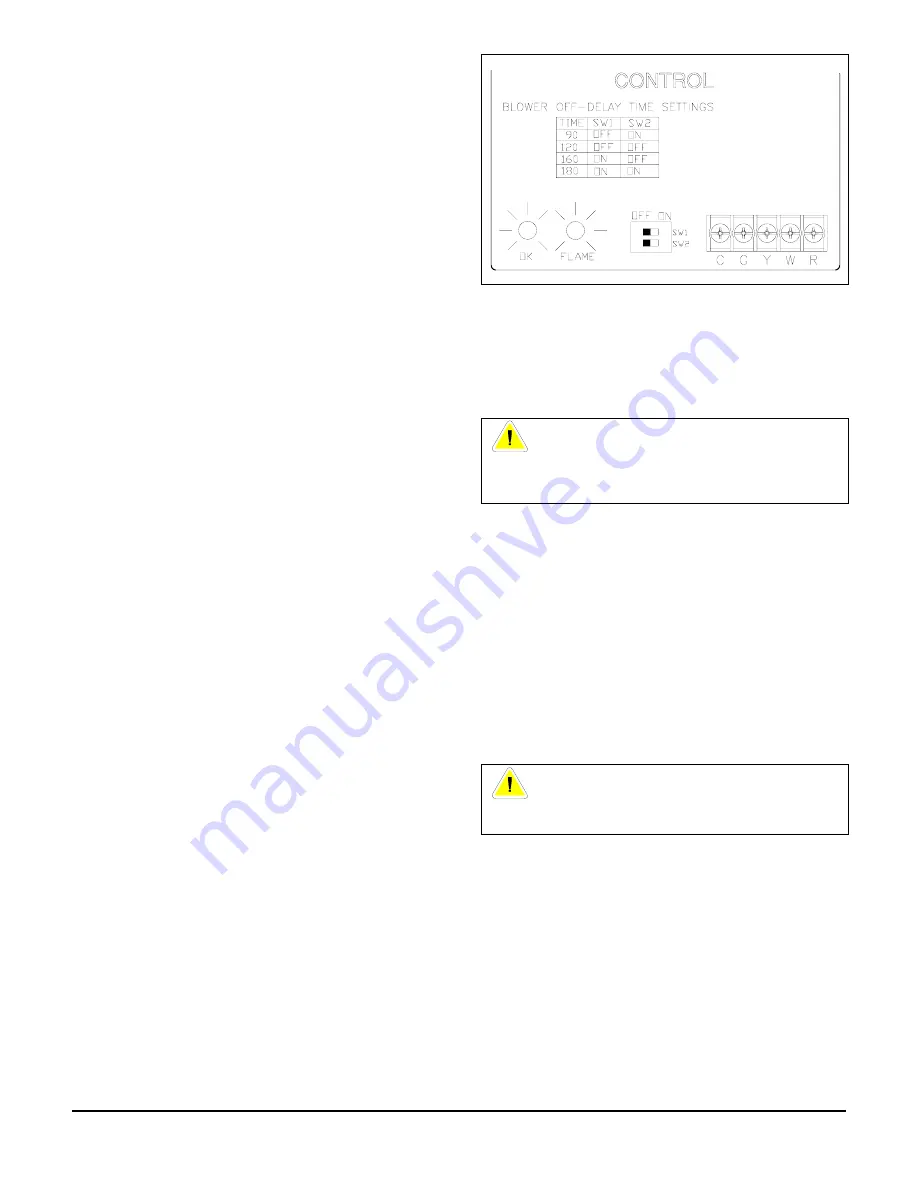
Installer’s Information Manual
Page 29
7. Diagnostic light labeled “FLAME” on Control should be
off.
8. Draft inducer should run and igniter should spark.
Manifold pressure should remain at zero.
9. Turn off electricity at electrical disconnect switch
located next to furnace. Turn gas control switch to
“ON” position.
10. Turn on electricity at electrical disconnect switch
located next to furnace. Draft inducer should run,
igniter should spark and ignite main burners. It may
take several minutes to purge the gas line before the
main burners ignite. Wait 30 seconds after main
burner ignition for main blower to start.
11. Cycle electrical disconnect switch next to furnace on
and off. Watch at least three ignition cycles. Igniter
should ignite main burners smoothly.
12. Burner flames should look the same with circulation
blower on and off.
13. Turn gas control switch to “OFF” position.
14. Remove manometer from gas control and replace
outlet pressure tap. Turn gas control switch to “ON”
position.
15. Use a commercial soap solution made to detect leaks
and check all gas piping connections. Bubbles indicate
gas leakage. Seal all leaks before proceeding.
16. Set room thermostat to desired setting.
SECTION 25. SETTING BLOWER
TIMINGS
Heating blower on-delay is fixed at 30 seconds from when
the main valve opens. It is not adjustable.
Heating blower off-delay is adjustable to one of four times:
90, 120, 160 or 180 seconds. Heating blower off-delay is
factory set at 120 seconds. If a different blower off-delay is
desired:
1. Find two small switches located near the 24-volt
terminal strip on Control.
2. Determine switch settings for desired heating blower
off-delay. See Figure 32.
3. Set switches on Control using a small screwdriver.
NOTE: Cooling blower off-delay is fixed at 90 seconds and
is not adjustable.
Figure 32. Heating Blower Off-Delay.
SECTION 26. MAINTAINING
FURNACE IN GOOD WORKING
ORDER
WARNING
: Use replacement parts listed in parts
list only. Use of incorrect parts on this furnace could cause
improper furnace operation, resulting in damage, injury or
death.
Inspection and cleaning by a qualified service person
should be performed once before each heating season
begins and once during heating season. Make sure the
inspection includes each of the items listed below.
Before inspecting furnace:
1. Turn room thermostat to its lowest or off setting.
2. Turn off equipment shut-off valve.
3. Wait at least five minutes for furnace to cool if it was
recently operating.
4. Turn off furnace electrical power.
WARNING
: Failure to disconnect electrical power
before servicing furnace could result in electrical shock or
death.
Inspect the following:
•
An operational check of the entire system. Assure that
the furnace is operating properly and safely.
•
Vent connector and vent pipe must be in place, slope
upward at least 1/4 inch per foot and must be
physically sound, without holes or excessive corrosion.
•
All venting components including vent connector, vent
pipe, chimney and vent cap must be clear and free of
obstructions.