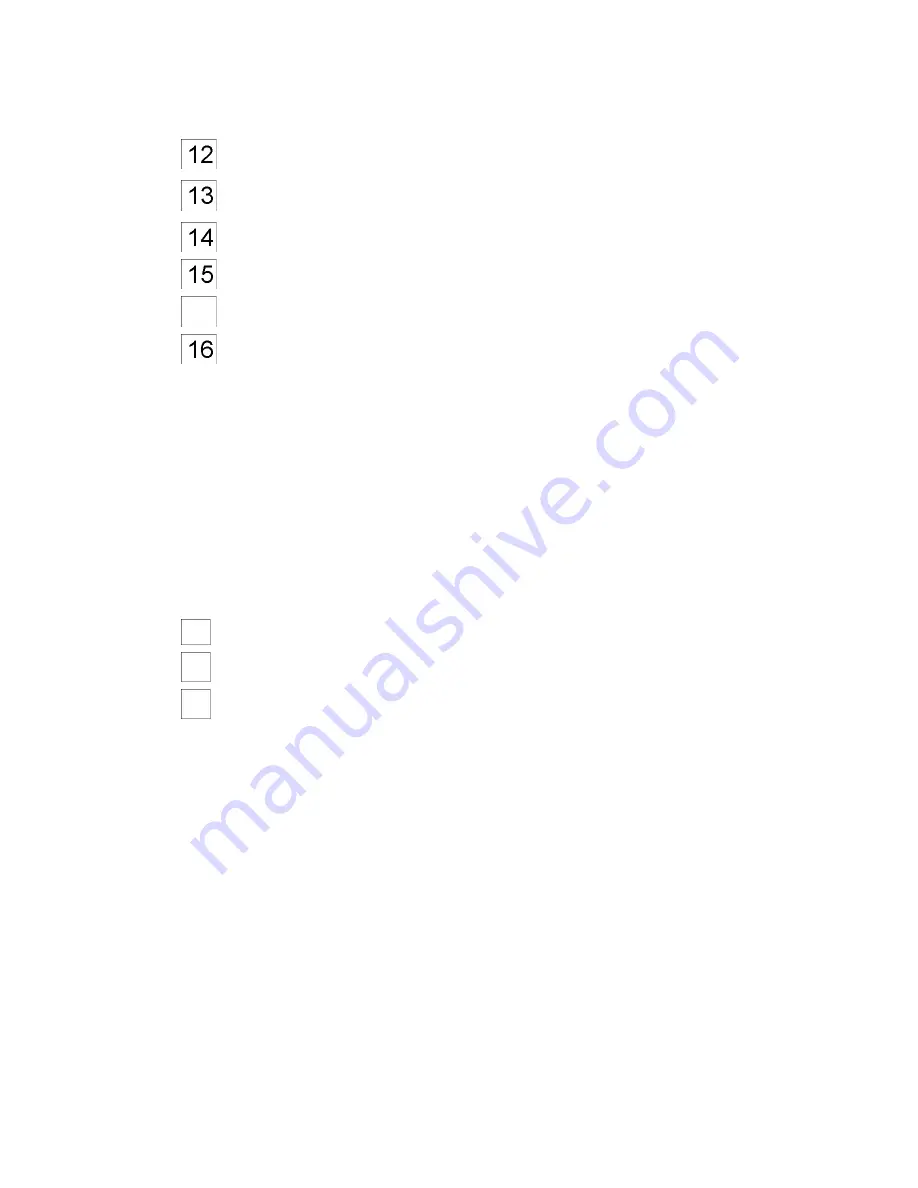
13
Procedures (continuation)
Unplug the circulating pump
Pull off the waste water hose that is connected to the upper
distributor
Loosen clamp at the collector; do not remove it
Unscrew the collector and take it out
Disconnect the circulating pump of the collector
Attach a new o-ring seal
Installation of the new collector
The installation is carried out in reverse order. At the same time a new
pump wheel is to be installed. The pump wheel has a left-handed
thread.
After the assembly:
Carry out a function test
Ventilate the dosing devices
Carry out a safety test according to VDE 0701
Summary of Contents for UC-L
Page 1: ...Winterhalter Undercounter Dishwashers UC Series Repair manual ...
Page 10: ...8 Exchange collector ...
Page 12: ...10 Exchange collector continuation ...
Page 14: ...12 Exchange collector continuation ...
Page 16: ...14 Exchange boiler heating element ...
Page 18: ...16 Exchange boiler ...
Page 22: ...20 Exchange tank heating element ...
Page 24: ...22 Exchange pump head dosing device Fluidos ...
Page 26: ...24 Exchange dosing device Fluidos ...
Page 28: ...26 Exchange integrated water softener ...
Page 30: ...28 Exchange integrated water softener continuation ...
Page 32: ...30 Exchange heat exchanger radial fan ...
Page 34: ...32 Exchange heat exchanger radial fan continuation ...
Page 46: ...44 ...
Page 47: ......