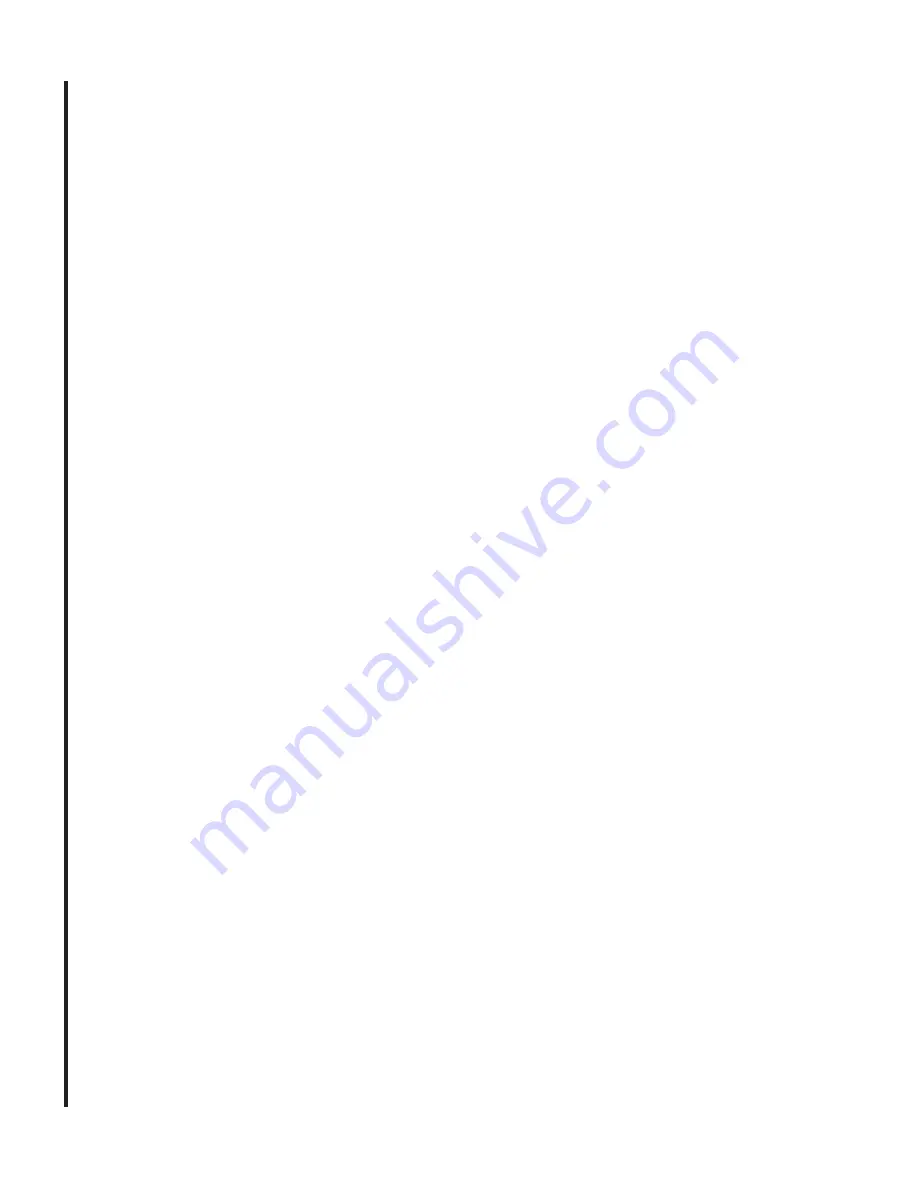
4
Wilton Abrasive Finishing Machines are available in three
different configurations: disc, belt, and combination disc
and belt. Each configuration is a rugged, heavy-duty
machine designed for maximum high production work in
an industrial environment.
The speed of stock removal and the quality of finish
achieved is determined largely by the aggressiveness of
the abrasive disc or belt mounted on the machine. With
very aggressive grits, these machines are typically con-
sidered grinding machines. With very fine grits, these
machines are typically considered sanding machines.
Whatever you call them, and however you use them, the
instructions in this manual will help you use them safely
and productively.
You will note there are several types of electrical sys-
tems available for these machines. All of these systems
are equally effective in providing power to the grinding
mechanism -- however, local codes and the type of envi-
ronment in which the machine is used will often be a
factor in your choice of system.
Instructions in this manual assume that you are using
one of the Model 4200A series Belt and Disc machines.
If you have a disc only, or belt only machine, you can
bypass those instructions which do not apply to you.
Machine and Manual Overview