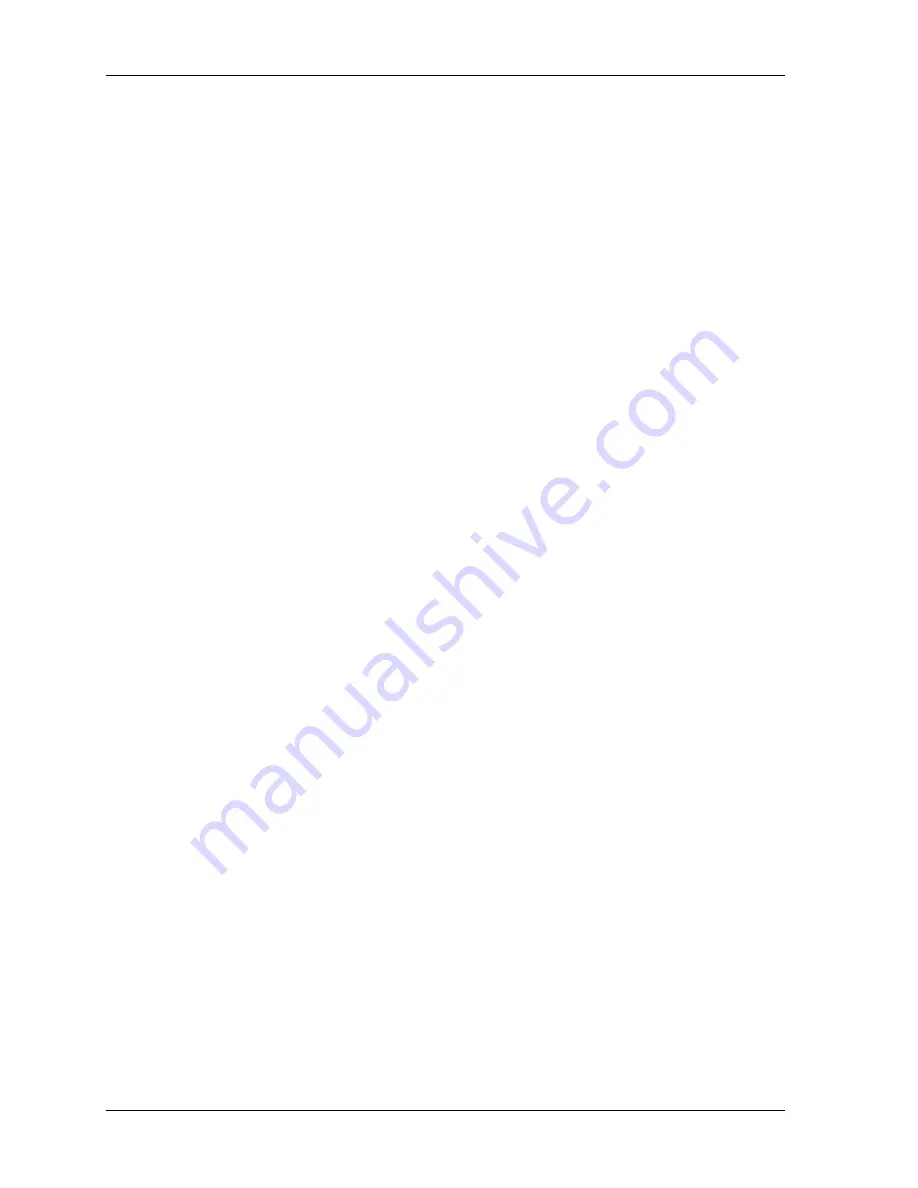
1143100
SmartPAC PRO User Manual
28
Chapter 1 – Introduction to SmartPAC PRO
Resolver-based Operation
For timing, the SmartPAC PRO uses a rugged and reliable resolver driven 1:1 with the press’s
crankshaft. The resolver constantly reports the crankshaft position to the SmartPAC PRO, enabling it
to create timing signals that are accurate to within 2/3 of a degree of rotation.
