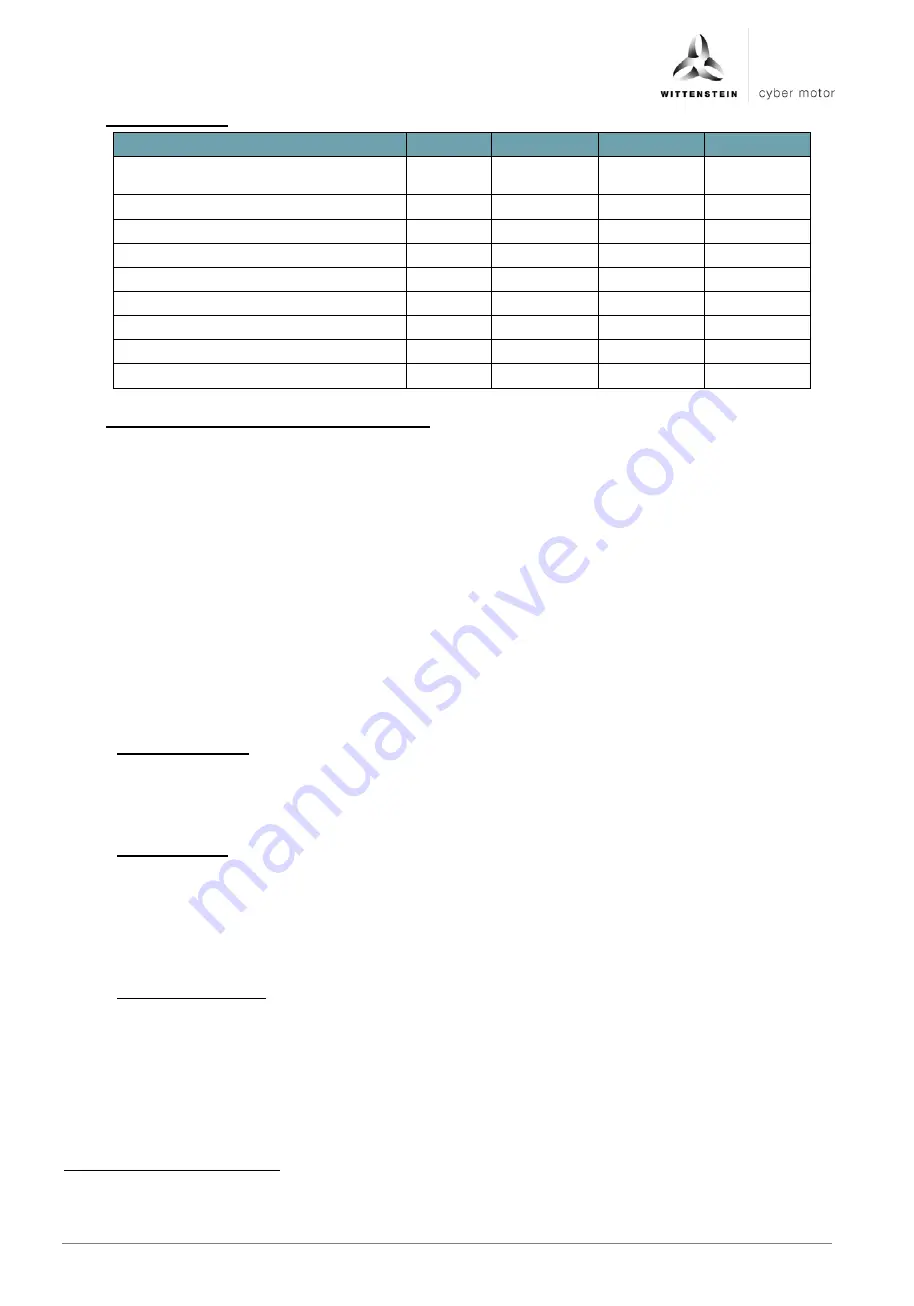
Operation Manual simco
®
drive
en-10
4022-D033499
Revision: 11a
3.3 Electrical data
Electrical data
Unit
SIM2002D
SIM2010D
SIM2015D
Nominal supply voltage,
intermediate circuit
V DC
48
48
48
Nominal power
W
125
500
750
Maximum intermediate voltage
V DC
16.. 56
16.. 56
16.. 56
Logic power supply
V DC
24 ± 10%
24 ± 10%
24 ± 10%
Current consumption logic supply
mA DC
< 250
< 250
< 250
Nominal output current of drive
Arms
2,5
10
1
15
1
Peak output current of the drive
Arms
5
20
30
Switching frequency of the drive
kHz
8 .. 32
8 .. 32
8 .. 32
Electrical rotary field frequency
Hz
0 .. 1000
0 .. 1000
0 .. 1000
3.4 Description of the simco
®
drive series
WITTENSTEIN simco
®
drive is an intelligent drive amplifier series for sine-commutated
servo motors with a continuous power of up to 750 W and peak output of up to 1.5 kW.
The different types of housing in the simco
®
drive series allow for a high degree of flexibility
in installation.
The housing with protection class IP65 enables decentralized assembly, so that the drive
technology can be integrated modularly and flexibly in the machine structure, reducing
wiring. The drive amplifier with protection class IP20 on the other hand is designed for
central installation in the control cabinet.
Depending on the device version, CANopen/DS402, EtherCAT with CoE, PROFINET RT /
IRT, Ethernet/IP IO or SERCOS III with FSP Drive are available as communication
interfaces.
The intelligence is reflected in the wide range of encoder interfaces, such as ENDAT 2.2,
BISS C or Resolver, high resolution current regulation and event logging with real-time
clock.
Intuitive startup and diagnosis is possible using a PC-based, graphic user interface.
3.4.1 Integrated safety
−
Comprehensive diagnostic functions to protect the drive amplifier, such as
overvoltage, overcurrent, short circuit or ground fault.
−
Temperature monitoring of the drive amplifier, motor and optionally the gearhead.
3.4.2 Digital control
−
Digital d-q current controller (PI) with a sampling rate of up to 32 kHz
−
Digital position and speed controller (PI) with a sampling rate of 8 kHz
−
Feed forward control of speed and current possible
−
Adjustable pulse width modulation with a clock rate of 8 .. 32 kHz
−
Anti-windup structure for all controllers
3.4.3 Inputs and outputs
−
4 programmable galvanically isolated digital inputs, 24 V
−
2 programmable galvanically isolated digital outputs, 24 V (short-circuit proof)
−
Output for controlling a 24 V holding brake
1
T
he nominal output current of the output stage is achieved at the installation positions described in chapter 5 and
a PWM frequency of 8 kHz. The nominal output current may reduce considerably in the case of other mounting
positions or PWM frequencies.
Summary of Contents for SIM2002D-CCSA-CA00-0000-0000
Page 1: ...4022 D033499 Revision 11a simco drive SIM2002D SIM2010D SIM2015D Operating Manual...
Page 2: ......
Page 51: ......