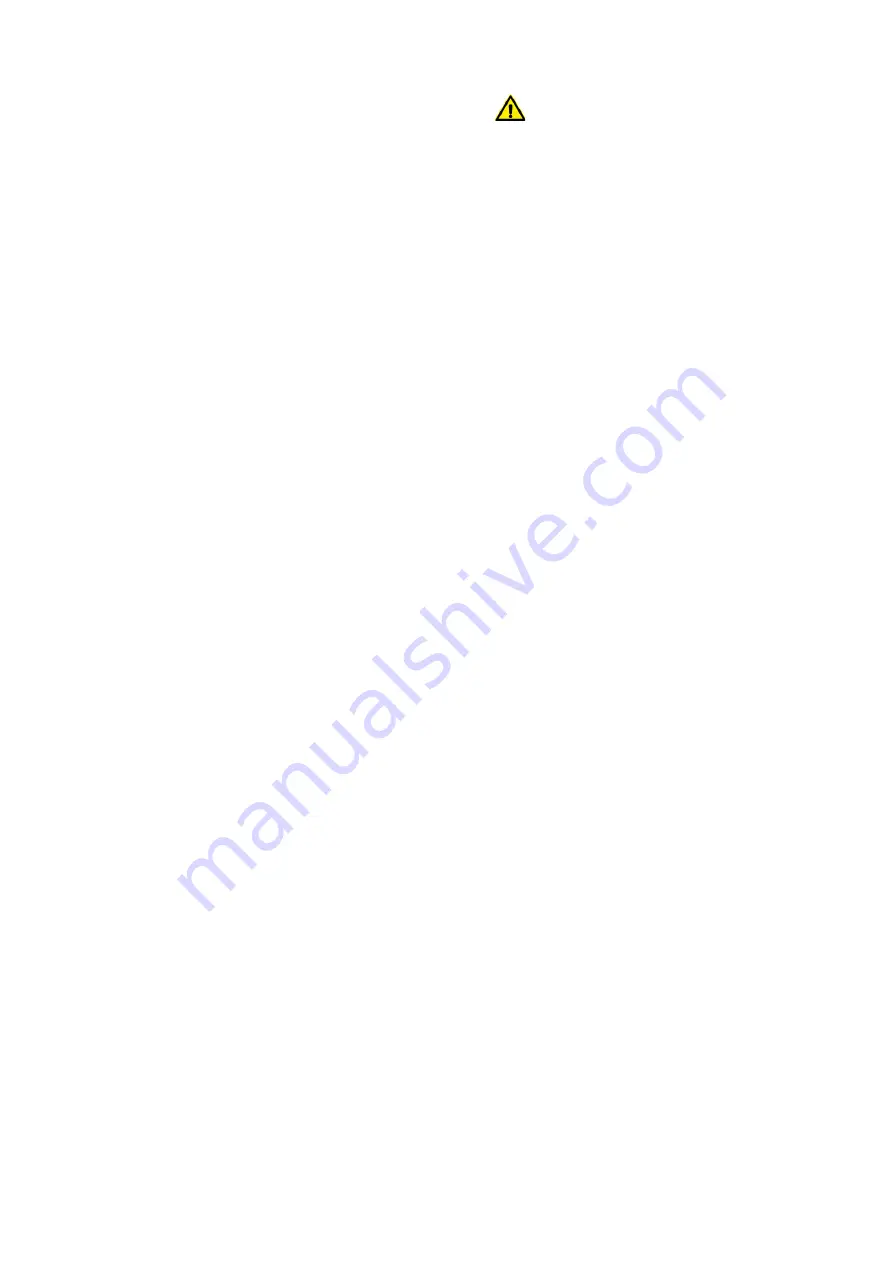
English
36
WILO SE 12/2019
7.4.2 Hydraulic connection
Connect the following circuits to pumping tank or
to priming tanks, by respecting the requirements
imposed by standard:
• Flow rate metering circuit for the pump test. If the
return to the tank is not possible, plan draining
towards the mains drainage (see fig. 5).
• Recirculation pipes. The recirculation circuit is
used to prevent overheating and damage to
pumps that remain in operation when the level of
pressure in the system is reached and before they
are turned off manually by authorised personnel.
• Sprinkler supply circuit of the fire extinguishing
system room.
• Connect main pumps and jockey pump to the fire
extinguishing system in accordance with the EN
12845 standard and with installation diagram.
• Connect the jockey pump directly to the water
tank by using a suction pipe which is adequately
proportioned to avoid priming pump troubles.
