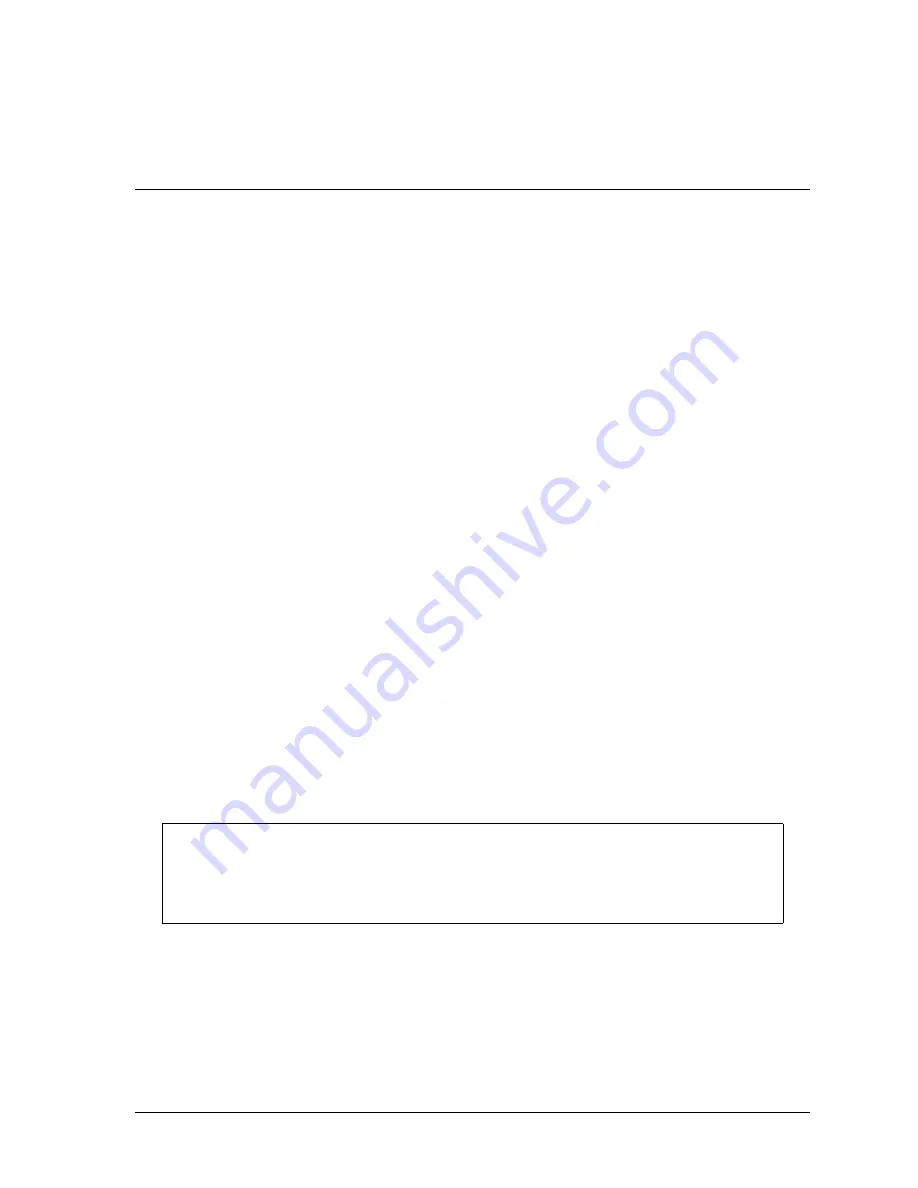
Reporting Downtime and Scrap to LETS
G-1
Appendix G. Reporting Downtime and
Scrap to LETS
This appendix shows you how to report press downtime from your SmartPAC 2 control to
Wintriss’s Line Efficiency Tracking Software (LETS). The appendix discusses the six
machine states to which LETS logs press time, explains the downtime reporting features of
SmartPAC 2, shows you how to set up SmartPAC 2 to report downtime to LETS, and
provides instructions for reporting downtime.
The appendix also shows you how to use the scrap counter on the SmartPAC 2 Counters
screen in Run mode to report scrap to LETS and how to adjust the Good Parts count that is
reported to LETS.
SmartPAC’s downtime- and scrap-reporting features are available only on SmartPAC 2
versions 4.59 or higher; in addition, the LETS firmware option must be installed.
Machine States to Which LETS Logs Press Time
LETS logs all elapsed time at each press to one of six categories called machine states. The
sum of all the times assigned to these machine states for an individual press is the number of
hours in a production day (e.g., 12 hours, 24 hours, etc.). LETS selects the machine state to
which to log press time on the basis of downtime reporting and other information it receives
from SmartPAC 2. Machine states are differentiated as follows:
•
Running Time–Press is running and making parts
•
Idle Time–Press is stopped, no SmartPAC error has occurred, and the reason the press is
stopped has not been documented in SmartPAC 2
•
Unplanned Downtime–Press is stopped due to a SmartPAC 2 error, or if the press is stopped
for another reason, that reason has been documented in SmartPAC 2 as a downtime reason
other than Planned Downtime or Tool Change
•
Planned Downtime–Press is stopped, and the reason has been documented in SmartPAC 2
as Planned Downtime
•
Changeover Time–Press is stopped, and the reason has been documented in SmartPAC 2 as
Tool Change
•
Offline Time–Press is stopped because there is no power to the press or the network is
down
The Planned Downtime machine state should only be assigned for lunch and coffee
breaks, meetings, training, etc. Planned Downtime is not used in calculating Overall
Equipment Effectiveness (OEE) and, therefore, does not reduce the OEE value.
NOTICE
Summary of Contents for SmartPAC2
Page 21: ...1126700 SmartPAC 2 User Manual xviii Table of Contents ...
Page 143: ...1126700 SmartPAC 2 User Manual 4 46 Initialization Mode ...
Page 197: ...1126700 SmartPAC 2 User Manual 5 54 Program Mode ...
Page 233: ...1126700 SmartPAC 2 User Manual 6 36 Run Mode ...
Page 245: ...1126700 SmartPAC 2 User Manual 7 12 Fault Messages ...
Page 271: ...1126700 SmartPAC 2 User Manual B 12 Updating SmartPAC 2 Firmware ...
Page 309: ...1126700 SmartPAC 2 User Manual E 6 Replacing SmartPAC 2 PC Board ...
Page 379: ......
Page 380: ......
Page 381: ......
Page 382: ......
Page 383: ......