscrew the top cap from the outer leg. Check for noticeable play between the
stanchion tube and the outer fork tube. If there is play, contact White Brothers or a
qualified dealer for service.
2.
Lower the outer leg until the seal touches the drop out. Place in vise with soft
jaws.
3. Remove air from cap.
Use a 25mm socket to loosen the rod from the air cap.
Hold the shaft on the flats with a 9mm open end wrench and unscrew the air cap
from the shaft.
4.
Remove the inner leg from the outer leg. Remove the stanchion plug using a
25mm wrench or socket.
5.
Remove from vise.
Remove the fork guard from the dropout. There is a set screw
positioned between two of the fork guard screw holes that should be removed at
this time. Turn the open end of the stantion down to your work bench top Use
compressed air to remove the springs by directing air into the hole to push the
springs and spring separator seal out the top of the leg.
6.
Clean and inspect all the parts. Check the DU bushings inside the outer leg
carefully for wear. This is done by looking at the color of the clean bushings. If the
bushings are dark gray, they are in good condition. If they are bronze/gold in areas,
they are worn and can cause fork stanchion damage. Please note that special tools
are required to remove and replace these bushings. This service can be performed
directly through White Brothers or a qualified dealer.
7.
Next, inspect the fork stanchion tubes for wear, nicks or scrapes. These will cause
premature wear on the seals and DU bushings. If there is any damage to the
stanchion tubes, have them replaced.
8.
Inspect the o-rings for damage. There is a o-ring on each end of the control rod and
on both spring guides. If there’s any question about them sealing, replace the o-
rings.
Disassembly of the Damper Leg Assembly (Right Hand)
NOTE:
Service of the damper is best performed by the WB factory. Contact White Brothers
for the details.
1.
Unscrew the top cap from the outer leg. Check for noticeable play between the
stanchion tube and the outer fork tube. If there is play, contact White Brothers or a
qualified dealer for service. Slide the outer leg down to the axle clamp.
2.
Unscrew the top cap counterclockwise from the shaft by holding the flats on the
shaft with an open end wrench.
Note there is a small spacer under the cap that can
fall out.
3.
Remove plastic washer, bumper and spring, then pull the inner leg out of the outer
leg.
BASIC FORK REASSEMBLY
Rebuilding the Outer Legs
1.
Throughly clean all the parts.
2.
Check the condition of the wiper seals and the inner oil seal for cracks, abrasions
or obvious signs of wear.
Note: If the wiper seals are in question, replacement is
always recommended.
It helps to keep the dirt out, especially when riding in harsh
conditions.
3.
The wiper seals can be removed with a spoon style tire iron or something similar
and can be re-installed using a large socket as a driver to install squarely in to the
leg.
Note: Jamming the seals in at an angle can crush the steel casing and the seal
will no longer seal correctly and/or stay in place.
4.
Apply grease to the DU bushings down inside the leg. Verify the bushings are in
good working order. Bushings are replaceable but require a number of special
tools to remove and install. Return to White Brothers to have the bushings changed
if required.
Rebuilding the Spring Leg Subassembly
1.
Throughly clean all the parts.
2.
Check the condition of the o-rings and replace if necessary.
Page 6
Page 7