• Check the tank of the jockey pump pre-inflation
and adjust it according to the value of pressure
which has to be maintained in the system accord-
ing to the instructions written on the tank or in its
instruction manual.
7.4.3 Protection of the system
• The specific standard for fire extinguishing sys-
tems includes protections against short-circuits
with the use of high breaking capacity fuses,
which allow the passage of initial current for elec-
tric motors start-up for a period longer than 20
seconds. These fuses are held inside the electric
pump control panels. No thermal protections for
the main fire extinguishing pumps are provided.
• Thermal protection against overload of jockey
pump is installed inside its control box. It must be
calibrated at a value slightly higher than the
absorbed or nominal current (in) for the motor.
• Standard does not envisage protection against
lack of water of pumps. In case of emergency,
pumps must use all the available water of tanks to
extinguish fire.
• If diesel engines are present, the diesel engine
electronic control panel manages engine operat-
ing parameters and possible alarms. For more
information concerning diesel engine boxes, see
the specialised instruction manual of the control
panel.
Advise for installation
• According to the type of installation planned by
the project, the booster can correctly operate if
these following points are checked:
• pipes are positioned in such a way as to avoid air
accumulation.
• suction pipes between the intake point and the
pumping has to be as shortest as possible. Its
diameter must be suitable and equal or exceed
the minimum required to maintain the maximum
speed as indicated by the EN 12845 standard
• pipes do not have leakages or air infiltration
CAUTION! Risk of malfunction of the pump!
Valves or gate valves must not be directly
installed on the pump suction.
• Include an eccentric cone as indicated by the EN
12845 standard
7.4.4 Unit with positive head
[Fig. 6a - 6b] (As defined in EN 12845, point
10.6.2.2)
• Check the minimum level given for the storage
tanks or the minimum historical level for virtually
inexhaustible tanks in order to agree the condi-
tions for installation of the unit.
• Ensure that the diameter of the suction pipes is
not less than DN 65, and check if the maximum
suction speed does not exceed more than 1.8 m/s.
• Check if the NPSH available on the suction side of
the pump is at least 1 meter higher than the NPSH
required for flow rate and at the max water tem-
perature.
• Fit a strainer outside the water tank on the suction
pipes, having a diameter measuring at least 1.5
the nominal diameter of the pipe, and that does
not allow the passage of parts bigger than 5mm in
diameter.
• Install a gate valve between the strainer and the
water tank.
7.4.5 Unit with suction lift
[Fig. 7] (as defined in EN 12845, point 10.6.2.3)
• Check the minimum level given for storage tanks,
or the minimum historical level for virtually inex-
haustible tanks.
• Ensure a diameter of the suction pipes equal or
higher than DN 80, and check if the max suction
speed does not exceed 1.5 m/s.
• Check if NPSH available on the suction side of the
pump is at least 1 meter higher than the NPSH
required for flow rate and at the max water tem-
perature.
• Include independent intake pipes for the pumps
equipped at the lowest point of the bottom valve.
• Fit a strainer on the suction pipes, before the bot-
tom valve. This strainer must be set up so that it
can be cleaned without having to empty the tank.
It must have a diameter measuring at least 1.5 the
nominal diameter of the pipe and does not allow
the passage of parts bigger than 5 mm in diame-
ter.
• The distance between the rotation axis of the
pump and the minimum water level must not
exceed 3.2 meters.
• Each pump must have automatic priming devices
in compliance with the requirements of EN 12845,
point 10.6.2.4.
Summary of Contents for SiFire EN 100/200-205-45 E
Page 2: ...Fig 1 Fig 2a A 2 2 E B C D ...
Page 3: ...Fig 2b Fig 3 21 25 26 13 11 12 19 15 22 27 20 24 23 2 1 14 4 16 7 5 6 10 18 17 9 9 10 8 3 ...
Page 4: ...Fig 4 Fig 5 ...
Page 5: ...Fig 6a 3 5 D D 4 D 2 3 C min max 1 8 m s Fig 6b min 3 5 D D 4 D max 2 m 2 3 C max 1 8 m s ...
Page 6: ...Fig 7 Fig 8 max 3 2 m min A B C D 2 4 5 6 3 8 7 1 ...
Page 7: ...Fig 9a Fig 9b A B C D 800 800 800 ...
Page 8: ...Fig 1a Fig 9a variant Fig 9b variant A B C D 800 800 800 ...
Page 9: ...Fig 10 Fig 11 1 2 1 2 1 ...
Page 10: ......