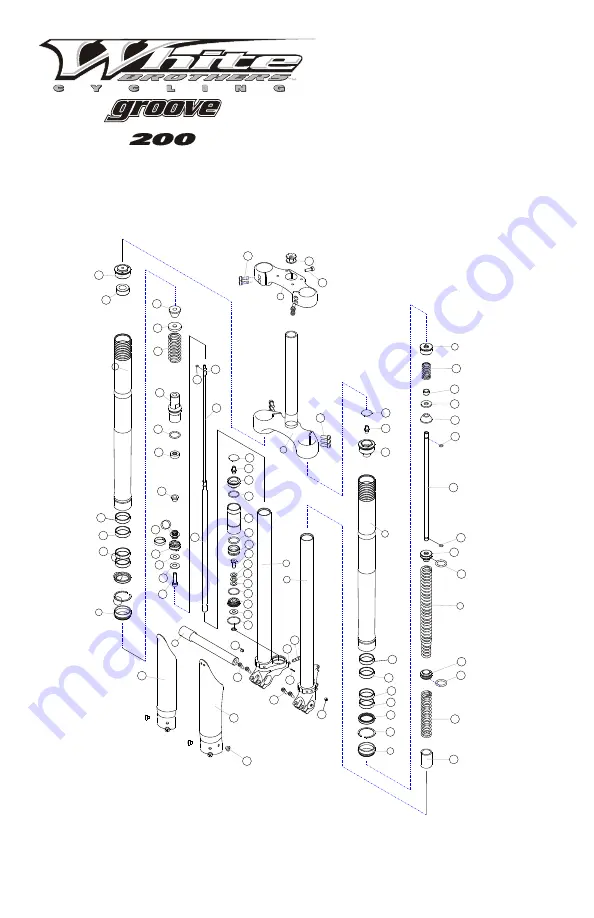
3.
Install the parts as shown in the exploded view, using heavy grease on all internal
parts. Thread the assembly into the inner leg. Use a 25 mm socket to get the
stanchion plug started, being carful not to cross thread it into the stanchion.
Rebuilding the Damper Leg Assembly
1.
Throughly clean all the parts.
2.
Inspect for obvious signs of damage. Pressurize the damper canister to at least 50
psi. Test the damper by pushing the shaft down. It should compress and return in a
controlled manner. Screw the compression adjuster in to insure the damper slows
when adjusted. At the top of the stroke, if the damper shaft does not return to 8”
above the seal head this indicates the need for damper service. Reinstall the
greased spring Reinstall the washer and bumper after the outer leg is installed.
Reinstalling the Outer Legs
1.
Apply Slick Honey or other non-lithium based suspension lube to the DU bushings
inside the outer leg. Make sure to lube the lower DU bushing which is deep in the
outer leg.
2.
With all parts cleaned and reinstalled with new grease, fit the outer leg over the
stanchion tube and gently rock and slide the legs until the inner leg slides into the
bushings. Slide the outer leg all the way down to the drop out. Check for
noticeable play between the stanchion tubes and the fork lower. If there is play,
contact White Brothers for service.
Reinstalling the Springs and LH Top Cap
1.
A 10mm wrench will hold the flats on the shaft as you thread the top cap down
until it stops. Hold the top cap with a 25 mm socket and tighten.
2.
Thread the top cap into the outer leg and tighten.
Note: A little more than hand
tight is all that is necessary, as the upper clamp will hold the top caps tight.
Reinstalling the RH Top Cap
1.
Screw the rebound needle in clockwise until it stops then back it out 3 to 4 turns.
2.
Install the small spacer under the top cap if you removed it earlier.
3.
On the damper shaft, install the chrome bottom out spring onto the seal head,
spring spacer and then the yellow bumper with heavy grease on all parts. The parts
will be seated the first time the fork bottoms out.
4.
Install the top cap onto the damper shaft and tighten. Remove the assembly from
the vise and thread the top cap into the outer leg and tighten.
Note: A little more
than hand tight is all that is necessary, as the upper clamp will hold the top caps
tight.
7.
Readjust the rebound needle to your preferred position.
The following is an illustration
and parts table which gives
you the exploded view of your
White Brothers fork. The parts
table indicates the part
Page 8
Page 9
22
45
28
29
30
31
32
34
35
36
33
26
27
27
11
23
24
25
21
1
58
58
58
57
56
8
7
50
51
52
54
3
55
54
49
20
10
1
54
2
49
20
48
38
46
43
43
43
41
62
53
53
37
42
44
45
47
9
15
60
18
17
61
14
61
19
16
4
13
19
12
59
58
58
58
57
56
8
65
65
64
58
58
40
5
6
64
63