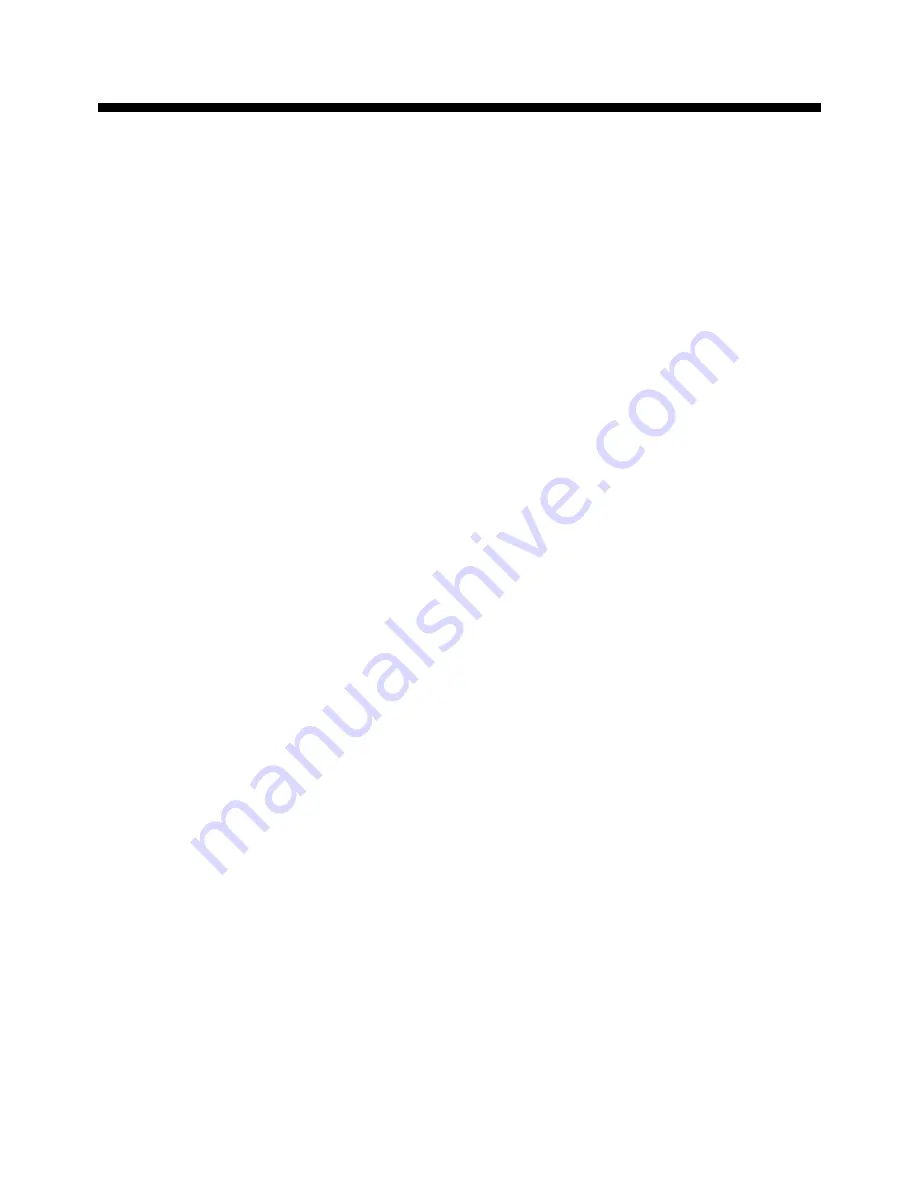
WILKERSON
OPERATIONS
Page 3
The Air Compressor 1
Although there are many types of compressors, all have
some type of inlet filtration. If this filtration is not maintained
or is not properly designed for ambient conditions (ie. large
amounts of coal dust, road dust, fly ash, etc.) the result will
be increased compressor maintenance and an additional
contamination load on downstream equipment.
Shut-Off Valve 2, 11, 14
Sized in accordance with air flow capacities, to provide the
minimum pressure drop.
Flexible Connections 3, 5, 10, 13
Flexible piping between a compressed air system and the air
dryer or aftercooler is recommended to eliminate any
possible vibration induced damage.
The Aftercooler 4
As the name implies, the aftercooler cools the hot air after
compression. This not only reduces the temperature of the
air to within acceptable values for downstream equipment,
but also condenses out a very large amount of water. This is
very important because for approximately every 20°F (11°C)
reduction in compressed air temperature, one half of the
water is condensed. A separator must be used to actually
remove the water from the system.
The Separator 6
The separator removes the large droplets of oil and water
from the compressed air stream which condense in the
aftercooler, subsequently improving the dryer capacity.
Though one of the least expensive components of the
compressed air system, the separator is one of the most
critical. A difference of only a few percent efficiency in a
separator can allow substantial amounts of additional water
to pass downstream, both overloading a dryer and causing
potential maintenance problems. A properly sized electronic
drain should be installed to drain away accumulated liquids.
Storage Tank 7
This acts as a storage vessel which will also remove liquids.
Therefore, an electric drain valve should be installed. (Note:
Where possible the receiver should be installed with the
inlet near the bottom and the outlet near the top.)
Prefiltration 8
Wilkerson refrigerated air dryers will operate efficiently and
reliably without filtration. But if your system also requires dirt
and oil free air, then appropriate particulate or coalescing
filtration is required.
Electric Drains 9
Proper drainage of accumulated liquids is essential to proper
system operation. Should liquids be allowed to build up in
receivers and filters, liquid “slugging” can occur causing loss
of performance to downstream components.
Automatic electric drain valves provided on the dryers
automatically drain liquid water from the dryer evaporator and
separator. They feature full adjustment of drain cycles from 1
to 45 minutes, and valve opening durations from 1 to 15
seconds. Two indicator lights for indicating “power on” and
“valve open” status allow for easy visual inspection. Electric
drains are also recommended for all other drain points in the
compressed air system including separators, filters,
receivers, and drip legs.
By-pass Valve System 12
It is strongly recommended that a by-pass valve system be
utilized to provide for convenient maintenance and service.
Applications which require a continuous supply of dry air
should consider installing two dryer systems. This will assure
a steady supply of dry air under any conditions.
Afterfiltration 15
For critical applications, to obtain a maximum downstream oil
content of .01 ppm/wt and .003 ppm/wt respectively. See the
chart below for recommended afterfilters.
The Refrigerated Air Dryer 16
The Wilkerson Refrigerated Air Dryer is the result of
unprecedented research and testing. It is subjected to
simulated no load, partial load and full load performance
examinations to meet our quality standards. As such, it will
provide years of reliable service if properly installed and
operated within its design specifications. The dryer should be
installed in a well ventilated area.
Components Of A Refrigerated Dryer Compressed Air System
Recommended Filtration
Recommended Coalescing Prefilters/Afterfilters
Dryer
Dryer/Filter
Model
Pipe
Type A
Type B1
Type C
Number
Size
5.0 Micron
1.0 Micron
(.01 ppm downstream
Inlet/Outlet
Particulate
Coalescing
remaining oil content)
WR( )-0250
2" NPT
F35-0
C
-
0
00
M35-0C-S00
M35-0
C
-000
WR( )-0300
2" NPT
F35-0
C
-
0
00
M35-0C-S00
M35-0
C
-000
WR( )-0400
2" NPT
F35-0
C
-000
M36-0C-S00
M36-0
C
-000
WR( )-0500
2" NPT
F35-0
C
-000
M36-0C-S00
M36-0
C
-000
NOTE: Recommended filters were selected on the basis of flow capacity—not pipe size.