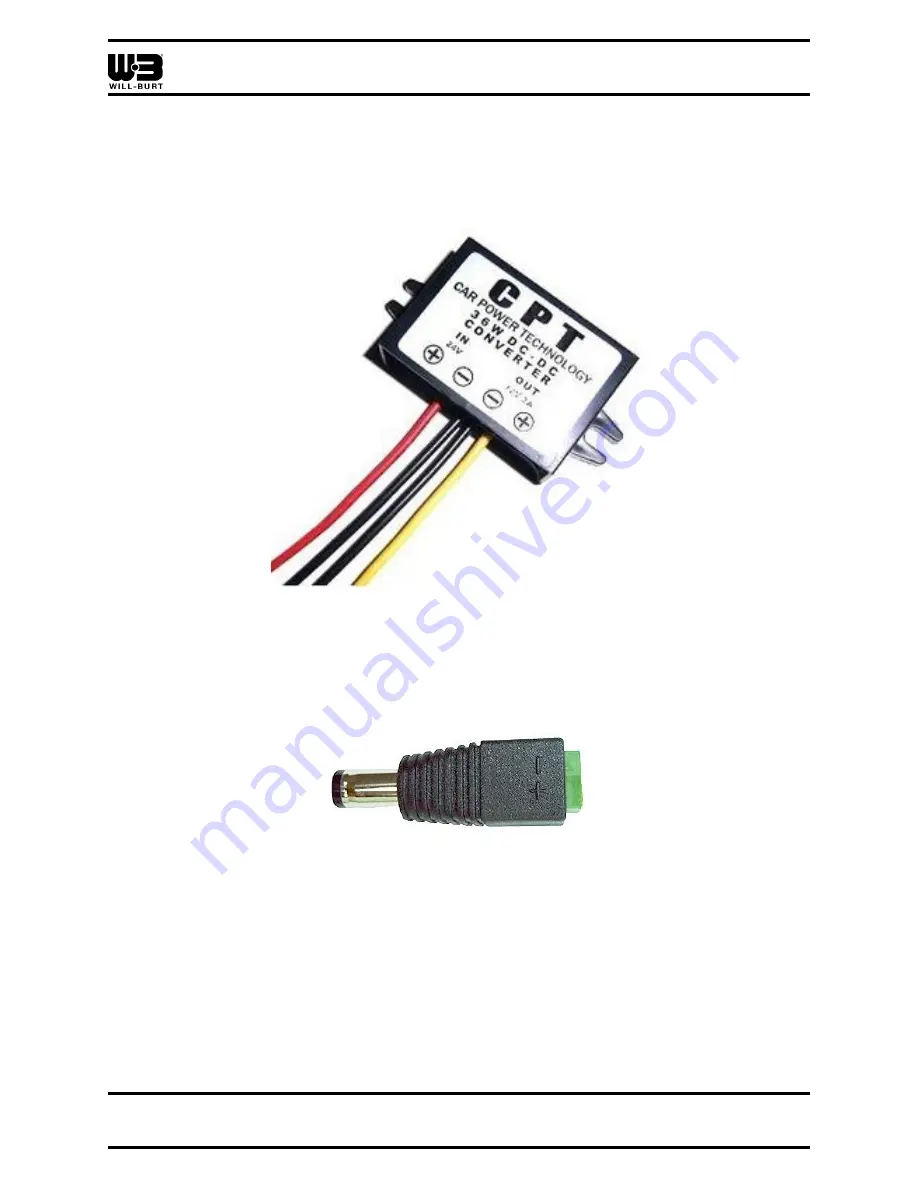
P
OSITION
I
T
PI-150
AND
PI-75
TP-5129001-J
1-9
January 2022
1.6.6 Step Down Converter
The step down converter (P/N: 208017) (Figure 1-8) is used in systems with 24 VDC input
power to step down the power to 12 VDC to power the default joystick controller if the AC power
supply supplied with the joystick is not used to provide power.
Figure 1-8 Step Down Converter
1.6.7 Barrel Connector (2.1 mm)
The 2.1 mm barrel connector (P/N: 5195601) (Figure 1-9) can be used to connect the controller
to the step down converter or 12 VDC power source.
Figure 1-9 Barrel Connector
Summary of Contents for 5061001
Page 2: ......
Page 8: ...POSITIONIT PI 150 AND PI 75 vi TP 5129001 J January 2022 ...
Page 34: ...POSITIONIT PI 150 AND PI 75 2 14 TP 5129001 J January 2022 ...
Page 44: ...POSITIONIT PI 150 AND PI 75 4 2 TP 5129001 J January 2022 ...
Page 50: ...POSITIONIT PI 150 AND PI 75 5 6 TP 5129001 J January 2022 ...
Page 56: ...POSITIONIT PI 150 AND PI 75 7 2 TP 5129001 J January 2022 ...
Page 57: ...POSITIONIT PI 150 AND PI 75 TP 5129001 J 7 1 January 2022 ...
Page 59: ...POSITIONIT PI 150 AND PI 75 TP 5129001 J 7 3 January 2022 ...
Page 61: ...POSITIONIT PI 150 AND PI 75 TP 5129001 J 7 5 January 2022 ...
Page 63: ...POSITIONIT PI 150 AND PI 75 TP 5129001 J 7 7 January 2022 ...
Page 65: ...POSITIONIT PI 150 AND PI 75 TP 5129001 J 7 9 January 2022 ...
Page 67: ...POSITIONIT PI 150 AND PI 75 TP 5129001 J 7 11 January 2022 ...