SmartPAC PRO Settings
You can make the following settings using the screen on the SmartPAC PRO:
•
Assign tool names/numbers.
Settings for each tool are stored by tool number or name, which
you assign to identify and access the tool when you want to program or load it.
•
Load settings by tool name/number
.
SmartPAC PRO saves all settings in its electronic
memory. To use tool settings again, you recall them by selecting the tool name or number from
the Tool Manager. SmartPAC PRO retains settings for thousands of tools.
•
Protect settings with lockout and optional password security
.
You can lock many of the
settings in Run mode, preventing anyone without access to the PROG/RUN keyswitch from
altering settings. You can also require that the user enter a password in order to change settings.
•
Set Brake Monitor.
You set the brake monitor stop time limit to provide a warning when the
brake needs service. When the stop time limit is exceeded, the brake monitor disables the press,
alerting you that your brake requires service. In addition, the Brake Warning LED on the
SmartPAC PRO front panel flashes when press stopping time approaches within 10msec of the
stop time limit, allowing you to schedule maintenance.
•
Set counters
. SmartPAC PRO’s counters keep track of the number of strokes made by the press,
the number of good parts produced, the total hits on the die. The good parts counter increments
only when the die protection or tonnage monitoring option does not generate a fault. Batch
counters can be set to top-stop the press their presets are reached. SmartPAC PRO is able to keep
an accurate parts count when multiple parts are produced on each stroke or when multiple strokes
are required to produce one part..
•
Review recent errors
. SmartPAC PRO’s Error/Event Log feature displays the 200 most recent
errors and events that have occurred at the press. Errors (i.e., incidents that cause the press to
stop) are shown along with the stroke count and crankshaft angle at which the error occurred.
Events, such as tool changes, are displayed with the date, time, and stroke count. The Error Log is
accessible from the Main Run Menu.
•
Set timing for sensor inputs (DiProPAC Only).
You can specify how you want installed
sensors to monitor press operation. Up to 32 sensors can be used, allowing detection of
malfunctions such as stock buckling, misfeeds, and improper part ejection.
•
Set timing for cam channels (ProCamPAC Only).
You can specify the crankshaft angle at
which to activate your feed pilot release, assembly operations, air cylinders, transfer devices,
lubricators, air blow-off, cut off, loader/unloader controls, and other equipment that requires
precise synchronization with the press. You can also assign a name to each cam channel.
Summary of Contents for SmartPAC PRO
Page 1: ......
Page 2: ......
Page 4: ......
Page 6: ......
Page 20: ......
Page 22: ......
Page 24: ......
Page 42: ...1143100 SmartPAC PRO User Manual 42 Chapter 1 Introduction to SmartPAC PRO ...
Page 142: ...1143100 SmartPAC PRO User Manual 142 Chapter 4 SmartPAC PRO Program Mode ...
Page 200: ...1143100 SmartPAC PRO User Manual 200 Chapter 6 Using DiProPAC Die Protection Optional ...
Page 222: ...1143100 SmartPAC PRO User Manual 222 Chapter 7 ProCamPAC Instructions ...
Page 254: ...1143100 SmartPAC PRO User Manual Appendix C SmartView Remote Viewing and E mail Setup 254 ...
Page 280: ...SmartPAC PRO User Manual 1143100 280 Appendix C Reporting Downtime and Scrap to SFC ...
Page 290: ...SmartPAC PRO User Manual 1143100 290 Index Y yellow fault 232 yellow sensor 169 ...
Page 292: ......
Page 294: ......
Page 296: ......
Page 298: ......
Page 300: ......
Page 301: ......
Page 302: ......
Page 303: ......
Page 304: ......
Page 305: ......
Page 306: ......
Page 307: ......
Page 308: ......
Page 309: ......
Page 310: ......
Page 311: ......
Page 312: ......
Page 313: ......
Page 314: ......
Page 315: ......
Page 316: ......
Page 317: ......
Page 318: ......