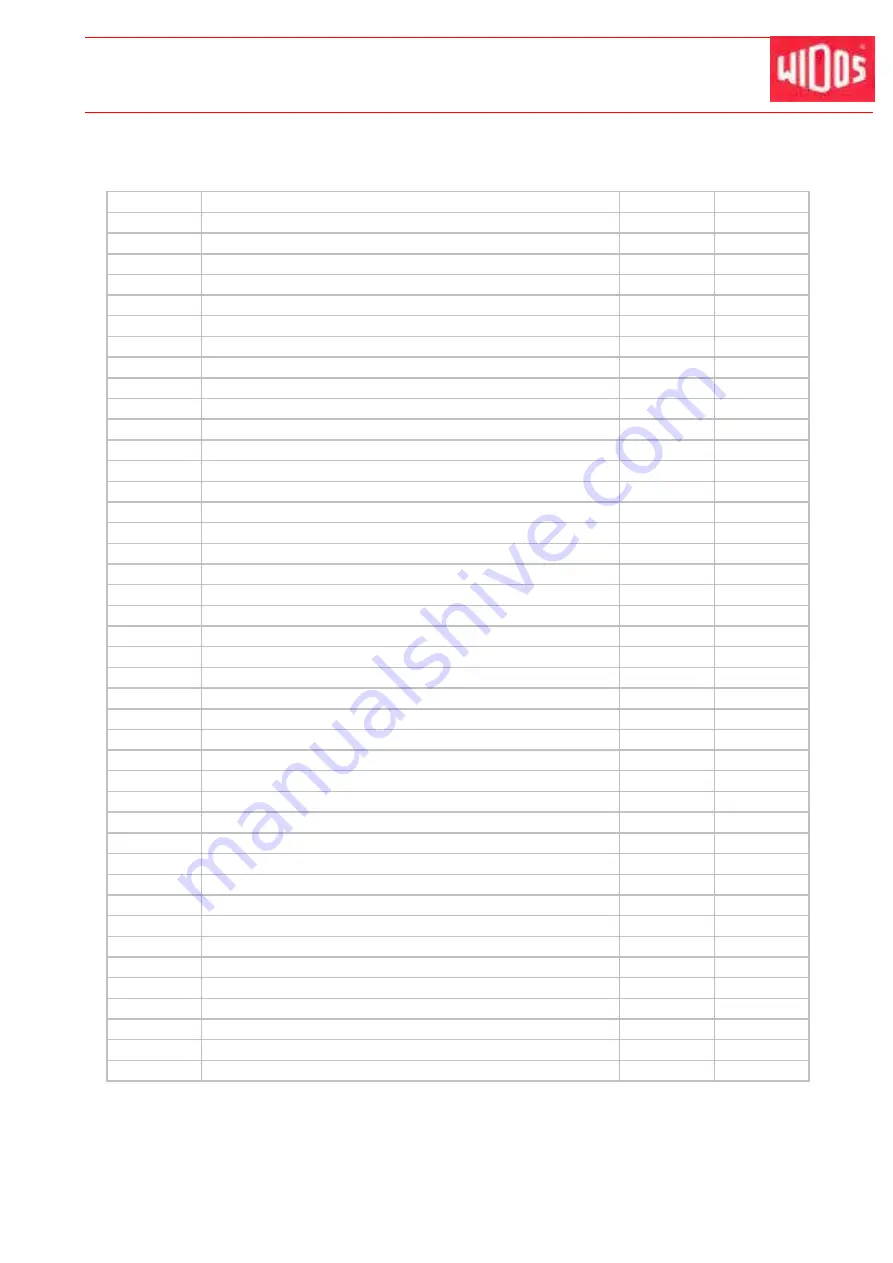
Kunststoffschweißtechnik
Spare parts list
Chapter 10
Basic machine
WIDOS 4900 CNC 3.5
Pos.
Name
Piece
Art.-No.
1
Outer clamp, fixed
1
216101
2
Inner clamp, fixed
1
216102
3
Inner clamp, movable
1
216103
4
Outer clamp, movable
1
216104
5
Upper clamp
4
214105
6
Thread insert M 6
8
GEW-M6
7
Threaded rod
8
091108
8
Nut
8
091109
9
Pressure disc M 14 DIN 6340
8
6340N
10
Rivet
8
216111
11
Lock washer Gr. 7 DIN 6799
8
6799G
12
Hydraulic cylinder
2
216106
13
Guide bearing
4
LKH3050
Gasket set for cylinder
2 set
D091106
14
Flat head screw M 12x20 DIN 7991
8
7991L020
15
Pull shaft
2
216107
16
Hexagon nut M 8 DIN 934
2
0934H
17
Disc M 8 DIN 125
2
0125H
18
Grub screw M 8x10 DIN 916
4
0916H010
19
Shaft
3
091131
20
Flat head screw M 12x30 DIN 7991
6
7991L030
21
Base frame
1
216118
22
Base plate for base frame
1
2161182
23
Pan-head screw M 8x30 DIN 912
2
0912H030
24
Support
1
216141
25
Hydraulic tube
2
VSCHL61
26
Quick coupling spigot
1
VST14
27
Quick coupling socket
1
VMU14
28
Screwed connection GE 8 LR 3/8"
2
VXGE8L38
29
Compressing collar
4
VP256
30
Threaded nippel 1/4"
2
VN856
31
Elbow nippel
2
VB386
32
Protection hose (3 m)
1
EA0801
33
Support for filter
2
092120
34
Disk M 8 DIN 125
2
0125H
35
Hexagon screw M 8x20 DIN 933
2
0933H020
36
Copper ring 5x9x1 DIN 7603
4
7603E
37
Pan-head screw M 5x6 DIN 912
4
0912G006
38
Tear off bar for heating element
1
216503
39
Washer M 8 DIN 6340
2
6340H
40
Hexagon-head screw M 8x12 DIN 933
2
0933H012
22.11.2005
Working instructions WIDOS 4900 CNC 3.0
Page 69 / 1 of 76